The gear hobbing process is a fundamental method used in the manufacturing of gears, offering precise and efficient gear production. This article provides a comprehensive overview of the gear hobbing process, starting from the basics and progressing to advanced techniques, shedding light on its key elements and advancements.
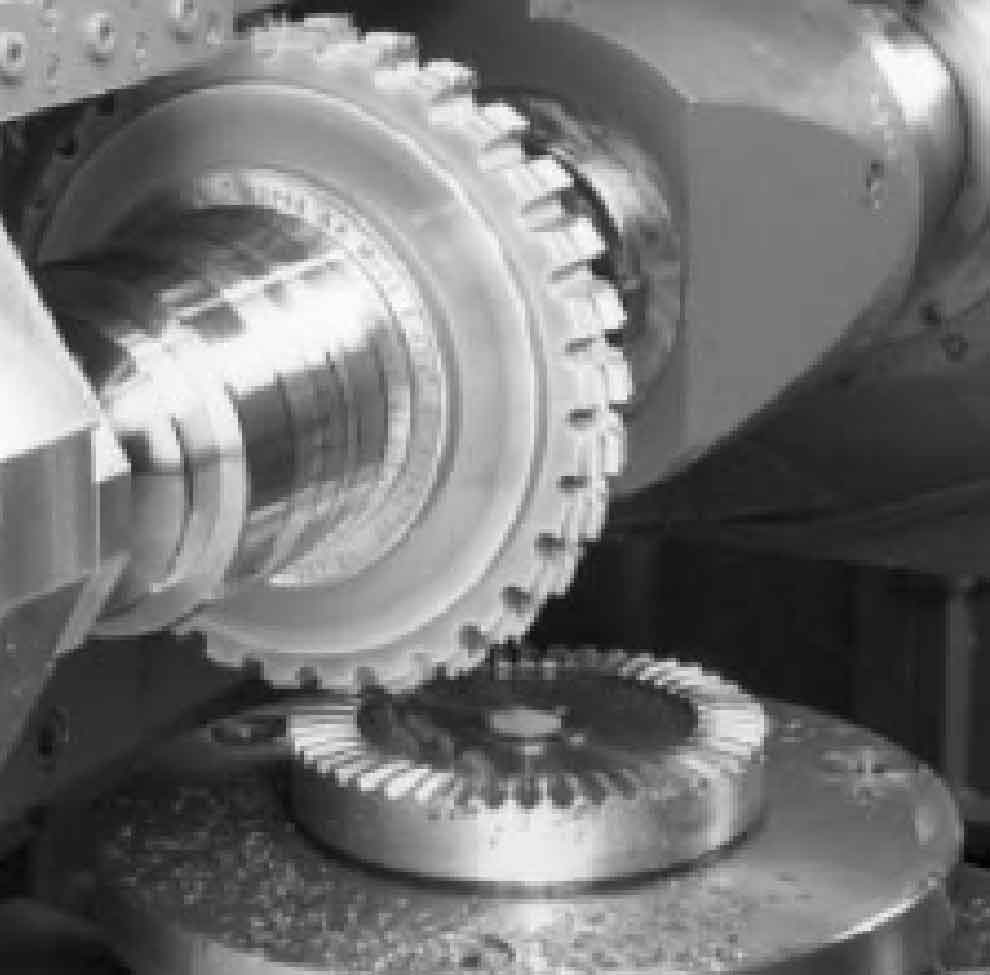
- Gear Hobbing Basics:
- Gear Hob: Exploring the characteristics of the gear hob, its design, and the various types available for different gear applications.
- Machine Setup: Understanding the setup of the gear hobbing machine, including workpiece mounting, hob positioning, and alignment considerations.
- Cutting Principles: Unraveling the fundamental principles of gear hobbing, including the relationship between the hob’s rotational speed, feed rate, and gear tooth profile generation.
- Gear Hobbing Process Steps:
- Preparatory Operations: Preparing the workpiece surface, selecting the appropriate cutting parameters, and ensuring proper lubrication for smooth operation.
- Hobbing Sequence: Detailing the sequence of movements involved in gear hobbing, such as hob rotation, axial feed, and indexing, and their role in creating the gear tooth profile.
- Finishing Operations: Examining the post-hobbing processes, including deburring, inspection, and heat treatment, to enhance the gear’s surface finish, durability, and overall quality.
- Advanced Gear Hobbing Techniques:
- High-Speed Gear Hobbing: Exploring the advancements in gear hobbing machines and techniques that allow for higher cutting speeds, improving productivity without sacrificing accuracy.
- Multi-Axis Gear Hobbing: Investigating the utilization of multi-axis machines to produce complex gear geometries, such as helical gears and non-circular gears.
- Dry Hobbing: Discussing the emerging trend of dry hobbing, which eliminates the need for coolant and provides environmental benefits while maintaining precision.
- Gear Hobbing Simulation and Optimization: Highlighting the use of computer-aided design (CAD) and computer-aided manufacturing (CAM) software for virtual gear hobbing simulations and optimization, reducing development time and ensuring optimal gear performance.
The gear hobbing process is a fundamental technique in gear manufacturing, allowing for precise and efficient production of various gear types. By understanding the basics of gear hobbing and exploring advanced techniques, manufacturers can optimize the process for enhanced productivity, improved gear quality, and increased versatility. With continuous advancements in gear hobbing technology and simulation tools, gear manufacturers can push the boundaries of gear design and achieve even greater precision and efficiency in their production processes.