Gear hobbing is a widely used gear manufacturing process that plays a critical role in producing high-quality gears for various industries. To ensure optimal gear quality and performance, there are several key considerations that manufacturers should take into account. This article highlights these considerations, providing insights into how they contribute to achieving superior gear characteristics.
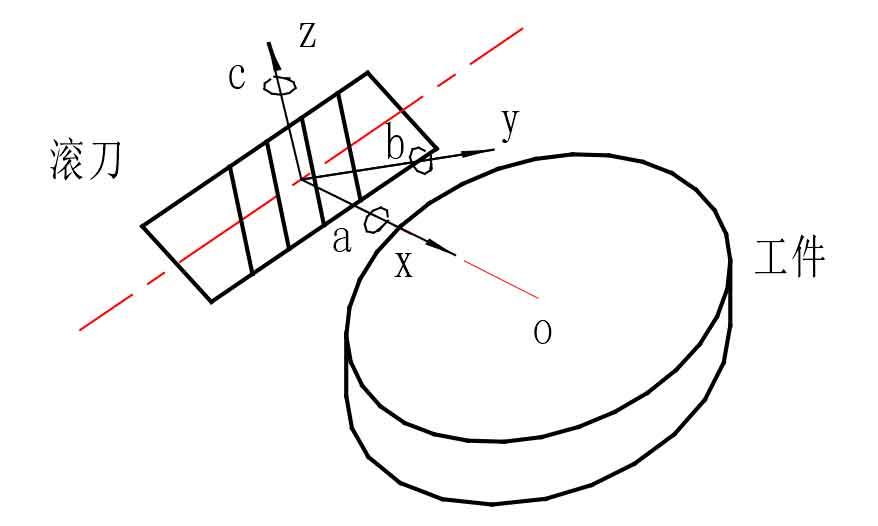
- Material Selection:
Choosing the right material is crucial for gear performance. Factors such as strength, wear resistance, and heat treatment response should be considered. Common gear materials include alloy steels, stainless steels, and non-ferrous alloys. Selecting the appropriate material based on the gear’s application and operating conditions is essential for achieving the desired gear quality and longevity.
- Design Considerations:
- Gear Tooth Profile: The gear tooth profile determines the gear’s engagement characteristics, load distribution, and noise generation. Optimizing the tooth profile, such as involute or custom-designed profiles, ensures proper meshing, efficient power transmission, and reduced noise levels.
- Tooth Geometry: Considerations such as tooth size, pitch, pressure angle, and addendum modification factor impact gear performance. These parameters should be carefully designed to meet the desired load capacity, contact ratio, and tooth strength requirements.
- Hob Selection and Tooling:
- Hob Design: The selection of the appropriate hob is critical to achieving the desired gear tooth profile accuracy and surface finish. Factors such as hob geometry, number of teeth, and helix angle should be carefully considered based on the gear specifications.
- Tool Wear and Maintenance: Regular inspection and maintenance of hobbing tools are essential for maintaining gear quality. Proper tool sharpening, reconditioning, and replacement at the right intervals help ensure consistent performance and avoid defects in the produced gears.
- Machine Parameters and Setup:
- Cutting Speed and Feed Rate: Optimizing the cutting speed and feed rate based on the gear material and hardness is crucial for achieving the desired gear surface finish, dimensional accuracy, and chip formation. Proper selection and adjustment of these parameters help prevent tool wear and overheating.
- Workpiece Setup and Alignment: Precise workpiece mounting and alignment are essential to ensure accurate gear tooth profiles and minimize runout. Proper setup and alignment prevent gear eccentricity, misalignment, and uneven tooth contact, resulting in improved gear quality and performance.
- Inspection and Quality Control:
- In-Process Inspection: Conducting regular in-process inspections using precision measuring instruments helps monitor gear quality during the hobbing process. This enables timely adjustments and corrections to maintain gear accuracy and prevent manufacturing defects.
- Final Inspection: Performing comprehensive final inspections using specialized equipment, such as coordinate measuring machines (CMMs), ensures that the finished gears meet all required specifications, including tooth profile, dimensions, surface finish, and hardness.
Optimal gear quality and performance in gear hobbing rely on various key considerations, including material selection, design considerations, hob selection, machine parameters, and inspection processes. By paying close attention to these factors, gear manufacturers can produce gears that meet stringent quality standards, exhibit excellent performance characteristics, and fulfill the requirements of diverse applications. Implementing a robust quality control system throughout the gear hobbing process ensures the consistent production of high-quality gears, contributing to the reliability and longevity of mechanical systems that rely on precise and efficient power transmission.