The gear calculator plays a crucial role in the gear engineering process, facilitating the journey from concept to the creation of gears. It assists engineers in various stages of gear engineering, ensuring accurate calculations and informed decisions. Here’s how a gear calculator helps in each step of the gear engineering process:
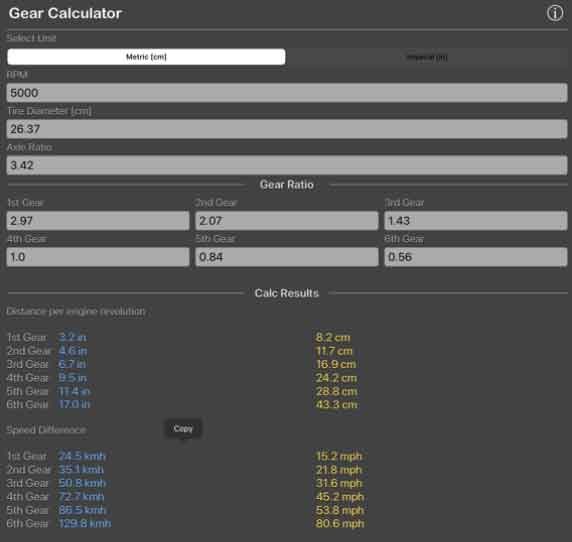
- Conceptual Design: In the initial stage of gear engineering, a gear calculator helps engineers explore different design concepts. By inputting basic parameters such as gear module, pressure angle, and number of teeth, the calculator generates preliminary calculations and provides an overview of the gear system’s characteristics. This aids engineers in assessing the feasibility of different gear designs and selecting suitable options for further analysis.
- Detailed Design: Once a design concept is chosen, a gear calculator assists in the detailed design phase. Engineers input specific parameters such as gear dimensions, tooth profiles, and material properties into the calculator. It accurately calculates critical dimensions, such as pitch diameter, tooth thickness, and center distance. The calculator ensures that the gear design meets the desired specifications and standards, providing essential information for the manufacturing process.
- Load Analysis: A gear calculator enables engineers to analyze the loads and operating conditions to which the gears will be subjected. By inputting parameters such as torque, speed, and gear ratios, the calculator calculates the load distribution across the gear teeth, contact stresses, and bending stresses. This analysis ensures that the gears are designed to handle the expected loads and operate within safe limits, promoting reliability and longevity.
- Efficiency Optimization: Gear calculators assist in optimizing gear efficiency. By considering parameters such as tooth profiles, lubrication conditions, and gear ratios, the calculator estimates the efficiency and power losses within the gear system. Engineers can analyze different design options and make informed decisions to maximize efficiency and minimize energy losses, resulting in improved overall gear system performance.
- Contact Analysis: Gear calculators perform contact analysis to evaluate the contact patterns between gear teeth. This analysis ensures proper tooth engagement, identifies potential issues like interference or edge contact, and guides engineers in making necessary modifications to achieve optimal gear meshing and reduce frictional losses.
- Simulation and Visualization: Advanced gear calculators provide simulation and visualization capabilities. Engineers can input the gear design parameters and simulate the behavior of the gear system, including tooth contact patterns, load distribution, and efficiency. This allows engineers to visualize and analyze the performance of different design configurations, identify potential issues, and optimize the gear system before manufacturing.
- Verification and Validation: Gear calculators serve as a tool for verification and validation of the gear design. Engineers can compare the calculated results with industry standards, design guidelines, and theoretical models to ensure accuracy and compliance. This step is critical to guarantee the gear design’s reliability, functionality, and adherence to required specifications.
By utilizing a gear calculator throughout the gear engineering process, engineers can effectively move from the conceptual design to the creation of gears. The calculator provides accurate calculations, enables load analysis, optimizes efficiency, performs contact analysis, facilitates simulation, and assists in verification and validation. This comprehensive tool empowers engineers to make informed decisions and achieve the desired gear engineering outcomes.