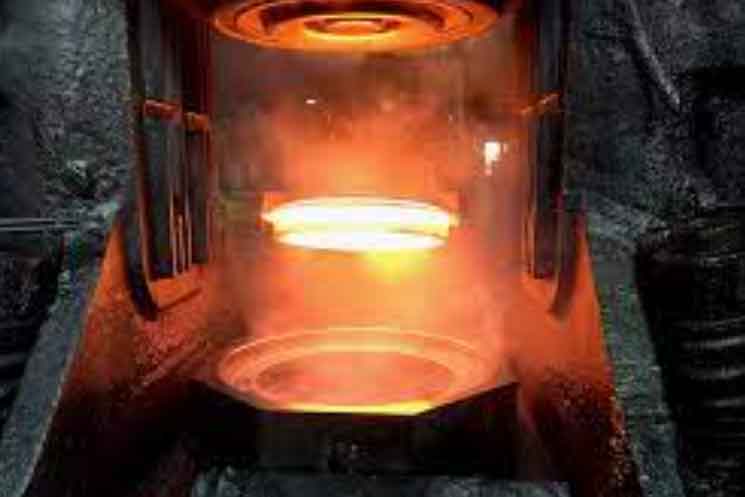
When it comes to gear manufacturing, choosing the right method between gear forging and gear machining depends on various factors such as the application requirements, production volume, cost considerations, and desired gear characteristics. Here’s a comparison between gear forging and gear machining to help you make an informed decision:
Gear Forging:
- Strength and Durability: Forged gears offer excellent strength, durability, and resistance to fatigue due to the grain flow alignment and refined microstructure achieved through the forging process. They are suitable for applications with high loads and demanding operating conditions.
- Customization: Gear forging allows for customization in terms of material selection, gear design, and heat treatment. It enables the production of gears with specific properties and geometries tailored to the application requirements.
- Cost-Effectiveness: Forging can be cost-effective for high-volume production due to its efficient material utilization and the ability to produce multiple identical gears using dedicated dies. It can also result in lower maintenance costs due to the gears’ superior strength and reliability.
- Production Lead Time: Gear forging generally requires longer lead times compared to gear machining, as it involves die preparation and setup. However, once the dies are ready, the production process can be relatively fast and efficient.
Gear Machining:
- Accuracy and Precision: Gear machining, such as gear hobbing or gear shaping, offers high accuracy and precision in creating gears with tight tolerances. It allows for the production of gears with complex geometries and specific tooth profiles.
- Flexibility: Machining provides flexibility in terms of producing gears in different sizes, tooth profiles, and materials. It can handle both small and large production runs and offers versatility for prototyping and low-volume production.
- Surface Finish: Machining processes can achieve excellent surface finishes on gear teeth, resulting in reduced friction, noise, and wear. It is advantageous for applications requiring smooth and precise gear operation.
- Cost-Effectiveness: Gear machining is generally more cost-effective for small to medium production volumes or complex gear designs. It does not require dedicated dies or tooling, making it suitable for producing gears in smaller quantities or when design changes are frequent.
- Lead Time: Machining processes typically have shorter lead times compared to forging, as they do not involve die preparation. Gears can be machined relatively quickly once the setup is complete, making it suitable for time-sensitive projects.
In summary, gear forging is preferable when superior strength, durability, and customization are required for high-volume production. On the other hand, gear machining offers accuracy, flexibility, and shorter lead times, making it suitable for small to medium production volumes, complex gear geometries, and prototyping. Ultimately, the choice between gear forging and gear machining depends on the specific requirements of the application, production volume, cost considerations, and desired gear characteristics.