Fatigue failure is one of the most important failure modes in the use of structures. In the process of using, it is found that there is an important problem in the fatigue failure of the structure, that is, when the frequency of the alternating load is consistent with or close to the natural frequency of a certain order and several orders of the structure, the structure will have resonance phenomenon, at this time, a certain excitation will produce greater response, so that it is easier to produce fatigue failure, The behavior of structural failure caused by resonance is called resonance fatigue.
In 1958, Crandall applied the theory of random vibration to the study of structural fatigue. In 1963, Crandall et al. First described the vibration fatigue as an irreversible vibration fatigue strength with damage accumulation under vibration load excitation. At the end of 1970s, Yao Qihang et al [4-5] put forward the concept of vibration fatigue, and then, together with Yao Jun, proposed that fatigue should be divided into static fatigue and vibration fatigue. Some studies show that the dynamic characteristics of the external excitation and the frequency response of the structure should be considered in the vibration fatigue analysis [6-8]. In engineering, vibration fatigue is divided into resonance fatigue and non resonance fatigue. Resonance fatigue is more related to component resonance or local resonance. Dynamic load excitation often causes fatigue fracture at the parts with large strain and defect or stress concentration in local resonance of structure [9]. Fatigue failure is caused by the joint action of local resonance and stress concentration of structure, This is also different from static fatigue analysis.
Gearbox device is one of the important equipment of high-speed EMU traction system, which is usually under the condition of high-speed and heavy load operation. The fatigue performance of its structure is directly related to the operation safety of high-speed train. In recent years, fatigue cracks appear in the gear box of a certain brand in the operation of train lines, which seriously threatens the operation safety of high-speed trains. Therefore, this paper takes this type of gear box as the research object, and makes statistics on the typical faults in the operation of the gear box, Based on the measured vibration acceleration signal and dynamic stress signal of the line, the vibration characteristics and dynamic stress response characteristics of the axle box and gear box under the two typical working conditions of high-speed straight line and low-speed straight line are analyzed, thus the wheel rail excitation related to the train operation speed is obtained, and compared with the natural frequency of the gear box. The analysis results show that: under the effect of wheel rail excitation, There is local resonance in the gearbox. The research lays a foundation for ensuring the safety of high-speed train operation and the new structural design of gear box.
1. Fracture analysis
The life of structural members is a function of local stress state and stress level, original manufacturing quality of structure, geometry and working environment of materials, etc. the failure mode and failure reason of members can be determined by fracture analysis of structure [11]. The gear box is of cast aluminum alloy structure. During the operation of high-speed train, the crack position of the upper box mainly occurs at the fixed code of the upper box sensor.
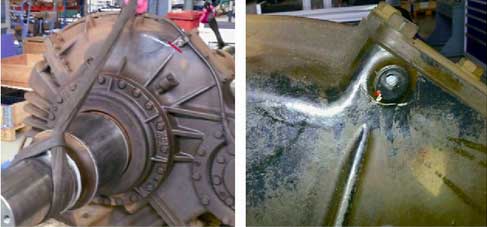
Through the macroscopic inspection of the crack fracture, it can be seen that the fracture crack has obvious fatigue characteristics – fatigue arc, which is formed in the fatigue crack growth stage and perpendicular to the crack growth direction, and is the macroscopic deformation trace along the line before the fatigue crack transient, as shown in Figure 2. Through a large number of fracture analysis of the failure gear box, it is known that the crack initiation point mainly occurs in the casting defects on the surface of the box body, such as surface pits, air holes, etc., and the casting defects such as air holes and shrinkage holes in the middle of the structure, which greatly reduces the bearing capacity of the gear box body.
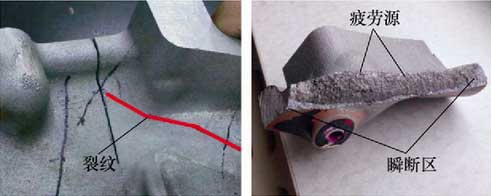
2. Crack statistics
The main failures of gearbox of high-speed EMU are oil leakage, high oil temperature in gearbox, foreign matters in gearbox, etc., but the main failure mode is fatigue crack of gearbox. According to statistics, since the first gearbox fatigue crack fault occurred in a high-speed EMU produced by a passenger car factory in June 2012, up to now, there have been more than 100 cumulative cracks in the gearbox, including 67 cracks near the upper box sensor fixing code. The figure shows the operation mileage when fatigue crack occurs on the upper box body. The maximum operation mileage is about 1.26 million km, the minimum operation mileage is about 95000 km, and the average operation mileage is about 523000 km.
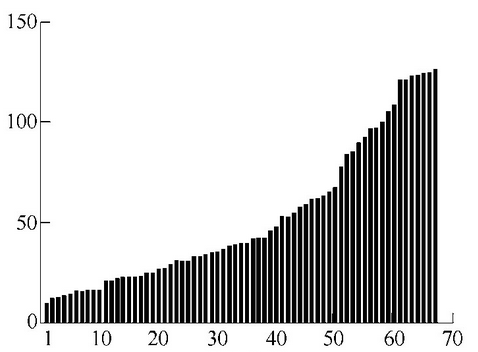