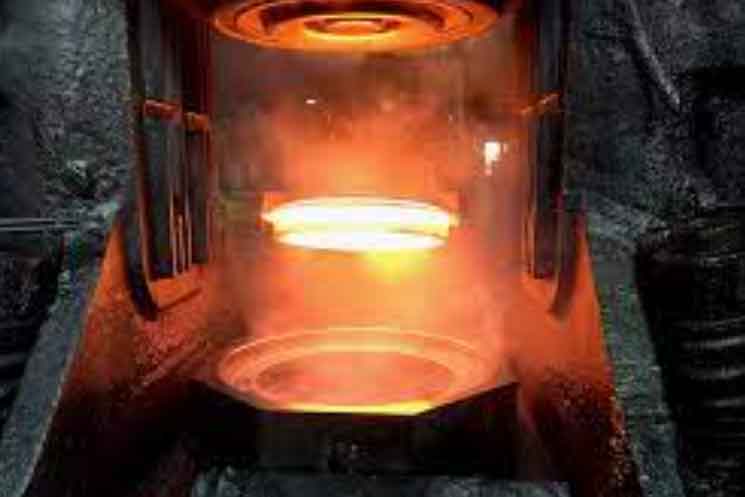
Gear forgings are indeed considered the future of gear manufacturing due to their numerous advantages over traditional gear manufacturing methods. By utilizing forging techniques, gears can be produced with enhanced strength, improved material properties, and higher precision. Here are some key aspects that make gear forgings the future of gear manufacturing:
Superior Strength:
Forged gears exhibit exceptional strength and durability compared to gears produced through other methods such as casting or machining. The forging process involves shaping metal under extreme pressure, resulting in a dense and uniform grain structure. This enhances the gear’s load-carrying capacity, resistance to wear, and overall performance.
Enhanced Material Properties:
Forging allows the utilization of various high-performance alloys and specialty materials, such as steel, titanium, or superalloys. These materials offer superior mechanical properties, including high tensile strength, improved fatigue resistance, and better heat resistance. Gear forgings can be tailored to meet specific requirements and operating conditions, leading to enhanced performance in critical applications.
Precision and Consistency:
With advancements in forging technologies, the dimensional accuracy and consistency of gear forgings have significantly improved. Computer-controlled forging processes, such as closed-die or precision forging, ensure tight tolerances, reduced dimensional variations, and consistent quality across production batches. This level of precision is vital for gears to mesh smoothly and efficiently, minimizing noise, vibration, and potential failure risks.
Cost-effectiveness:
While gear forgings may have higher upfront costs compared to alternative manufacturing methods, they often prove to be more cost-effective in the long run. The superior strength and durability of forged gears result in reduced maintenance requirements, longer service life, and decreased downtime. Additionally, the ability to forge near-net shapes minimizes material waste and machining operations, optimizing material utilization and reducing overall manufacturing costs.
Complex Geometries:
Forging enables the production of gears with intricate and complex geometries that are challenging to achieve through other manufacturing techniques. The ability to forge near-net shapes reduces the need for extensive machining, which can be time-consuming and costly. This opens up possibilities for innovative gear designs and customization to meet specific application requirements.
Sustainability:
Gear forgings align with the growing focus on sustainable manufacturing practices. The forging process typically requires less energy compared to other methods like casting or machining. Additionally, the ability to use recycled materials or environmentally friendly alloys further contributes to reducing the environmental impact associated with gear manufacturing.
Gear forgings offer superior strength, enhanced material properties, precision, cost-effectiveness, and the ability to produce complex geometries. These advantages make gear forgings a promising technology that will shape the future of gear manufacturing, particularly in demanding industries such as automotive, aerospace, power generation, and heavy machinery.