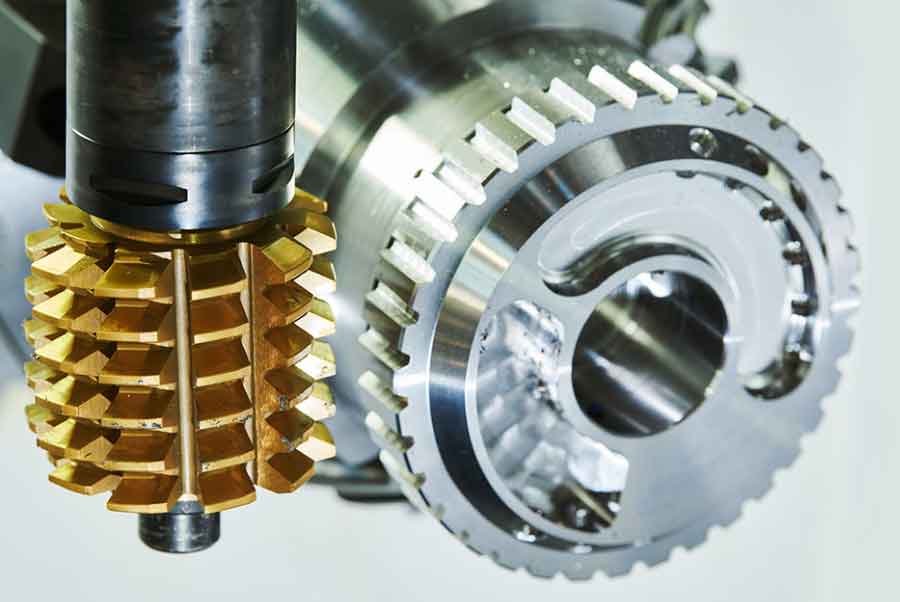
Gear hobbing is a widely used and versatile gear manufacturing process that involves cutting gear teeth using a specialized tool called a hob. This comprehensive guide provides an overview of gear hobbing, covering its principles, equipment, process steps, and key considerations in gear manufacturing.
I. Gear Hobbing Principles:
Gear hobbing is based on the principle of generating gears by the continuous engagement between the hob and the rotating gear blank. The hob’s cutting edges gradually form the gear teeth through a combination of axial and rotational movements. The tooth profile of the hob determines the final shape of the gear teeth.
II. Gear Hobbing Equipment:
Gear hobbing requires specialized equipment known as gear hobbing machines. These machines consist of several components, including a hob spindle, work spindle, hob head, hob slide, work table, and various control systems. The machine’s design and capabilities determine the size, complexity, and precision of gears that can be produced.
III. Gear Hobbing Process Steps:
The gear hobbing process involves several essential steps:
- Gear Blank Setup: The gear blank, typically a cylindrical workpiece, is securely mounted on the work spindle. It must be aligned and positioned correctly to ensure accurate gear tooth cutting.
- Hob Mounting: The hob is mounted on the hob head, which positions it correctly relative to the gear blank. The hob’s size, tooth profile, and other specifications should match the desired gear tooth geometry.
- Cutting Parameters Selection: Cutting parameters such as hob speed, workpiece rotation speed, feed rate, and depth of cut are determined based on the gear specifications, material, and desired accuracy.
- Cutting Operation: The hob head and work table are synchronized to produce the desired gear tooth profile. The hob moves axially across the gear blank while the gear blank rotates, gradually cutting the gear teeth. The process continues until all teeth are cut.
- Finishing Operations: Depending on the desired gear quality, additional finishing operations such as gear shaving, grinding, or honing may be performed to improve tooth surface finish, accuracy, and noise characteristics.
IV. Key Considerations in Gear Hobbing:
- Material Selection: The choice of gear material depends on the application requirements, including strength, wear resistance, and operating conditions. Common materials include alloy steels, stainless steels, and non-ferrous alloys.
- Hob Design and Selection: The hob must be designed to match the desired tooth profile, pressure angle, helix angle, and module or pitch of the gear. Factors like hob material, coatings, and geometry influence tool life, cutting efficiency, and gear quality.
- Accuracy and Precision: Gear hobbing requires precise control over cutting parameters, machine movements, and tool geometry to achieve accurate gear tooth profiles and minimize deviations. Proper setup, calibration, and measurement techniques are critical for maintaining gear accuracy.
- Tool Life and Maintenance: Hob wear affects gear quality and productivity. Regular inspection, re-sharpening, and replacement of worn-out hobs are essential to maintain optimal cutting performance. Proper lubrication and cooling systems help extend tool life.
- Process Optimization: Continuous improvement in gear hobbing involves optimizing cutting parameters, minimizing cycle times, reducing setup and changeover times, and implementing automation and advanced control systems to enhance productivity and efficiency.
Gear hobbing is a fundamental process in gear manufacturing, offering versatility, precision, and efficiency. By understanding the principles, equipment, process steps, and key considerations in gear hobbing, manufacturers can produce high-quality gears that meet specific application requirements. Gear hobbing, coupled with advancements in machine technology, tool design, and process optimization, continues to drive innovation in gear manufacturing and enables the production of complex, reliable gears for various industries.