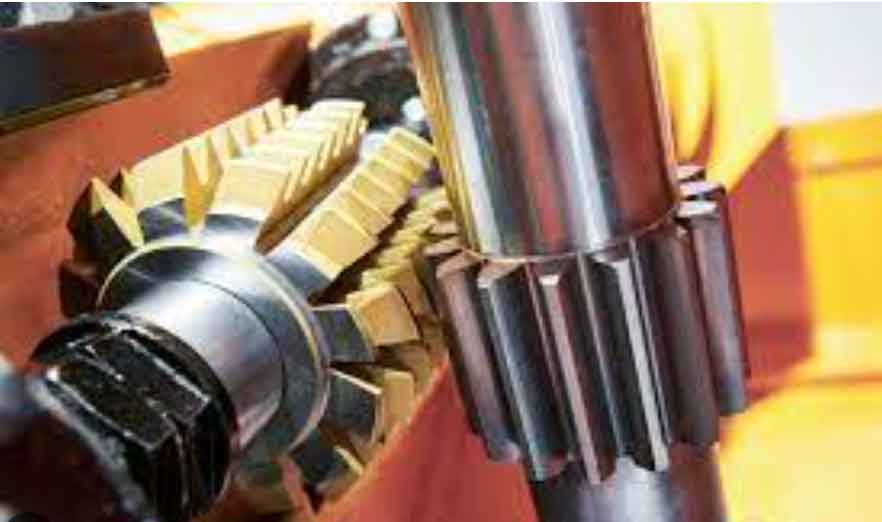
Gear hobbing machines have evolved significantly over the years, incorporating advanced technologies to improve productivity, accuracy, and versatility. These advancements have been instrumental in meeting the demands of various industries for high-quality gears. Here are some key advancements and modern technologies in gear hobbing machines:
1. CNC Technology:
Computer Numerical Control (CNC) technology has revolutionized gear hobbing machines, enabling precise and automated control of the cutting process. CNC gear hobbing machines use computer programming to set up gear profiles, cutting depths, and other parameters, leading to consistent and repeatable gear production.
2. Multi-Axis Capability:
Modern gear hobbing machines often feature multi-axis capability, allowing for the simultaneous movement of multiple axes during the hobbing process. This enhances the machine’s flexibility, enabling the production of more complex gear geometries and reducing the need for multiple setups.
3. Direct-Drive Technology:
Some gear hobbing machines now incorporate direct-drive technology, where the hob and workpiece are directly driven by high-torque motors. This design eliminates the need for intermediate transmission components, reducing backlash and improving accuracy.
4. High-Speed Hobbing:
Advancements in cutting tool materials and machine dynamics have enabled high-speed gear hobbing. High-speed hobbing reduces cutting time, improves productivity, and can result in better surface finishes.
5. In-Process Measurement and Inspection:
Modern gear hobbing machines often come equipped with in-process measurement and inspection systems. These systems allow real-time monitoring and adjustment of gear profiles, ensuring the gears meet the required specifications.
6. Automation and Robotics:
Automation and robotics have been integrated into gear hobbing machines to streamline the loading and unloading of workpieces, reducing setup times and enhancing overall productivity. Robotic systems can also be used for tool changing and other auxiliary tasks.
7. Simulation and Virtual Prototyping:
Computer simulation and virtual prototyping tools have become essential for optimizing gear hobbing processes. These tools help in designing and analyzing gear profiles, identifying potential issues, and optimizing cutting parameters before physical machining begins.
8. Advanced Cutting Tools and Coatings:
Advancements in cutting tool materials and coatings have improved tool life and cutting performance in gear hobbing. High-speed steel (HSS), carbide, and cubic boron nitride (CBN) hobs, along with various coatings, offer enhanced wear resistance and cutting efficiency.
9. Industry 4.0 Integration:
Gear hobbing machines are increasingly being connected to Industry 4.0 networks, allowing for data collection, analysis, and predictive maintenance. This integration facilitates smart manufacturing and improves machine uptime and performance.
10. Eco-Friendly Solutions:
Some gear hobbing machines now incorporate eco-friendly features, such as energy-saving technologies and environmentally friendly lubricants, to reduce the environmental impact of gear manufacturing processes.
These advancements in gear hobbing machines have significantly enhanced the efficiency, accuracy, and capabilities of gear manufacturing. As technology continues to progress, gear hobbing machines are expected to further evolve, meeting the ever-increasing demands for precision gears in various industries.