Gear forgings indeed play a crucial role in heavy-duty machinery, serving as the cornerstone for reliable and efficient mechanical power transmission systems. Let’s delve into the significance of gear forgings and their role in heavy-duty applications.
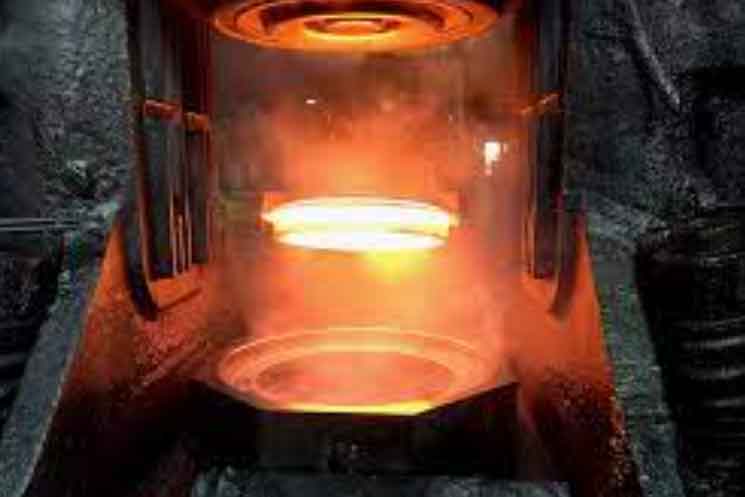
Gear forgings refer to the process of shaping and forming metallic gears through the application of heat and pressure. This forging method involves deforming a heated metal billet or ingot using specialized machinery and dies, resulting in the desired gear shape. The process enhances the mechanical properties of the metal, making it highly durable and capable of withstanding heavy loads, high speeds, and harsh operating conditions.
Here are some reasons why gear forgings are widely preferred in heavy-duty machinery:
- Strength and Durability: Gear forgings are renowned for their exceptional strength and durability. The forging process aligns the grain structure of the metal, making it more resistant to fatigue, impact, and wear. This ensures a longer service life and minimizes the risk of premature gear failure.
- Load Carrying Capacity: Heavy-duty machinery often operates under substantial loads and torque. Gear forgings can handle these demanding conditions due to their superior metallurgical properties. They offer high load-carrying capacities, enabling efficient power transmission without sacrificing performance.
- Precision and Accuracy: Gear forgings allow for precise dimensional control, ensuring accurate gear teeth profiles and clearances. This precision is vital for maintaining proper gear meshing, minimizing noise, vibrations, and the risk of damage caused by misalignment.
- Customization: Gear forgings can be tailored to meet specific application requirements. Manufacturers can produce gears with a wide range of sizes, tooth profiles, and gear ratios, ensuring compatibility and optimal performance in various heavy-duty machinery setups.
- Resistance to Wear and Fatigue: Heavy-duty machinery often operates in demanding environments with high temperatures, corrosive substances, or abrasive particles. Gear forgings are designed to withstand such conditions and exhibit excellent resistance to wear, corrosion, and fatigue, contributing to their long-term reliability.
- Cost-Effectiveness: While gear forgings may involve higher initial production costs compared to alternative methods, their long-term cost-effectiveness shines through. The durability and extended lifespan of gear forgings reduce maintenance and replacement expenses, leading to overall cost savings in heavy-duty machinery operations.
Commonly forged gears include spur gears, helical gears, bevel gears, and worm gears. These gear types find applications in a wide range of industries such as mining, construction, oil and gas, power generation, marine, and heavy transportation.
In summary, gear forgings are integral to heavy-duty machinery due to their exceptional strength, durability, load-carrying capacity, precision, customization options, resistance to wear and fatigue, and overall cost-effectiveness. They provide the reliable power transmission necessary to withstand demanding operating conditions and ensure the optimal performance of heavy-duty equipment.