Abstract
This paper addresses the complexity of the topological surface of high reduction hypoid (HRH) gears. Utilizing the method of conjugate surface with identical tangent planes, the tooth surface model and ease-off surface of HRH gears are constructed. Kinematic parameters such as curvature parameters at contact points, entrainment velocity, and sliding-to-rolling ratio are obtained through analysis. Load, tooth stiffness, and deformation compatibility equations are established using the differential strip method for loaded tooth contact analysis (LTCA), yielding the distribution of load and contact stress on the tooth surface. Combined with the empirical formula for elastohydrodynamic lubrication (EHL) friction coefficient, issues related to instantaneous contact area distortion and EHL parameter calculation are resolved. The distribution laws of oil film thickness, friction coefficient, and friction power loss on the tooth surface are analyzed. The proposed LTCA, friction power loss analysis, and meshing efficiency calculation models are validated through transmission efficiency tests.
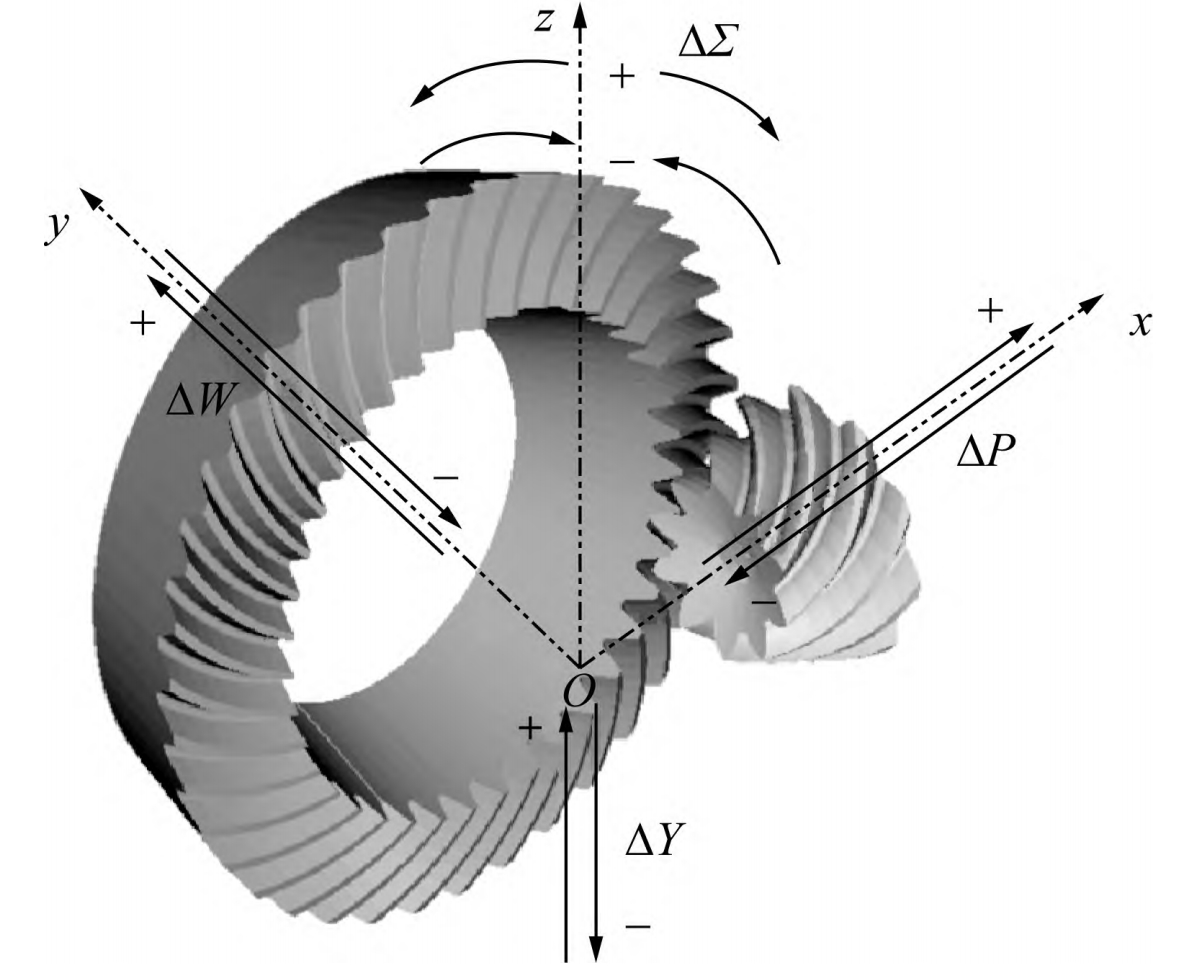
1. Introduction
Modern mechanical equipment places increasing demands on power density, efficiency, and low carbon emissions. As one of the core components in mechanical transmission, gears, particularly their meshing quality and transmission efficiency, have attracted significant attention. To achieve better meshing performance, tooth surface modification technology is widely applied in gear design. Various studies have focused on the impact of different modification methods and amounts on gear transmission performance, tooth surface wear and system dynamic response, as well as optimization of tooth surface modification based on minimum wear. Furthermore, research has been conducted on optimizing砂轮profiles for topological modification of gears, solving methods for machine tool motion parameters in grinding topological modified face gears, and methods for calculating ease-off parameters of spiral bevel gears using contact point angle errors.
Combining gear topological modification design with tooth surface friction power loss analysis promotes low-power consumption design of tooth surfaces. Researchers have proposed multi-objective optimization models for hypoid gear transmission performance through the combination of LTCA and mixed elastohydrodynamic lubrication (mEHL) analysis. Studies have also investigated the impact of friction force on mesh stiffness when tooth surface roughness changes, provided regression formulas for mEHL friction coefficients, studied the meshing efficiency of hypoid gear pairs, analyzed the influence of wear on transmission efficiency and NVH dynamics by combining gear TCA models with multibody tribology models, and established mathematical models to predict oil film thickness and friction coefficients under EHL conditions for bevel gears.
However, the high coupling between tooth surface topology design and EHL model parameters, along with the complexity of tooth surface geometry and EHL parameter calculations, limits the development of tribology, especially for HRH gears with extremely complex spatial structures. Given this, this paper takes a pair of 3:60 HRH gears as an example, starting from geometric modeling of tooth surface topological modification and ease-off analysis, to obtain curvature parameters at contact points. Using the LTCA method, mechanical parameters of the tooth surface are obtained, solving the coupling issue between geometric and mechanical parameters. LTCA and mEHL differential strip calculation methods are proposed and validated through transmission efficiency tests.
2. Methodology
2.1 Conjugate Surface with Identical Tangent Planes
The meshing equation between the pinion and the generating gear is as follows:
The actual tooth surface equation of the pinion r1(u1, θ1) can be obtained. The relative modification amount between the pinion and gear is:
zd(u2, θ2) = (rc1 – r1) · nc1
By analyzing the ease-off surface, the tooth surface contact trace points and contact line gaps can be obtained. The transmission error (TE) of the tooth meshing is composed of the ease-off deviations of all trace points.
Table 1: Example of Geometric Parameter Calculations
Parameter | Description | Symbol |
---|---|---|
Rotation speed | Rotation speed of gear 1 (pinion) | ω1 |
Rotation speed | Rotation speed of gear 2 | ω2 |
Radius of curvature | Radius of curvature at contact point | R |
Entrainment velocity | Relative motion line speed | v(12) |
Sliding-to-rolling ratio | Ratio of sliding to rolling velocity | Sr |
3. LTCA for Contact Point Load Calculation
For any contact lin], in addition to the trace point, there are gaps zc at other positions on the contact line. Assuming a total deformation δi under load F, which is also the normal deformation of the trace point, the deformation of other elements on the same contact line is δi – zc.
4. EHL Friction Power Loss Calculation Analysis
4.1 Minimum Oil Film Thickness Calculation
While the line contact EHL model is easy to solve, the curvature, entrainment velocity, and load parameters at any position on the contact line vary, making direct application of the line contact EHL model impractical. Utilizing the contact stress calculation unit , the point contact problem is transformed into micro-unit line contact by subdividing the EHL interface. The classic Dowson and Hamrock formula is used to calculate the contact line.
Table 2: Example of EHL Parameter Calculations
Parameter | Description | Symbol |
---|---|---|
Oil film thickness | Minimum oil film thickness | hmin |
Friction coefficient | EHL friction coefficient | μ |
Contact stress | Contact stress at each micro-unit on the contact line | σc |
5. Experimental Validation
Transmission efficiency tests are conducted to validate the proposed LTCA, friction power loss analysis, and meshing efficiency calculation models. The test setup includes the HRH gear pair, driving and loaded systems, data acquisition and processing systems, etc.
6. Conclusion
This paper presents a comprehensive analysis of friction power loss and efficiency for high reduction hypoid gears. By utilizing the conjugate surface with identical tangent planes method, LTCA, and EHL theory, the distribution laws of oil film thickness, friction coefficient, and friction power loss on the tooth surface are obtained. The proposed models are validated through transmission efficiency tests, providing valuable insights for the design and optimization of hypoid gears.