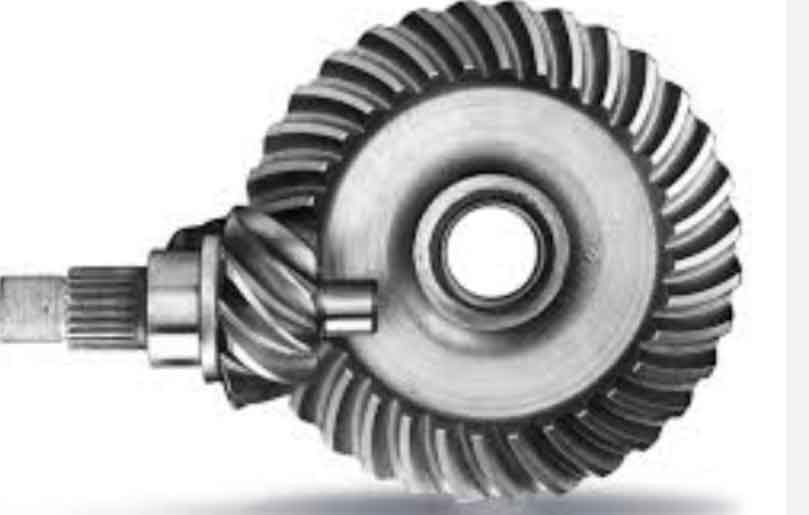
Hypoid gears are a type of spiral bevel gears that are widely used in mechanical systems due to their unique advantages over other gear types. They are known for their ability to transmit power between non-parallel shafts while offering higher torque capacity, smoother operation, and improved efficiency compared to traditional straight bevel gears. Implementing hypoid gears in mechanical systems involves several steps, from design considerations to manufacturing and maintenance. Below is an overview of the process:
- Design and Analysis:
- Define the application requirements, such as torque, speed, operating conditions, and space constraints.
- Choose the appropriate hypoid gear ratio to achieve the desired torque transmission between non-parallel shafts.
- Conduct detailed stress analysis and simulations to ensure the gears can handle the expected loads and minimize noise and vibration issues.
- Gear Geometry and Calculations:
- Determine the gear parameters, including pitch diameter, pressure angle, helix angle, and backlash.
- Calculate the gear tooth profiles using specialized software or formulas based on the chosen hypoid gear type (e.g., Gleason or Klingelnberg).
- Gear Material Selection:
- Select suitable materials with high strength, wear resistance, and durability to withstand the operating conditions and loads.
- Consider factors like heat treatment and surface coatings to enhance gear performance and prolong service life.
- Manufacturing Process:
- Use advanced CNC machines for precise gear cutting to ensure accurate tooth profiles and proper meshing between gears.
- Depending on the complexity and quantity of gears required, consider traditional methods like gear hobbing or modern techniques like 5-axis machining.
- Assembly and Testing:
- Assemble the hypoid gears into the mechanical system with precision to ensure proper alignment and meshing.
- Conduct thorough testing to validate the gear performance under the expected operating conditions.
- Address any issues identified during testing and make necessary adjustments.
- Lubrication and Maintenance:
- Implement an appropriate lubrication strategy to reduce friction, wear, and noise during gear operation.
- Develop a maintenance plan, including regular inspections, lubricant replacement, and gear reconditioning when necessary.
- Efficiency and Noise Considerations:
- Optimize the gear design and manufacturing process to improve gear efficiency and reduce noise levels.
- Use specialized software tools and Finite Element Analysis (FEA) to evaluate the gear’s performance and predict noise behavior.
- Application-specific Considerations:
- Depending on the specific application, consider additional factors such as environmental conditions, safety standards, and regulatory requirements.
Implementing hypoid gears in mechanical systems requires careful design, precision manufacturing, and rigorous testing to ensure optimal performance, reliability, and longevity of the gear system. Collaboration between mechanical engineers, gear designers, and manufacturing experts is essential to successfully incorporate hypoid gears into various applications ranging from automotive differentials to industrial machinery and beyond.