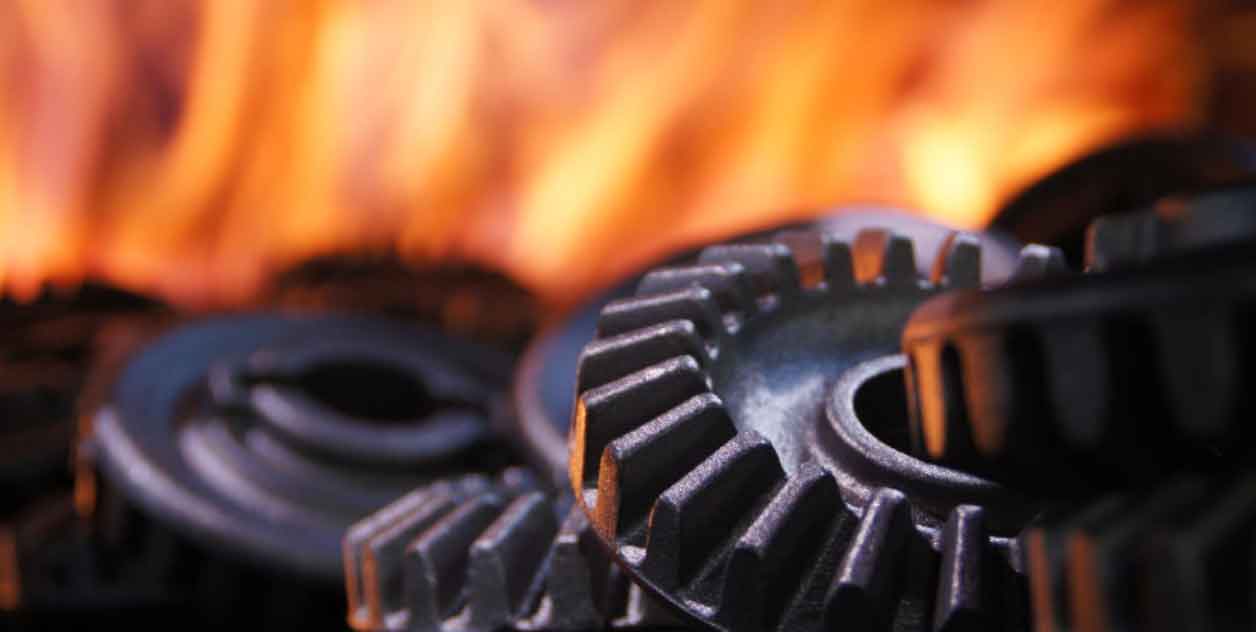
The production of quality gears requires a combination of advanced techniques, precision engineering, and meticulous craftsmanship. Gear forgings, in particular, exemplify the artistry and skill involved in creating gears of exceptional quality. This article delves into the art of gear forgings, highlighting the key aspects that contribute to the production of high-quality gears.
I. Design Expertise:
Creating quality gears begins with a solid understanding of gear design principles. Design engineers with expertise in gear geometry, load analysis, and performance requirements play a crucial role in ensuring the functionality and efficiency of the gears. They consider factors such as tooth profiles, gear ratios, load distribution, and backlash during the design process, setting the foundation for successful gear forgings.
II. Material Selection and Metallurgy:
The choice of material for gear forgings significantly impacts their performance and longevity. Metallurgical expertise is essential in selecting the right material that exhibits the desired properties, such as strength, durability, and resistance to wear and fatigue. Metallurgists consider factors like alloy composition, heat treatment requirements, and the interaction between the material and the operating environment to ensure optimal gear performance.
III. Forging Process Optimization:
The forging process itself is a critical aspect of creating quality gears. Skilled forge technicians and process engineers work together to optimize the forging parameters, including temperature, deformation, and strain rate, to achieve the desired material properties and shape. Proper control of these parameters ensures uniform deformation, minimal internal defects, and enhanced grain structure, resulting in gears with excellent strength and integrity.
IV. Precision Machining:
After the forging process, precision machining further refines the gear forgings, ensuring accurate tooth profiles, smooth surfaces, and precise dimensions. CNC machining centers equipped with specialized gear-cutting tools and grinding machines are utilized to achieve the required tolerances and surface finishes. Highly skilled machinists operate these machines, meticulously following the design specifications to create gears with exceptional precision.
V. Heat Treatment and Surface Enhancement:
Heat treatment plays a crucial role in the final properties of the gears. Heat treat experts carefully control the heating, quenching, and tempering processes to achieve the desired hardness, strength, and toughness. Additionally, surface enhancement techniques, such as shot peening or nitriding, may be employed to improve surface hardness, wear resistance, and fatigue life. The expertise of heat treat specialists ensures that the gears attain the necessary metallurgical properties for optimal performance.
VI. Quality Control and Inspection:
Ensuring the quality of gear forgings involves rigorous inspection and quality control measures. Non-destructive testing techniques, such as magnetic particle inspection and ultrasonic testing, are employed to detect any internal defects or discontinuities. Dimensional inspections, hardness testing, and metallurgical analysis are conducted to verify compliance with specified standards. Skilled inspectors meticulously evaluate the gears to ensure they meet the required quality standards.
VII. Continuous Improvement and Innovation:
The art of gear forgings is an ever-evolving process. Manufacturers invest in research and development to improve the manufacturing techniques, explore new materials, and enhance gear performance. They strive for continuous improvement in terms of efficiency, reliability, and overall gear quality. Through innovation, manufacturers push the boundaries of gear forging technology, driving advancements in gear manufacturing as a whole.
Forging quality gears is an intricate art that requires expertise, precision, and a deep understanding of gear design and manufacturing processes. The art of gear forgings encompasses design expertise, material selection, forging process optimization, precision machining, heat treatment, quality control, and a commitment to continuous improvement. By mastering this art, manufacturers can produce high-quality gears that excel in performance, durability, and reliability, meeting the stringent demands of various industries and applications.