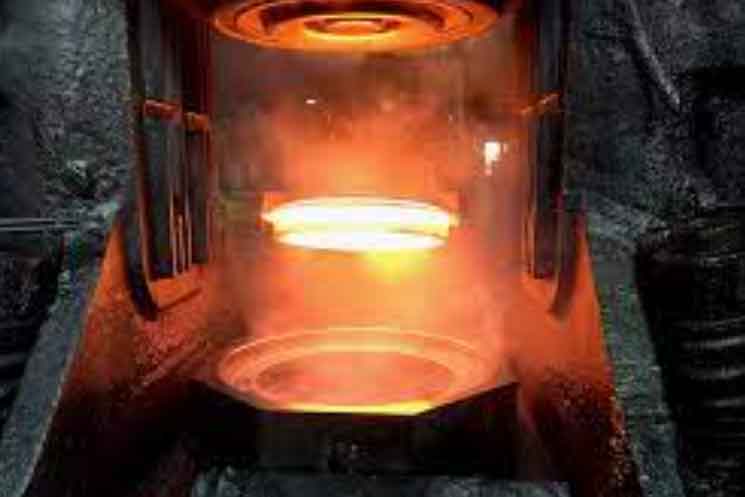
When it comes to gear manufacturing, ensuring precision and reliability is crucial to the performance and longevity of the gears. Gears are essential components in various industries, including automotive, aerospace, robotics, and many others. To forge quality gears, several key factors need to be considered throughout the manufacturing process. Here are some important steps to ensure precision and reliability in gear manufacturing:
Design and Engineering:
The gear manufacturing process starts with proper design and engineering. This involves understanding the specific requirements of the application, such as torque, speed, load capacity, and operating conditions. The gear design should be optimized for efficiency, strength, and noise reduction. Computer-aided design (CAD) and simulation software can help in creating accurate gear models and performing virtual testing before actual manufacturing.
Material Selection:
Choosing the right material for gears is critical. Factors such as strength, durability, wear resistance, and heat treatment capability should be considered. Common materials for gears include alloy steels, stainless steels, and various types of heat-treated steels. The material should be carefully selected to meet the performance requirements and expected service life of the gears.
Machining and Forming Processes:
Gear manufacturing involves various processes, such as machining and forming, to shape the gears accurately. CNC (Computer Numerical Control) machines are commonly used for precise cutting, milling, and shaping of gears. The machines should be properly calibrated and maintained to ensure accurate dimensions and tight tolerances. Forging, casting, or powder metallurgy techniques can also be employed depending on the type and size of the gear.
Heat Treatment:
Heat treatment plays a vital role in enhancing the mechanical properties of gears. Processes such as carburizing, quenching, and tempering are commonly employed to increase the surface hardness, improve wear resistance, and provide the necessary core toughness. Precise control of temperature, time, and cooling rates during heat treatment is crucial to achieve the desired material properties.
Finishing Operations:
After the core manufacturing processes, finishing operations are performed to improve the surface finish, accuracy, and noise characteristics of the gears. Processes like grinding, honing, lapping, or superfinishing can be utilized to achieve the required gear tooth profile and surface quality. Careful attention should be given to the tolerances and tooth geometry to ensure proper meshing and smooth operation.
Quality Control and Inspection:
Throughout the gear manufacturing process, quality control and inspection are essential. Advanced measurement techniques like coordinate measuring machines (CMM), gear analyzers, and profile testers can be employed to verify dimensional accuracy, tooth profile, and runout. Non-destructive testing methods, such as ultrasonic or magnetic particle inspection, can be used to detect internal defects.
Lubrication and Maintenance:
Proper lubrication is crucial for the smooth operation and longevity of gears. The selection of appropriate lubricants and regular maintenance are necessary to minimize friction, wear, and noise. Following manufacturer guidelines for lubrication intervals and ensuring adequate lubricant supply are important factors in ensuring gear reliability.
Continuous Improvement and Quality Assurance:
Gear manufacturers should emphasize continuous improvement and quality assurance. This includes analyzing performance feedback, identifying areas for improvement, and implementing measures to enhance gear quality, efficiency, and reliability. Close collaboration between design, manufacturing, and quality assurance teams is essential to optimize gear manufacturing processes.
By following these steps and maintaining strict quality standards, gear manufacturers can forge quality gears that meet the highest precision and reliability requirements. It is important to adhere to industry standards, employ skilled personnel, and utilize advanced technologies to ensure consistent quality and customer satisfaction.