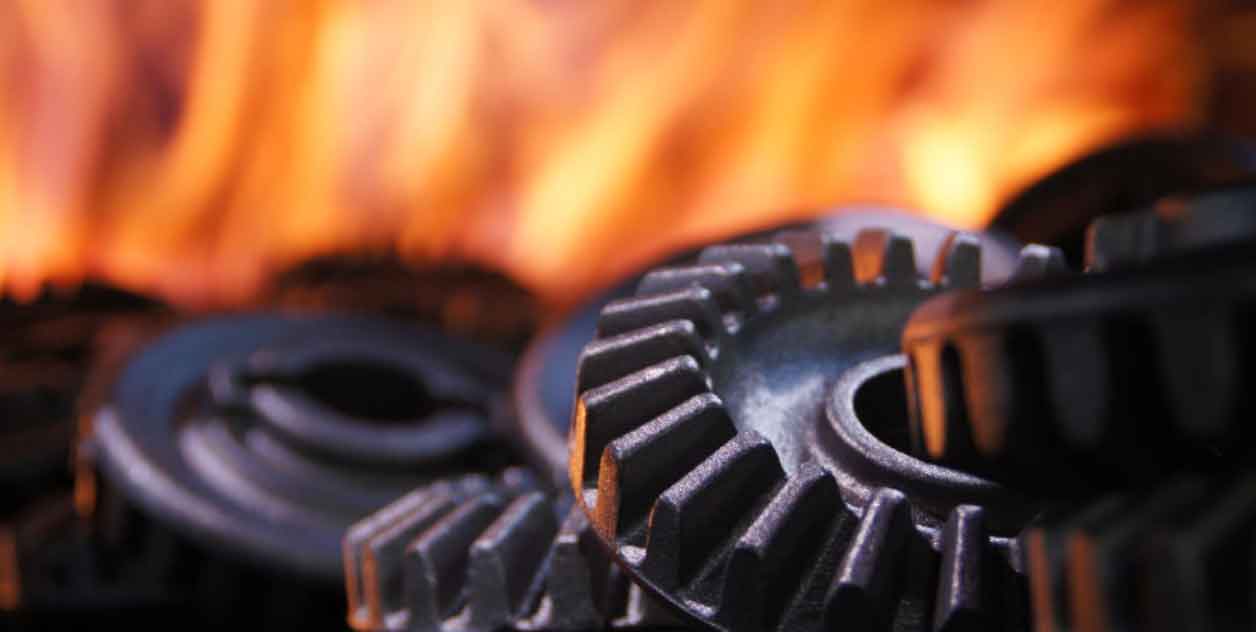
Gear forgings are indeed a robust solution for achieving reliable gear performance in various mechanical applications. Forgings, in general, are produced by applying compressive forces to a metal billet or ingot, thereby shaping it into the desired form. When it comes to gear production, utilizing forging processes offers several advantages over other manufacturing methods such as casting or machining. Let’s explore some of the reasons why gear forgings are preferred for reliable gear performance:
1.Strength and Durability:
Forgings exhibit exceptional strength due to the inherent grain structure refinement that occurs during the forging process. The controlled deformation and recrystallization of the metal grains result in increased strength and improved mechanical properties of the gear. As a result, forged gears can withstand heavy loads, shock loads, and cyclic stresses without premature failure, ensuring reliable performance.
2.Enhanced Fatigue Resistance:
Gears often experience cyclic loading, which can lead to fatigue failure if the material is not capable of withstanding repeated stress. Forged gears have superior fatigue resistance due to their refined grain structure and absence of internal defects, such as voids or gas pockets. This enhanced fatigue resistance contributes to the long-term reliability of the gear, minimizing the risk of unexpected failures.
3.Consistency and Uniformity:
Forging processes allow for precise control over the shaping of the gear, resulting in excellent dimensional accuracy and uniformity. The grain flow and mechanical properties can be optimized throughout the gear’s geometry, ensuring consistent performance across all sections of the gear tooth. This uniformity eliminates potential stress concentration points, further enhancing reliability.
4.Material Selection:
Forgings can be produced from a wide range of metals and alloys, depending on the specific application requirements. Common materials used for gear forgings include carbon steels, alloy steels, and stainless steels. The ability to select a material with suitable properties, such as high strength, toughness, and wear resistance, allows for tailored gear solutions that are optimized for the intended application.
Cost Efficiency: While the initial tooling and setup costs for gear forgings may be higher compared to other manufacturing methods, the long-term cost benefits are significant. The superior strength, durability, and fatigue resistance of forged gears result in extended service life, reduced maintenance, and lower replacement costs. The overall cost per unit of reliable gear performance is often more favorable when using gear forgings.
In summary, gear forgings provide a robust and reliable solution for gear performance in various applications. The combination of strength, enhanced fatigue resistance, dimensional accuracy, and material selection flexibility ensures that forged gears can handle demanding operating conditions with minimal risk of failure. Additionally, the long-term cost efficiency of gear forgings makes them a preferred choice for industries where reliability and performance are critical.