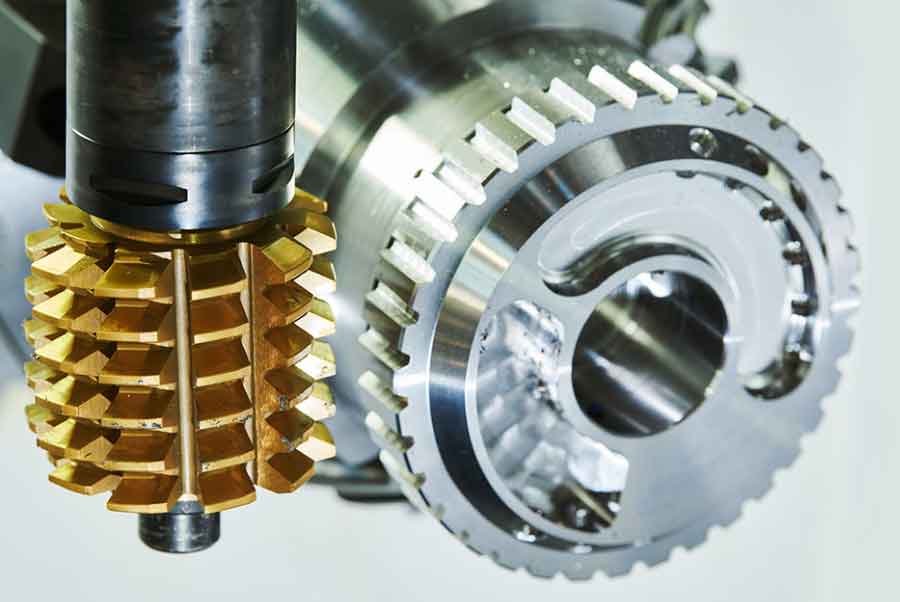
Gear hobbing is a fundamental process in precision gear manufacturing that enables the production of high-quality gears with accurate tooth profiles. This article explores the gear hobbing process, its key components, and its significance in achieving precision in gear manufacturing.
I. Overview of Gear Hobbing:
Gear hobbing is a machining process used to produce cylindrical gears, splines, and sprockets. It involves the use of a specialized cutting tool called a hob, which is a cylindrical-shaped cutter with equally spaced cutting teeth. The hob rotates and moves axially across the gear blank, gradually forming the gear teeth through the cutting action.
II. Gear Hobbing Machine:
The gear hobbing machine is a specialized machine tool designed for the gear hobbing process. It consists of several essential components, including a spindle to hold the gear blank, a hob head that carries the hob cutter, a hob slide for axial movement, and a work table for rotational movement of the gear blank. The machine also incorporates various mechanisms for controlling the speed, feed, and depth of cut.
III. Hob Design and Selection:
The design and selection of the hob play a crucial role in achieving precision in gear hobbing. Hobs are carefully designed to match the desired tooth profile, pressure angle, helix angle, and module or pitch of the gear. They come in different sizes and configurations to accommodate various gear specifications. The correct hob selection ensures accurate gear tooth geometry and optimal performance.
IV. Cutting Process:
During the gear hobbing process, the hob cutter engages with the gear blank, gradually removing material to form the gear teeth. The gear blank rotates while the hob moves axially across it, generating the desired tooth profile. The cutting action is precise and controlled, resulting in the accurate shape and spacing of gear teeth.
V. Feed Mechanism:
The feed mechanism in a gear hobbing machine controls the rate at which the hob advances across the gear blank. It determines the pitch or spacing between the gear teeth and influences the surface finish and accuracy of the gear. The feed mechanism must be carefully calibrated and synchronized with the rotation of the gear blank to achieve precise tooth spacing.
VI. Tooth Profile Accuracy:
Gear hobbing is renowned for its ability to achieve excellent tooth profile accuracy. The hob cutter’s shape and the machine’s synchronized movements ensure the gear teeth match the desired tooth profile with high precision. This accuracy is crucial for smooth and efficient power transmission, minimal noise and vibration, and optimal gear performance.
VII. Finishing Operations:
After the gear hobbing process, additional finishing operations may be performed to further refine the gear’s surface finish and accuracy. These operations can include gear shaving, gear grinding, or gear honing. Finishing processes remove any remaining imperfections and ensure the gear meets the required tolerances and surface quality standards.
VIII. Advantages of Gear Hobbing:
Gear hobbing offers several advantages in precision gear manufacturing. It allows for efficient production of gears with accurate tooth profiles and high repeatability. It is suitable for a wide range of gear sizes, from small to large. Gear hobbing is also a cost-effective process, as it can produce gears in large quantities with minimal material wastage.
Gear hobbing is a vital process in precision gear manufacturing that enables the production of high-quality gears with accurate tooth profiles. With the use of specialized hob cutters, precise machine movements, and careful control of feed mechanisms, gear hobbing achieves excellent tooth profile accuracy, ensuring smooth and efficient power transmission. The gear hobbing process, coupled with additional finishing operations, results in precision gears that meet the stringent requirements of various industries, including automotive, aerospace, and industrial machinery.