Gear forging is a manufacturing process that enhances the performance and reliability of gears in various applications. Here are some ways in which gear forging contributes to the improvement of gear performance and reliability:
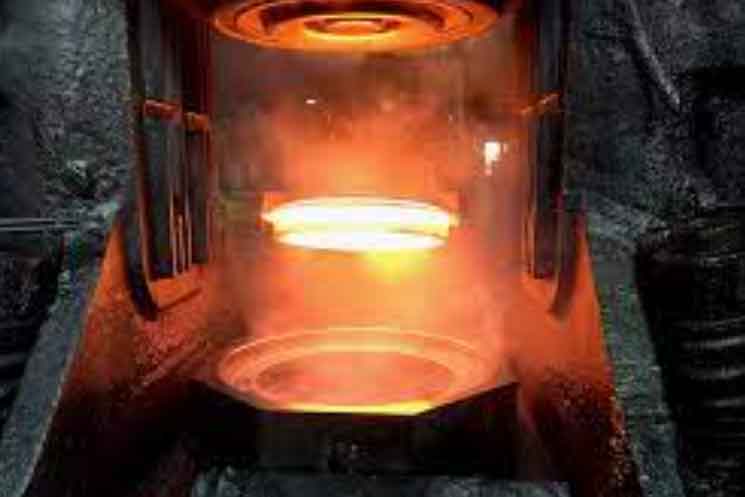
- Improved Material Strength: Forged gears exhibit superior material strength compared to gears produced by other methods. The forging process aligns the grain structure of the material, resulting in enhanced mechanical properties such as higher tensile strength, fatigue resistance, and impact toughness. This increased material strength allows forged gears to withstand heavy loads, high speeds, and demanding operating conditions without deformation or failure.
- Enhanced Wear Resistance: Gear forging ensures a more uniform and refined microstructure, which improves wear resistance. The forged gears have a dense and homogeneous structure with fewer defects or voids, reducing the potential for surface damage and wear. This results in extended gear life and reduced maintenance requirements in applications with high wear rates or abrasive environments.
- Optimized Tooth Geometry: The forging process allows for precise control over the tooth geometry of the gears. The use of precision dies and careful forging techniques ensures accurate tooth profiles, tooth spacing, and gear dimensions. This optimized tooth geometry enables proper gear meshing, reduces noise and vibration, and enhances the overall efficiency of gear transmission.
- Uniform Grain Flow: During gear forging, the material experiences controlled plastic deformation, leading to a uniform grain flow pattern. This uniform grain flow enhances the mechanical properties and structural integrity of the gears. The aligned grain structure provides improved strength and fatigue resistance, minimizing the risk of premature gear failure.
- Reduction of Internal Defects: The forging process eliminates internal defects commonly found in other manufacturing methods, such as voids, porosity, and inclusions. By subjecting the material to high pressure and compressive forces, any internal defects are closed or eliminated, resulting in a sound and defect-free gear structure. This significantly improves the reliability and fatigue life of the gears.
- Consistent Material Properties: Gear forging ensures consistency in material properties throughout the gear. The controlled and uniform deformation of the material during forging leads to consistent mechanical properties across the entire gear profile. This consistency allows for predictable gear behavior, better load distribution, and improved overall performance in gear systems.
- Higher Fatigue Resistance: Forged gears have excellent fatigue resistance due to their refined microstructure and improved material properties. The aligned grain structure reduces stress concentrations and enhances the gear’s ability to withstand cyclic loading without developing cracks or failures. This makes forged gears highly reliable and durable, even under repetitive or fluctuating loads.
- Improved Dimensional Accuracy: Gear forging offers excellent dimensional accuracy, ensuring precise gear dimensions and tooth profiles. The use of precision dies and the controlled forging process results in tight tolerances and consistent gear geometry. This accuracy enables proper gear meshing, minimizes backlash, and contributes to smoother and more efficient power transmission.
Gear forging plays a vital role in enhancing the performance and reliability of gears in various industries, including automotive, aerospace, power generation, and heavy machinery. By leveraging the advantages of gear forging, manufacturers can produce high-quality gears that deliver superior performance, extended service life, and increased reliability in demanding applications.