Here are a few case studies that highlight the successful application of gear calculators in real-world gear design projects:
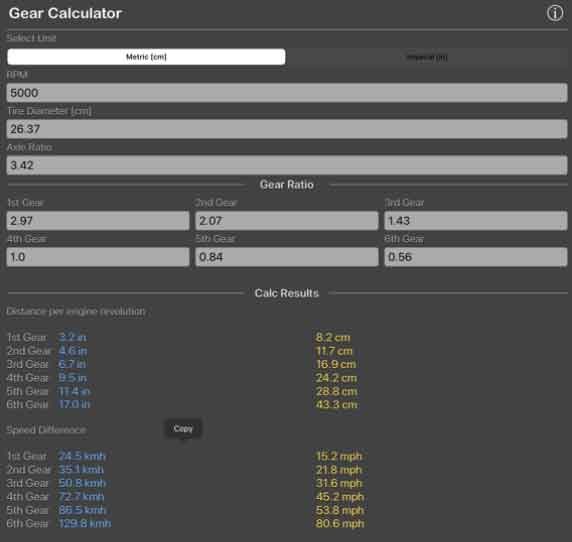
Case Study 1: Industrial Gearbox Design A manufacturer needed to design a gearbox for an industrial application that required specific speed reduction and torque requirements. By using a gear calculator, they input the desired input and output speeds, torque values, and other relevant parameters. The gear calculator helped them determine the optimal gear ratio and select suitable gear types and configurations. The calculator provided accurate calculations for gear dimensions, tooth profiles, load distribution, and estimated efficiency. The gearbox design was successfully optimized using the gear calculator, resulting in a reliable and efficient gear system.
Case Study 2: Automotive Transmission Design An automotive company aimed to develop a new transmission system for their vehicles. They used a gear calculator to evaluate different gear configurations, such as helical gears and bevel gears, and determine the appropriate gear ratios. The gear calculator helped them analyze load distribution, calculate tooth contact patterns, estimate power losses, and optimize gear dimensions. By iteratively using the gear calculator, they refined the design, achieved the desired gear ratios, minimized noise and vibration, and improved overall transmission efficiency.
Case Study 3: Robotics Gear System Design A robotics company needed to design a compact and high-performance gear system for their robotic arm. They used a gear calculator to evaluate various gear types, such as planetary gears and worm gears, and determine the best configuration for their specific requirements. The gear calculator assisted in calculating gear ratios, analyzing load distribution, estimating power losses, and optimizing gear sizes. By using the gear calculator, they achieved a compact and efficient gear system that met their torque and speed requirements while ensuring smooth and precise motion control.
Case Study 4: Wind Turbine Gearbox Design A wind turbine manufacturer aimed to design a gearbox for a wind turbine system. They utilized a gear calculator to analyze different gear configurations, such as parallel shaft gears and helical gears, and determine the optimal gear ratios for power generation. The gear calculator helped them assess load distribution, estimate power losses, calculate gear sizes, and optimize the gear system for high efficiency and durability. By leveraging the capabilities of the gear calculator, they successfully designed a gearbox that met the demanding requirements of wind turbine applications.
These case studies demonstrate how gear calculators have been instrumental in achieving successful gear designs across various industries. By utilizing the advanced calculations, simulations, and optimization features provided by gear calculators, engineers can effectively design gear systems that meet specific performance requirements, improve efficiency, reduce noise and vibration, and enhance overall reliability.