The future of spur gear technology is shaped by advancements in materials science, manufacturing techniques, and the increasing demands of various industries for more efficient, durable, and compact gear systems. Here’s a look at some of the emerging trends that are likely to define the next generation of spur gear technology:
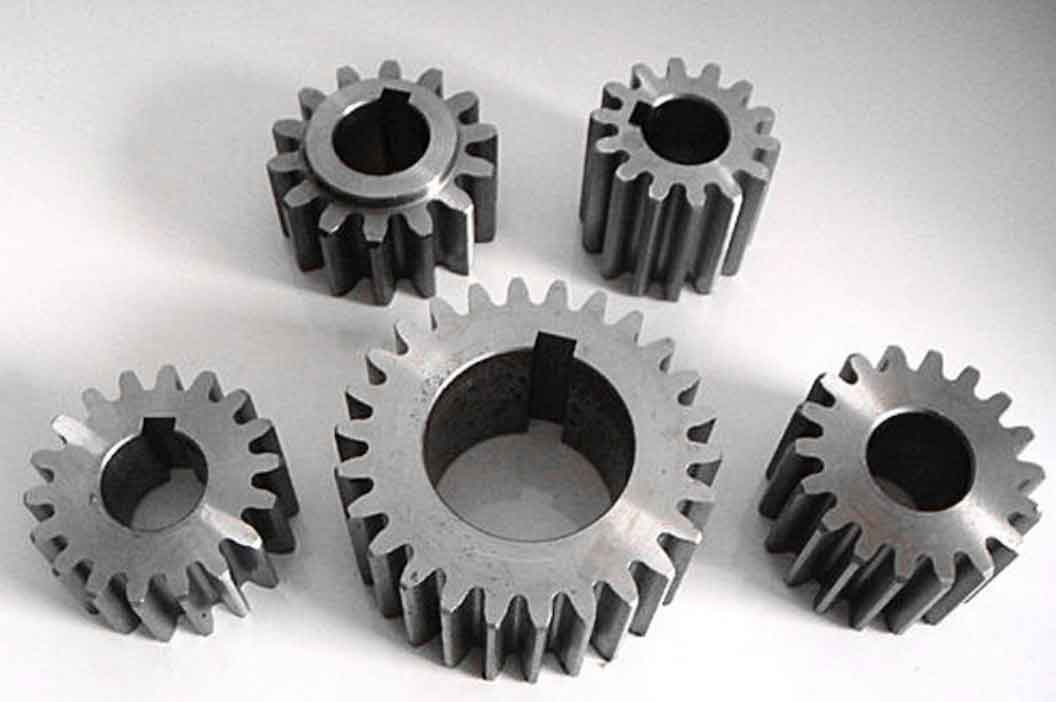
1. Advanced Materials
- Composite Materials: The use of lightweight composite materials is expected to increase, particularly in aerospace and automotive industries, where reducing weight is crucial for efficiency and performance. Composite spur gear offer significant weight savings along with adequate strength and noise reduction capabilities.
- Smart Materials: Developments in smart materials that can adapt their properties based on environmental conditions or load requirements might revolutionize spur gear designs, offering dynamic performance adjustments.
- High-Performance Alloys: Continuing innovations in metallurgy will likely produce new alloys that are stronger, more wear-resistant, and capable of operating under higher stresses and temperatures.
2. Additive Manufacturing
- 3D Printing of Gears: Additive manufacturing allows for the creation of complex geometries that are difficult or impossible to achieve with traditional methods. For spur gears, this could mean integrated designs with variable tooth profiles or built-in cooling channels.
- Rapid Prototyping: The ability to quickly produce prototypes will speed up the development cycles of new spur gear systems, allowing for more iterative testing and optimization.
3. Surface Engineering
- Advanced Coatings: New coatings will enhance the surface hardness, wear resistance, and corrosion resistance of spur gears. Techniques like diamond-like carbon (DLC) coatings and other nanocomposite coatings are already showing promise in extending gear life and performance.
- Laser Peening: This process induces residual compressive stress on spur gear surface to improve fatigue strength. As this gear technology becomes more accessible, it could become a standard treatment for high-performance gears.
4. Microgeometry and Topology Optimization
- Tooth Flank Modifications: The refinement of tooth flank modifications will continue to evolve to further reduce stress concentrations and improve load distribution across spur gear teeth, enhancing the overall lifespan and noise characteristics.
- Topology Optimization: Utilizing advanced computational methods to optimize the material layout within spur gear for the best mechanical performance while minimizing weight.
5. Noise Reduction Technologies
- Noise Optimization: As the demand for quieter machinery increases, particularly in consumer-facing industries, the development of spur gears with optimized noise characteristics will become more prevalent. This will involve both design improvements and material choices that naturally dampen vibration and noise.
6. Integration with IoT and Smart Systems
- Condition Monitoring: Future spur gear is likely to be integrated with sensors that monitor their condition in real time, providing data on wear, temperature, and lubrication status. This IoT integration will facilitate predictive maintenance and system optimizations based on actual usage data.
- Smart Lubrication Systems: Automated lubrication systems that adjust the flow and type of lubricant based on real-time operating conditions could significantly extend the life of spur gear while maintaining optimal efficiency.
7. Sustainability and Recycling
- Greener Production: As environmental regulations tighten, there will be a push towards more sustainable manufacturing processes. This includes the use of recyclable materials and energy-efficient production techniques.
- Lifecycle Management: The entire lifecycle of spur gear—from production and operation to disposal—will increasingly be optimized for minimal environmental impact.
Conclusion
The future of spur gear technology is poised for exciting developments driven by innovations across several domains. These advancements will not only enhance the performance and efficiency of spur gear but also open up new applications and capabilities in diverse sectors, reinforcing the relevance of this fundamental mechanical component.