Gear hobbing is a key process in gear production, and maximizing efficiency and productivity is crucial for achieving cost-effective manufacturing. Here are some strategies to maximize efficiency and productivity in gear hobbing:
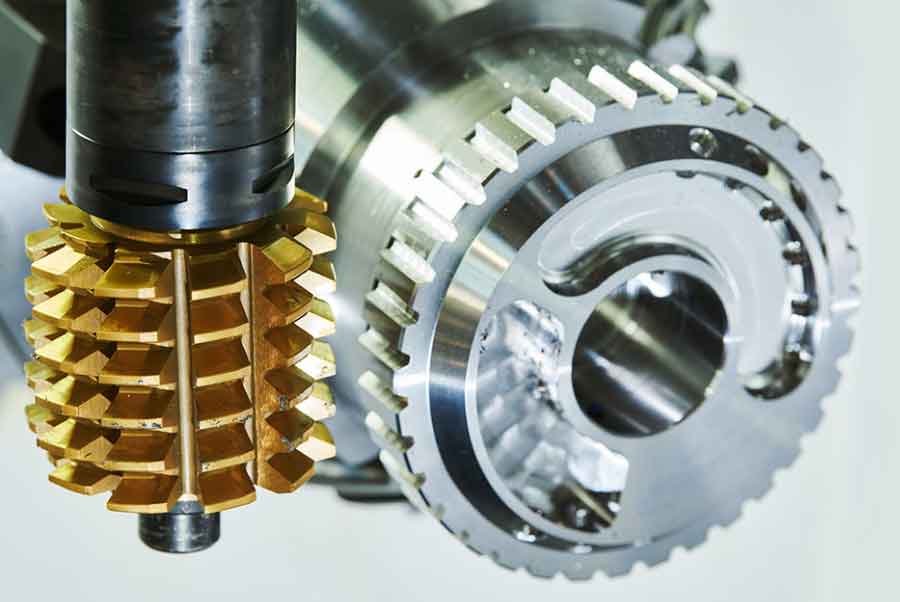
- Optimize Cutting Parameters: Analyze the gear specifications, material properties, and desired surface finish to determine the optimal cutting parameters such as cutting speed, feed rate, and depth of cut. Finding the right balance between productivity and tool life is essential. Higher cutting speeds and feed rates can increase productivity, but they should be within the limits of the machine and tool capabilities.
- High-Quality Tooling: Invest in high-quality hobs and cutting tools that are specifically designed for gear hobbing. Choose tools with the appropriate tooth geometry, material, and coatings for the gear material and cutting conditions. High-quality tools will provide better performance, longer tool life, and more consistent gear quality.
- Proper Machine Setup: Ensure the gear hobbing machine is properly set up and calibrated. Align the machine components accurately, including the hob, workpiece spindle, and tooling. Proper alignment helps minimize vibrations, maximize cutting performance, and enhance gear quality. Regular machine maintenance and calibration are essential to ensure optimal performance.
- Implement Process Monitoring and Control: Utilize process monitoring and control systems to monitor key parameters such as cutting forces, tool wear, and temperature. Real-time monitoring helps identify potential issues and allows for timely adjustments to optimize the process. Implement feedback mechanisms to automatically adjust cutting parameters or halt the process if deviations exceed acceptable limits.
- Minimize Setup Time: Reduce the setup time between gear changeovers by implementing efficient tool change systems and standardized workholding setups. Minimizing setup time allows for more productive machine utilization and faster gear production.
- Efficient Chip Evacuation: Proper chip evacuation is essential for maintaining a clean cutting zone and preventing chip buildup, which can lead to poor surface finish and tool wear. Use suitable chip breakers, chip conveyors, or chip evacuation systems to ensure efficient chip removal.
- Advanced Machine Features: Explore gear hobbing machines with advanced features such as multiple-axis control, automatic tool changers, and integrated measurement systems. These features can streamline the production process, enhance accuracy, and reduce non-cutting time.
- Continuous Improvement: Foster a culture of continuous improvement by regularly reviewing the gear hobbing process, identifying bottlenecks, and implementing efficiency-enhancing measures. Encourage feedback and suggestions from machine operators and maintenance personnel to optimize the process and increase productivity.
- Operator Training: Invest in operator training programs to ensure that machine operators have a deep understanding of the gear hobbing process, machine capabilities, and tooling. Well-trained operators can effectively troubleshoot issues, optimize cutting parameters, and maximize productivity.
- Collaboration with Suppliers: Work closely with tooling suppliers and machine manufacturers to stay updated on the latest advancements in gear hobbing technology. Collaborating with experienced partners can provide valuable insights, support, and access to innovative solutions.
By implementing these strategies, gear manufacturers can enhance the efficiency and productivity of gear hobbing processes, resulting in increased output, improved quality, and reduced production costs. Regular evaluation, monitoring, and continuous improvement efforts are key to sustaining high levels of efficiency and productivity in gear production.