Gear hobbing is a widely used gear manufacturing process that involves cutting gear teeth using a hobbing machine. One critical aspect of gear hobbing is optimizing the gear tooth profiles to enhance gear efficiency and performance. This article explores the importance of optimizing gear tooth profiles in gear hobbing and discusses key strategies to improve gear efficiency.
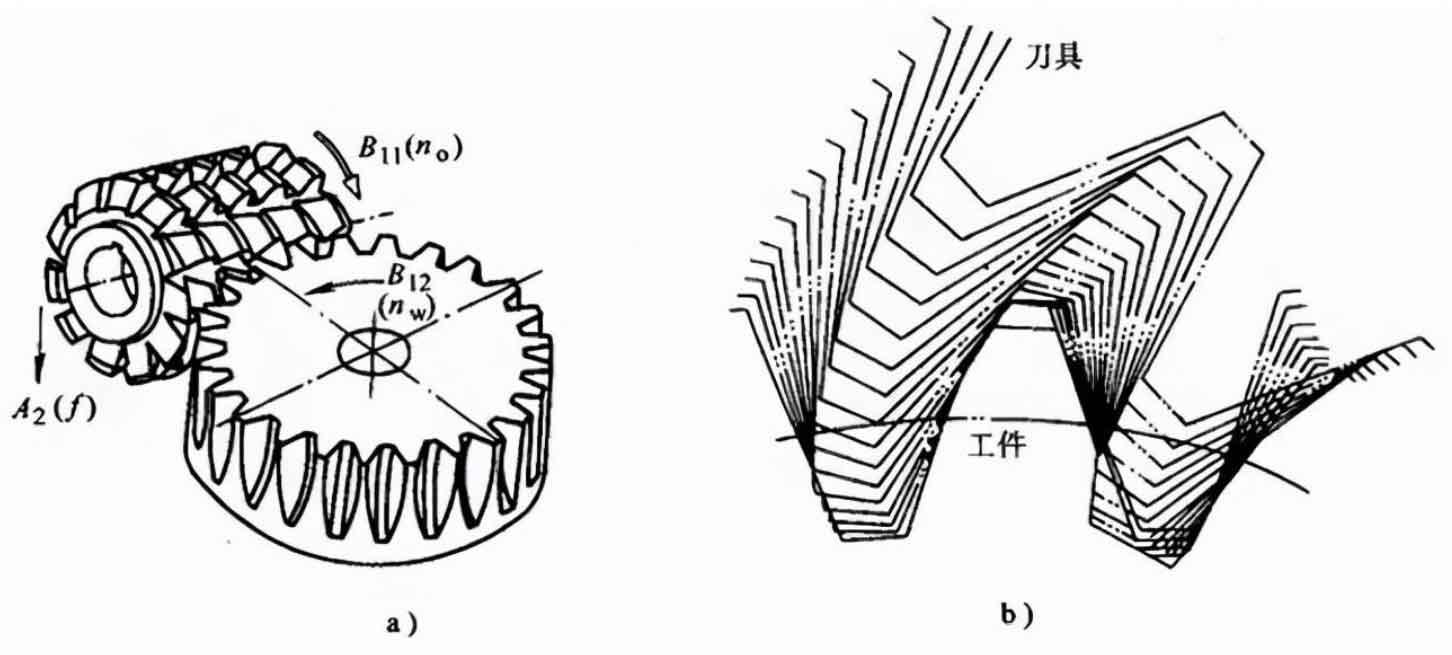
1.Understanding Gear Tooth Profiles:
Gear tooth profiles, such as involute, are crucial for efficient power transmission and smooth gear meshing. The correct tooth profile ensures proper load distribution, minimal friction, and reduced wear. Optimizing the gear tooth profiles involves fine-tuning the tooth geometry to maximize efficiency.
2.Tooth Profile Modifications:
To improve gear efficiency, gear hobbing can incorporate tooth profile modifications, such as tip relief, crowning, and profile shifting. These modifications optimize the contact pattern and load distribution across the gear teeth, minimizing edge contact, and enhancing gear performance.
- Tip Relief: By relieving the tooth profile near the tip, tip relief reduces interference and edge contact during gear meshing. This minimizes stress concentration and improves gear life.
- Crowning: Crowning involves slightly modifying the gear tooth profile to create a convex or concave shape along the tooth width. Crowning compensates for misalignments, deflections, and load variations, ensuring uniform contact and load distribution across the gear face width.
- Profile Shifting: Profile shifting involves shifting the gear tooth profile relative to the mating gear. It can adjust the gear center distance, optimize tooth contact, and control backlash. Profile shifting is beneficial for achieving specific gear performance requirements, such as noise reduction or increased torque capacity.
3.Advanced Simulation and Modeling:
To optimize gear tooth profiles, advanced simulation and modeling techniques can be employed. Computer-aided design (CAD) software and gear design analysis tools allow engineers to simulate gear meshing and analyze tooth contact patterns, pressure angles, and tooth stresses. Through virtual prototyping, engineers can iteratively refine gear tooth profiles to achieve the desired efficiency and performance.
4.Material Selection and Heat Treatment:
Optimizing gear tooth profiles also involves considering the material properties and heat treatment processes. Proper material selection ensures the necessary strength, durability, and resistance to wear and fatigue. Heat treatment processes, such as carburizing or induction hardening, can further enhance the gear’s surface hardness and toughness, improving gear efficiency and lifespan.
5.Lubrication and Maintenance:
Efficient gear operation relies on proper lubrication and regular maintenance. Adequate lubrication reduces friction and wear between the gear teeth, improving efficiency. Regular inspections and maintenance help identify any gear tooth damage, wear, or misalignments, allowing for timely corrective actions to preserve gear efficiency.
Optimizing gear tooth profiles in gear hobbing is essential for achieving improved gear efficiency and performance. Tooth profile modifications, such as tip relief, crowning, and profile shifting, help optimize load distribution, minimize stress concentration, and enhance gear life. Advanced simulation and modeling techniques aid in refining gear tooth profiles to achieve desired performance characteristics. Material selection, heat treatment, lubrication, and maintenance practices further contribute to efficient gear operation. By implementing these strategies, manufacturers can optimize gear tooth profiles during the gear hobbing process, resulting in gears that offer enhanced efficiency, durability, and overall performance in various applications.