Gear hobbing is a widely used gear manufacturing process that involves the cutting of gear teeth using a specialized cutting tool called a hob. Let’s explore the theoretical principles and practical steps involved in gear hobbing:
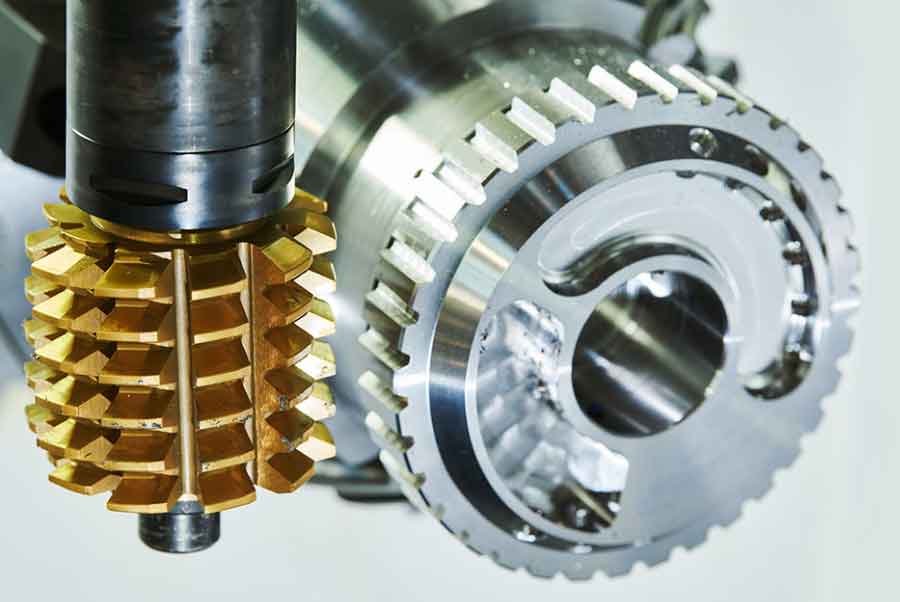
- Gear Hobbing Theory:
- Gear Tooth Generation: Gear hobbing follows the principle of generating gear teeth by the continuous reciprocal motion of the hob and the rotational motion of the workpiece.
- Hob Design: The hob is designed with the inverse tooth profile of the desired gear. It has multiple cutting edges that progressively engage with the workpiece to generate the gear teeth.
- Gear Hobbing Machine: Gear hobbing is performed on a gear hobbing machine, which consists of a hob spindle, workpiece spindle, and various mechanisms for tool movement, workpiece rotation, and feed control.
- Gear Hobbing Process Steps:
- Setup: Mount the hob on the hob spindle and secure the workpiece on the workpiece spindle. Ensure proper alignment and centering of the hob and workpiece.
- Gear Data Input: Input the necessary gear parameters such as module, number of teeth, pressure angle, and helix angle into the gear hobbing machine’s control system.
- Machine Settings: Set the cutting speed, feed rate, and depth of cut based on the gear specifications, material, and desired surface finish. Ensure appropriate lubrication or coolant supply to maintain cutting efficiency and reduce heat.
- Workpiece Rotation: Start the rotation of the workpiece spindle, which drives the workpiece rotation for gear tooth generation.
- Hob Movement: Activate the hob spindle to rotate the hob. The hob is fed towards the workpiece to progressively cut the gear teeth.
- Gear Cutting: The cutting edges of the hob engage with the workpiece, gradually removing material and forming the gear teeth. The hob and workpiece movements are synchronized to maintain proper tooth spacing and tooth profile accuracy.
- Completion and Inspection: After completing the cutting process, stop the hob and workpiece rotation. Inspect the gear for tooth profile accuracy, tooth spacing, surface finish, and other critical dimensions using appropriate measuring and inspection equipment.
- Factors Affecting Gear Hobbing:
- Hob Design: The design of the hob, including tooth profile accuracy, chip clearance, and relief angles, impacts the quality of the gear teeth.
- Cutting Parameters: Cutting speed, feed rate, and depth of cut need to be optimized to achieve the desired gear quality, balancing productivity and tool life.
- Material Selection: Gear hobbing can be performed on various materials, including steel, cast iron, and non-ferrous alloys. Material properties influence cutting parameters and tool selection.
- Machine Rigidity: The rigidity and stability of the gear hobbing machine play a crucial role in achieving accurate gear tooth generation and minimizing vibration.
- Tool Maintenance: Regular inspection, sharpening, and replacement of hobs are essential to maintain consistent cutting performance and gear quality.
Gear hobbing is a versatile and efficient method for manufacturing a wide range of gears. It combines theoretical principles with precise machine operation to produce high-quality gears with accurate tooth profiles, proper tooth spacing, and excellent surface finish. Mastering the gear hobbing process requires a combination of knowledge, experience, and attention to detail to achieve optimal gear manufacturing results.