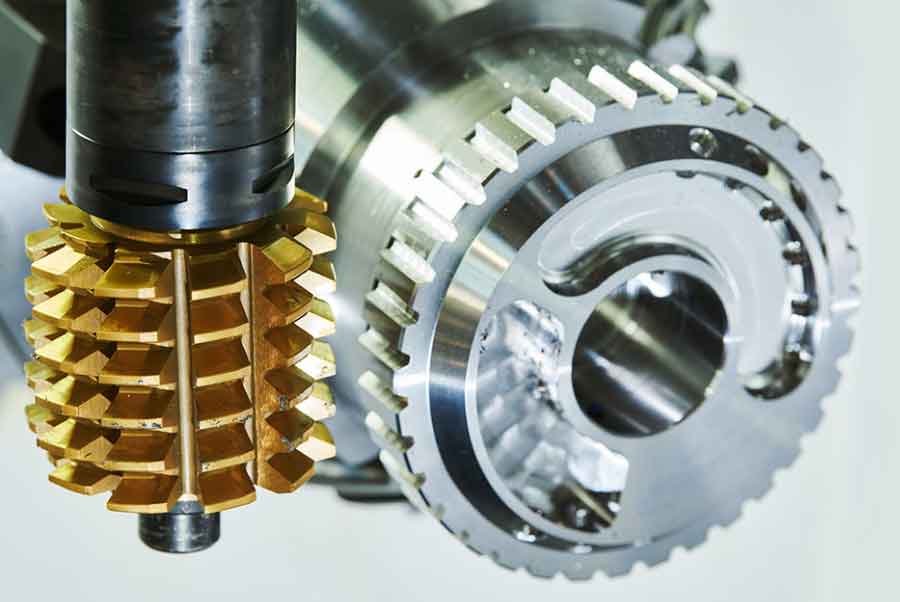
Gear hobbing machines have played a pivotal role in revolutionizing the gear manufacturing industry. These specialized machines have undergone significant advancements, offering increased precision, productivity, and versatility. This article explores how gear hobbing machines have transformed gear manufacturing and highlights their key contributions to the industry.
I. Enhanced Precision:
Gear hobbing machines have greatly improved the precision of gear manufacturing. Advanced control systems and servo motors provide precise positioning and movement of the cutting tool and workpiece. This level of control ensures accurate tooth profiles, precise tooth spacing, and consistent gear quality. Tighter tolerances can be achieved, enabling gears to meet the stringent requirements of modern applications.
II. Increased Productivity:
Gear hobbing machines have significantly increased productivity in gear manufacturing. CNC (Computer Numerical Control) technology enables automated and programmable operation, reducing setup times and allowing for efficient production. Multiple axes of motion and simultaneous machining operations further enhance productivity by reducing cycle times and eliminating the need for additional setups. These machines can handle a wide range of gear sizes and types, enabling manufacturers to produce gears in large quantities with improved efficiency.
III. Versatility in Gear Production:
Gear hobbing machines offer remarkable versatility in gear production. They can produce a variety of gear types, including spur gears, helical gears, worm gears, and splines. With the ability to generate complex gear tooth profiles and accommodate various gear specifications, gear hobbing machines cater to diverse industry needs. The flexibility to produce gears of different sizes, module/pitch, pressure angles, and helix angles ensures the suitability of these machines for a wide range of applications.
IV. Advanced Control Systems:
Modern gear hobbing machines incorporate advanced control systems that enhance performance and ease of use. CNC technology allows for precise control over cutting parameters, tool movements, and feed rates. Operators can program complex gear profiles and make adjustments on the fly, ensuring efficient and accurate production. Additionally, real-time monitoring and diagnostics enable timely identification of issues, reducing downtime and improving overall machine performance.
V. Integration with Automation:
Gear hobbing machines have seamlessly integrated with automation technologies, further streamlining gear manufacturing processes. Robots, gantry loaders, and conveyor systems can be integrated with gear hobbing machines for automated loading and unloading of workpieces. This integration increases productivity, reduces manual intervention, and enhances overall process efficiency. The combination of gear hobbing machines and automation paves the way for lights-out manufacturing and continuous production.
VI. Advancements in Tooling:
Gear hobbing machines have also benefited from advancements in tooling technology. High-performance hob cutters with advanced coatings and geometries improve cutting efficiency, extend tool life, and enhance gear quality. The development of custom tooling solutions and tool management systems allows for rapid tool changes and optimization of cutting processes. These advancements in tooling contribute to improved performance and cost-effectiveness of gear hobbing machines.
VII. Integration with Industry 4.0:
Gear hobbing machines are increasingly being integrated into the concepts of Industry 4.0. Connectivity, data exchange, and smart manufacturing principles are being implemented to monitor and optimize gear hobbing processes. Integration with manufacturing execution systems (MES), data analytics, and IoT devices enables real-time monitoring, predictive maintenance, and remote diagnostics. This integration enhances productivity, quality control, and overall equipment effectiveness.
Gear hobbing machines have revolutionized the gear manufacturing industry by offering enhanced precision, increased productivity, and versatility in gear production. Through advanced control systems, automation integration, and advancements in tooling, these machines have enabled manufacturers to produce gears with higher quality, tighter tolerances, and improved efficiency. The integration of gear hobbing machines with Industry 4.0 principles further augments their capabilities and ensures continued advancements in gear manufacturing technology. Gear hobbing machines are poised to play a crucial role in meeting the evolving demands of industries that rely on high-quality gears.