The external teeth of the part are spur gears and the internal teeth are involute spline teeth. Three forming process schemes are designed according to one-step forming and multi-step forming of internal and external teeth.
Scheme I: simultaneous extrusion of internal and external teeth – finishing of external teeth
Fig. 1 is the process schematic diagram of scheme 1. Considering that if the internal and external teeth can be formed at one time, the forming efficiency of the parts will be significantly improved, the process scheme is designed to form the internal and external teeth in one step. During cold extrusion forming, the preformed annular blank after lubrication treatment is put into the outer tooth die sleeve, the blank is in contact with the head of the outer tooth die, the spline punch goes down, and the front-end guide area is inserted into the inner hole of the blank until the involute spline tooth head contacts the blank, the upper and lower ends of the blank are extruded at the same time, resulting in plastic deformation, and the deformation of the formed inner tooth is smaller than that of the formed outer tooth When the forming load is low, the spline punch first completes the extrusion forming of the internal teeth. The spline punch continues to go down until the step surface contacts the blank, and the blank is extruded to complete the external tooth forming. The spline punch stops downward, returns and exits the external tooth concave model cavity, and at the same time, the lower ejector ejects the whole part. Turn the upper end face of the part formed with internal and external teeth at the same time, put it into the through finishing die, and push the part through the shaping area with a simple disk flat punch with a large diameter less than the diameter of the tooth root circle of the external tooth, so as to complete the finishing and improve the accuracy of the spur gear of the external tooth.
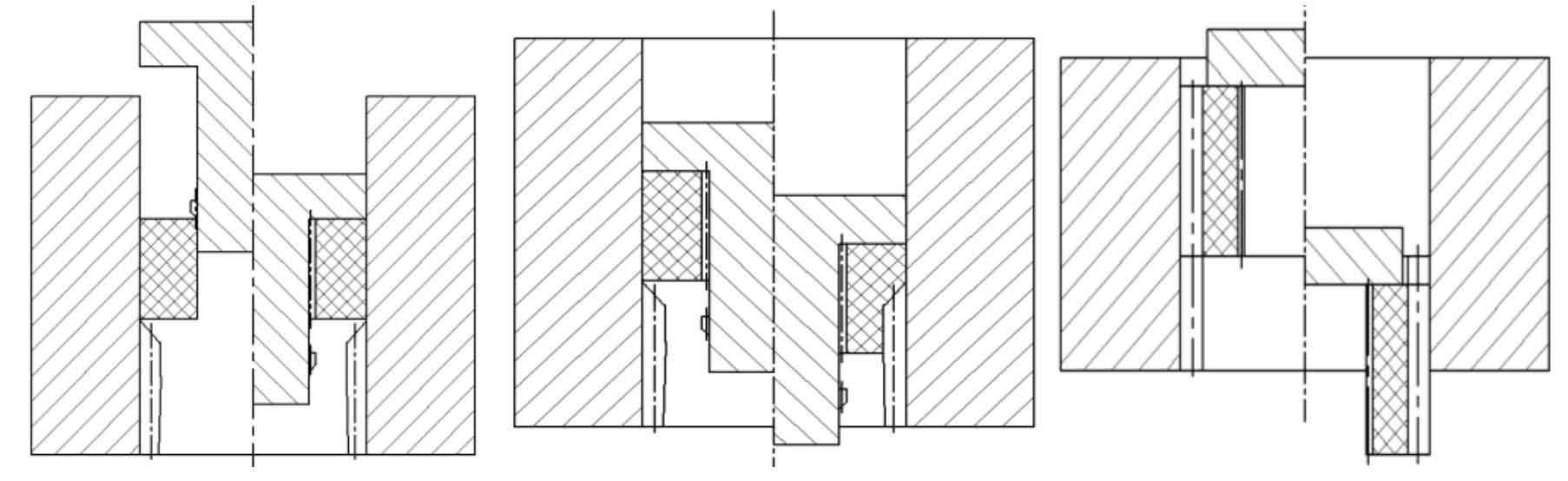
Scheme 2: continuous cold extrusion of external teeth – finishing of external teeth + extrusion of internal teeth
It is difficult to form internal and external teeth at the same time, which may not be easy to achieve. The precision of spur gear with external teeth of formed parts is required to be high. After external teeth are extruded, the precision of spur gear must be improved through finishing in order to meet the requirements of assembly and use. The forming of sun gear must complete three main processes: external tooth forming, internal tooth forming and external tooth finishing. The internal tooth forming and external tooth finishing are both forming methods with relatively small deformation and have little influence on each other. Considering the combination of internal tooth forming and external tooth finishing, the process scheme of extruding the external teeth first, then finishing the external teeth and extruding the internal teeth at the same time is designed. When the external teeth are extruded separately, the through extrusion female die is designed to transfer the torque in the form of blank “pressing part”, so as to realize continuous extrusion and improve the production efficiency. Moreover, the upper die does not need to process the supporting tooth structure, and the structure of ordinary flat punch can be adopted, which simplifies the upper die structure and reduces the processing and manufacturing cost. Mandrel constraint is required during external tooth forming to ensure that the dimensional accuracy of inner hole can meet the requirements during subsequent internal tooth forming.
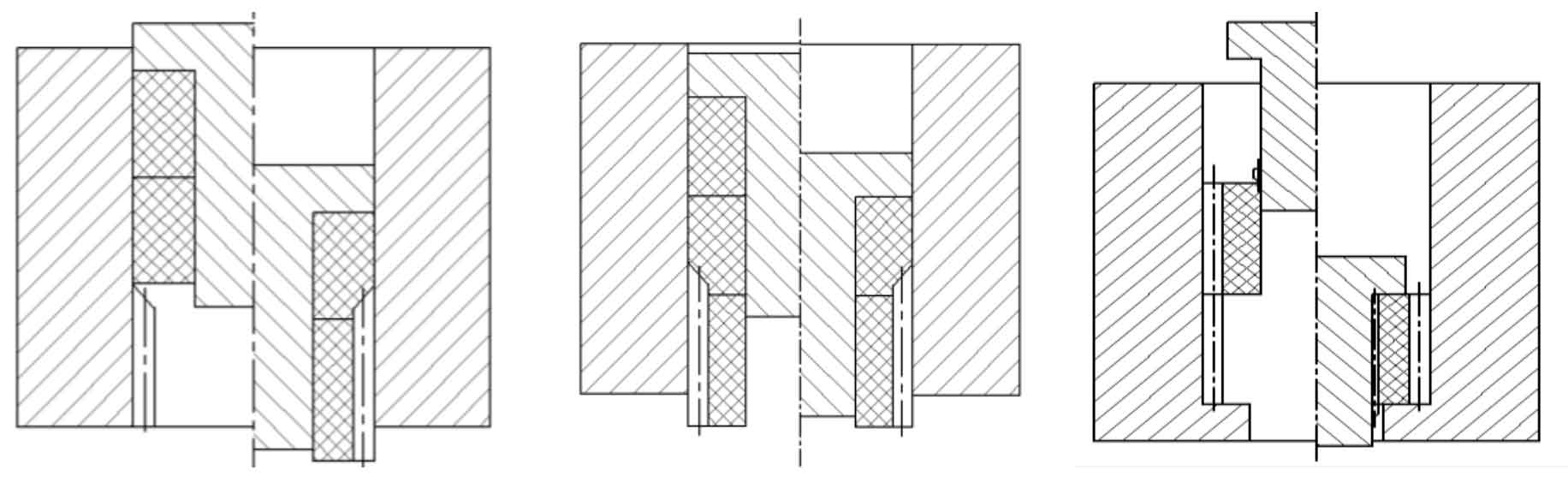
Fig. 2 is the process schematic diagram of scheme 2. When cold extruding the external teeth, two prefabricated annular blanks that have been lubricated are superimposed in the sleeve of the external tooth concave die, the mandrel of the extrusion flat punch is inserted into the inner hole of the blank until the step surface contacts the upper blank, the extrusion flat punch goes down, the lower blank is plastically deformed by the load transmitted by the upper blank, and the blank metal flows into the external tooth concave die to form the external teeth, When the extrusion flat punch reaches the set stroke, it returns. At this time, the blank at the upper end just enters the toothed die, and the blank at the lower end completely enters the toothed die but does not exit the die. Continue to add a blank in the die sleeve, extrude the blank at the lower end, extrude the blank at the top, extrude the middle blank to form the outer teeth, and extrude the lower blank to exit the die while the middle blank forms the outer teeth, After the extrusion flat punch reaches the set stroke downward, stop and return to complete a single continuous extrusion action. Put the part with only extruded outer teeth into the finishing die, insert the inner tooth punch with guide area into the inner hole of the part until the head of the inner tooth punch contacts the blank. The deformation of the outer tooth finishing is less than that of the inner tooth forming. First push the part to complete the outer tooth finishing of spur gear, and then the part is fixed at the bottom of the finishing die, The internal tooth punch continues to go down to complete the internal tooth forming, and then returns to exit the finishing model cavity. At the same time, the lower ejection will eject the whole spur gear.
Scheme 3: continuous cold extrusion external teeth – finishing external teeth – machining internal teeth
External tooth forming, internal tooth forming and external tooth finishing are essential processes in the production and manufacturing of sun gear. Although the compound forming of the two processes can improve the production efficiency, it will also increase the forming difficulty. The second scheme is feasible in theory. Therefore, on the basis of scheme 2, we designed scheme 3: continuous cold extrusion of external teeth, finishing of external teeth, and then machining of internal teeth.
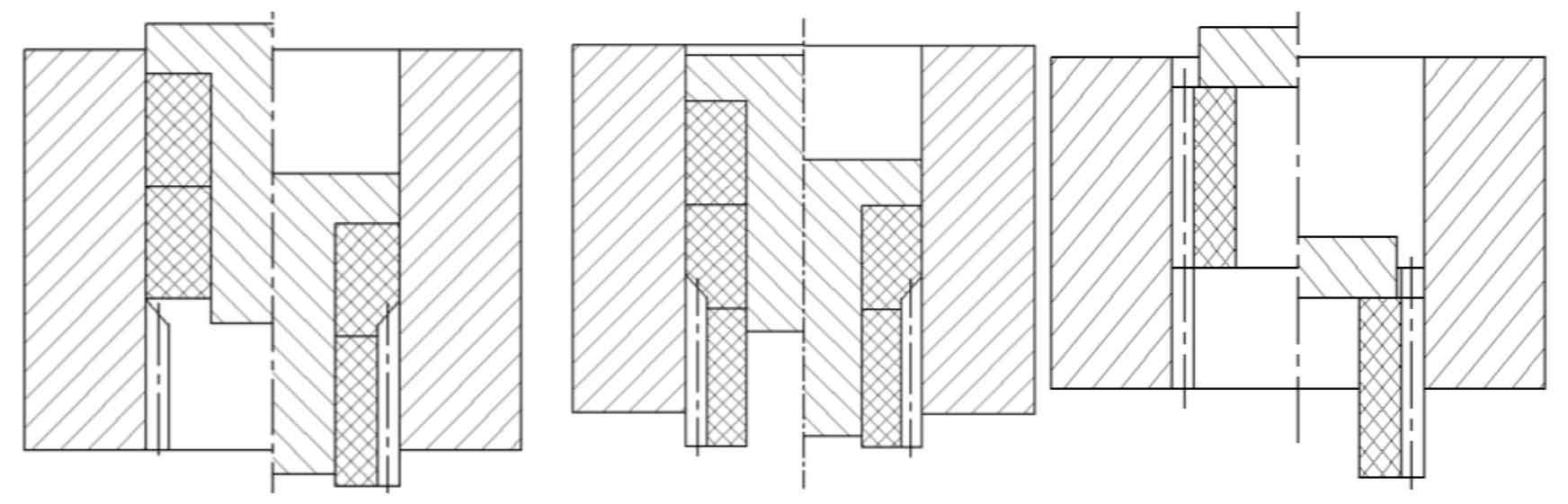
Fig. 3 is the process schematic diagram of scheme 3. The continuous cold extrusion forming process of external teeth is the same as scheme 2. Put the parts with only extruded external teeth into the through finishing die, and push the parts through the shaping area with a simple disk flat punch with a large diameter less than the diameter of the tooth root circle of external teeth to complete the finishing and improve the precision of spur gear of external teeth. Finish the finished parts, machine the end face and inner hole, and broach the spline inner teeth after heat treatment