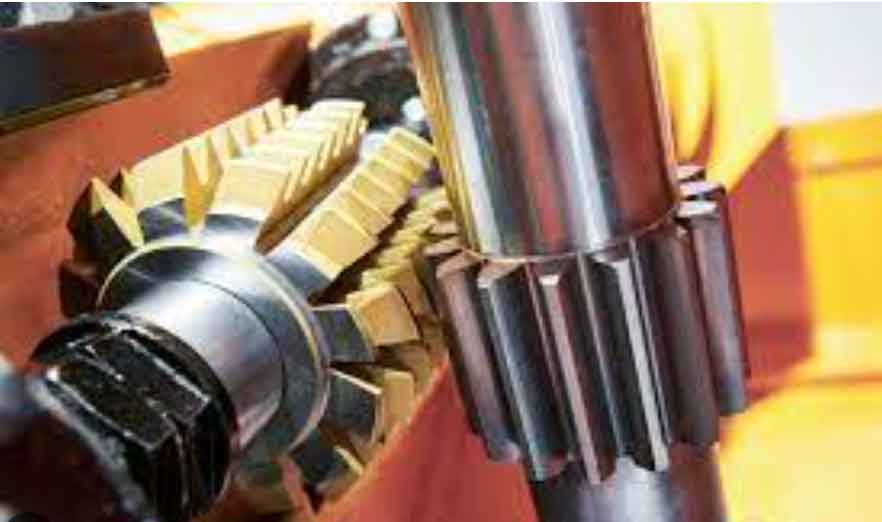
As technology continues to advance, gear hobbing is expected to undergo several innovations and trends to meet the evolving needs of various industries. Some future trends in gear hobbing technology include:
- High-Speed Gear Hobbing: Advancements in cutting tool materials, machine rigidity, and cutting strategies will enable even higher cutting speeds during gear hobbing. High-speed gear hobbing will reduce cycle times and increase productivity without compromising gear quality.
- Automation and Industry 4.0 Integration: Gear hobbing machines will become more interconnected with other manufacturing processes, enabling seamless automation and integration into Industry 4.0 systems. This integration will allow real-time data monitoring, predictive maintenance, and adaptive control to optimize the entire production process.
- Smart Tooling and Sensors: Gear hobbing tools will incorporate smart sensors to monitor cutting conditions, tool wear, and other crucial parameters. Real-time feedback from these sensors will enable adaptive control and ensure consistent gear quality throughout the production process.
- Simulation and Virtual Machining: Advanced simulation software will allow manufacturers to simulate the gear hobbing process virtually before actual production. This will help optimize cutting parameters, reduce setup times, and minimize the risk of errors.
- Additive Manufacturing and Hybrid Processes: Additive manufacturing techniques will be combined with traditional gear hobbing processes to produce complex gear geometries and optimize gear performance for specific applications.
- Environmentally Friendly Lubrication: Gear hobbing will transition towards more eco-friendly lubrication techniques, reducing the environmental impact of machining processes while maintaining high performance.
- Digital Twin Technology: The use of digital twin technology will enable virtual replicas of gear hobbing machines, allowing for predictive maintenance, optimization, and performance analysis.
- Optimization Algorithms: AI-driven optimization algorithms will be employed to find the best cutting parameters and hob cutter designs for specific gear types and materials, enhancing efficiency and gear quality.
- Continuous Hobbing: Continuous hobbing methods will gain popularity, eliminating idle times between workpieces and enhancing production throughput.
- Green Gear Hobbing: Manufacturers will focus on sustainability, energy efficiency, and waste reduction during gear hobbing processes to reduce the overall environmental footprint.
- Hybrid Gear Manufacturing: Hybrid gear manufacturing processes, combining gear hobbing with other techniques like gear shaping or gear grinding, will offer increased flexibility and cost-effectiveness for gear production.
- Miniaturization: Gear hobbing machines for micro-gears will be developed to meet the growing demand for precision miniature gears used in various industries, including medical devices and electronics.
These trends will drive the future of gear hobbing technology, making gear production more efficient, accurate, and adaptable to diverse applications. Gear hobbing will continue to be a critical process in gear manufacturing, supporting industries ranging from automotive and aerospace to robotics and medical devices.