Gear forging plays a vital role in the aerospace industry, where stringent quality and performance standards are essential for ensuring the safety, reliability, and efficiency of aircraft. Let’s explore how gear forging meets these standards and contributes to the aerospace industry:
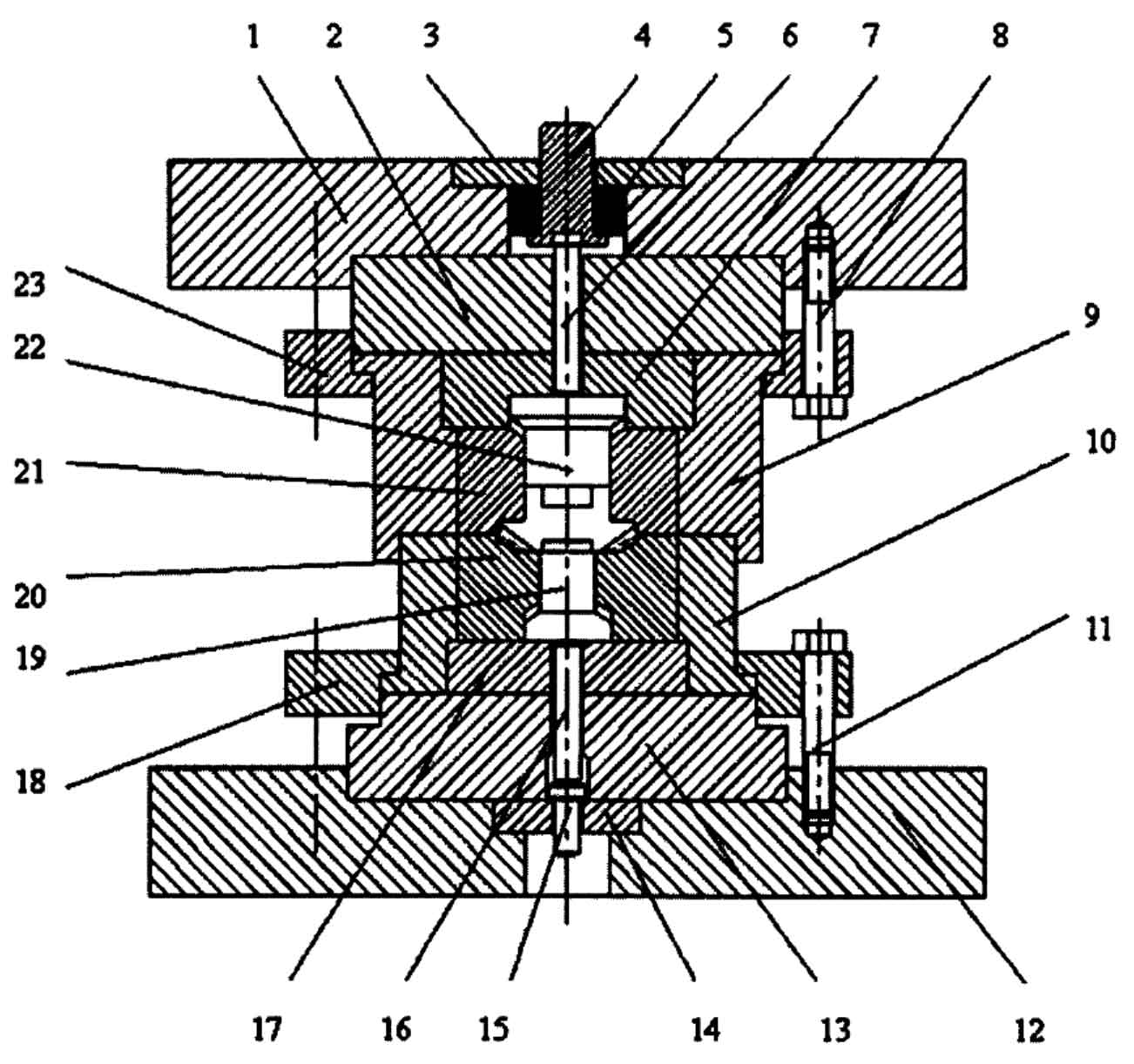
- Material Strength and Performance: Aerospace gears operate in demanding conditions, experiencing high loads, extreme temperatures, and rapid changes in torque and speed. Gear forging produces gears with superior strength and performance characteristics. The forging process aligns the grain structure of the material, resulting in improved mechanical properties such as high tensile and fatigue strength, toughness, and resistance to wear and corrosion. Forged gears are capable of withstanding the challenging operating conditions encountered in aerospace applications, providing reliable and efficient power transmission.
- Weight Optimization: Weight reduction is a critical factor in aerospace design to enhance fuel efficiency and maximize payload capacity. Gear forging offers the advantage of producing lightweight gears with high strength-to-weight ratios. By optimizing the material distribution and removing excess material through the forging process, forged gears achieve weight savings without compromising strength and performance. This contributes to overall weight reduction in aircraft systems.
- Dimensional Accuracy and Tolerances: Gear precision is of utmost importance in aerospace applications. Forging processes, such as closed-die forging, enable high dimensional accuracy and tight tolerances. The use of specialized dies and advanced forging techniques ensures consistent gear profiles and precise tooth geometry. This accuracy enhances gear meshing, minimizes noise and vibration, and ensures reliable and smooth operation of the aerospace systems.
- Fatigue and Life-Cycle Performance: Aerospace gears are subjected to cyclic loading and high-stress environments, making fatigue resistance a critical requirement. Gear forging enhances fatigue performance by optimizing the grain structure, eliminating material defects, and improving the surface finish. The resulting forged gears exhibit excellent fatigue strength and durability, providing a long operational life and reducing the risk of premature failures in aerospace applications.
- Quality Assurance and Traceability: The aerospace industry has stringent quality control requirements. Gear forging processes incorporate comprehensive quality assurance measures to ensure adherence to these standards. This includes stringent material testing, non-destructive inspection techniques, dimensional verification, and adherence to industry-specific certifications such as AS9100. Additionally, the traceability of materials and manufacturing processes is crucial in aerospace applications, and gear forging enables clear documentation and traceability throughout the production process.
- Reliability and Safety: The aerospace industry places a paramount emphasis on reliability and safety. Forged gears offer a high level of reliability due to their enhanced strength, durability, and performance capabilities. The precise manufacturing and quality control processes involved in gear forging ensure consistent and reliable gear performance. This reliability is critical for the safe operation of aerospace systems, including engines, landing gear systems, and rotorcraft transmissions.
- Customization for Aerospace Applications: Gear forging allows for customization to meet the unique requirements of aerospace applications. Aerospace gears often have specific design considerations, such as reduced noise, vibration, and space constraints. Forging processes enable the production of gears with optimized tooth profiles, geometries, and surface finishes to address these specific requirements and ensure optimal performance in aerospace systems.
Gear forging in the aerospace industry meets the stringent quality and performance standards necessary for safe and reliable operation. It offers exceptional material strength, dimensional precision, fatigue resistance, and weight optimization, contributing to the overall efficiency and performance of aircraft systems. The rigorous quality control measures and traceability ensure adherence to industry standards and regulations, ensuring the highest level of safety and reliability in aerospace applications.