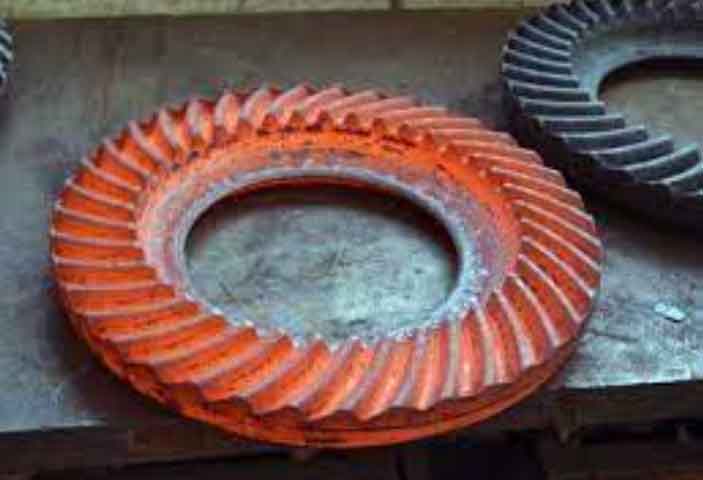
Gear forging is a manufacturing process that involves shaping metal into gears through the application of compressive forces. Forged gears offer exceptional strength, reliability, and other advantages, making them highly desirable in various industries. Here are the key benefits of forged gears:
Superior Strength:
Forged gears have higher strength and toughness compared to gears produced through other methods like casting or machining. The forging process aligns the grain structure of the metal, resulting in increased mechanical properties and resistance to wear and fatigue.
Enhanced Reliability:
Due to their superior strength, forged gears can handle heavy loads, high speeds, and harsh operating conditions with minimal risk of failure. They are known for their long-lasting performance and reduced maintenance needs.
Consistent Quality:
The forging process ensures uniform and consistent material properties across the entire gear, leading to higher quality and reliability. Forged gears exhibit excellent dimensional accuracy and tight tolerances.
Reduced Material Waste:
Forging generates minimal material waste compared to other manufacturing processes like machining. This makes the forging process more sustainable and cost-effective in the long run.
Customizable Design:
Forging allows for the production of gears with intricate shapes, profiles, and custom specifications to meet specific application requirements. The flexibility in design ensures that forged gears can be tailored for various gear systems.
Impact and Shock Resistance:
Forged gears exhibit excellent resistance to impact and shock loads, making them suitable for heavy-duty applications in industries such as mining, construction, and agriculture.
Cost-Effectiveness:
While the initial tooling and setup costs for gear forging can be higher, the long-term benefits of improved gear performance, extended service life, and reduced maintenance costs outweigh the initial investment.
Shorter Lead Times:
Forging can provide quicker production times compared to other methods like gear cutting. This advantage is particularly beneficial when a rapid gear supply is required.
Wide Range of Materials:
Forging can be applied to various materials, including carbon steels, alloy steels, stainless steels, and non-ferrous metals, allowing for versatility in gear material selection.
Safety and Reliability:
The enhanced material properties of forged gears contribute to safer operations, as they are less prone to sudden failures that could lead to accidents.
Due to these numerous advantages, forged gears are widely used in critical applications, such as automotive transmissions, industrial machinery, heavy equipment, marine propulsion systems, and more. The combination of strength, reliability, and customized design options makes gear forging a preferred choice for high-performance gear applications.