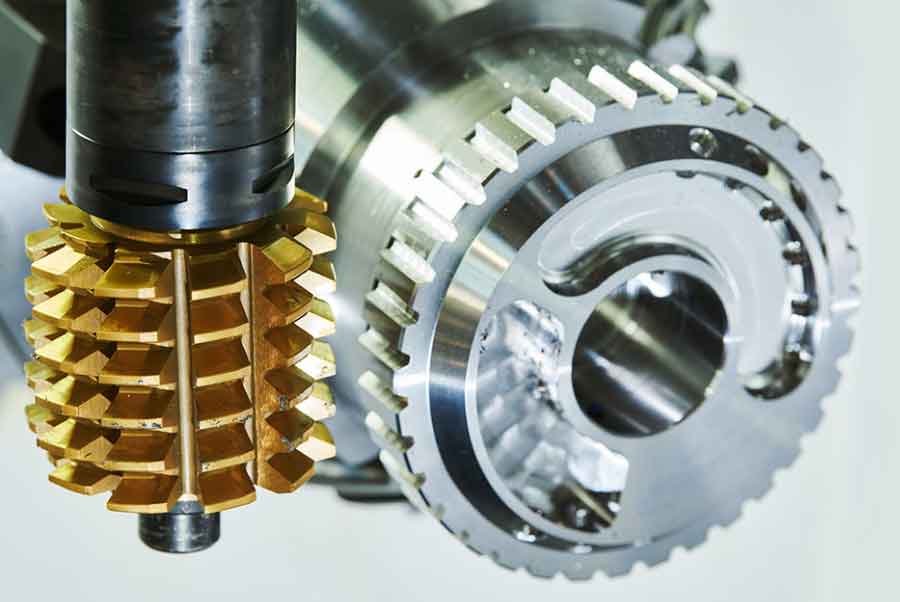
Gear hobbing is a crucial manufacturing process that plays a key role in producing reliable and high-performance gears. It involves the precise cutting of gear teeth using a hobbing machine, resulting in gears with accurate tooth profiles, excellent surface finish, and optimized performance characteristics. This article explores how gear hobbing serves as the key to achieving gears that are reliable, efficient, and capable of withstanding demanding applications.
I. Precise Tooth Profiles:
Gear hobbing allows for the creation of gears with precise tooth profiles, which are essential for smooth and efficient gear engagement. The hobbing process ensures that each gear tooth is accurately formed, resulting in consistent tooth spacing, proper involute shape, and precise pitch diameter. These factors contribute to minimal backlash, efficient power transmission, and reduced noise and vibration.
II. Excellent Surface Finish:
Gear hobbing enables the production of gears with excellent surface finish, which is crucial for their performance and longevity. The cutting action of the hob generates smooth tooth surfaces with controlled roughness. This leads to reduced friction, improved lubrication distribution, and enhanced wear resistance. The superior surface finish achieved through gear hobbing minimizes the risk of surface fatigue and increases gear durability.
III. Wide Range of Gear Types:
Gear hobbing is versatile and capable of producing a wide range of gear types, including spur gears, helical gears, worm gears, and more. The flexibility of gear hobbing machines allows for the production of gears with various tooth configurations and geometries to suit specific application requirements. Gear hobbing can accommodate different module/pitch sizes, pressure angles, helix angles, and gear ratios, providing manufacturers with the capability to produce gears for diverse applications.
IV. High Production Efficiency:
Gear hobbing is a highly efficient process, especially when it comes to high-volume production. Modern gear hobbing machines can perform continuous cutting operations, enabling the production of multiple gear teeth in a single pass. This results in increased productivity and reduced manufacturing time compared to other gear manufacturing methods. The efficiency of gear hobbing makes it well-suited for industries that require large quantities of gears, such as automotive and industrial equipment manufacturing.
V. Cost-Effective Manufacturing:
Gear hobbing offers cost-effective gear manufacturing compared to alternative processes. The ability to produce multiple gears simultaneously and the high repeatability of gear hobbing machines contribute to cost savings in terms of labor, time, and material waste. Gear hobbing also allows for the use of a wide range of materials, including both ferrous and non-ferrous alloys, providing manufacturers with flexibility in material selection based on application requirements and cost considerations.
VI. Reliability and Durability:
Gears produced through gear hobbing are known for their reliability and durability. The accurate tooth profiles, precise tooth engagement, and excellent surface finish achieved through gear hobbing contribute to the overall reliability and longevity of gears. Gears manufactured using gear hobbing techniques can withstand high loads, operate under demanding conditions, and maintain their performance characteristics over extended periods of use.
VII. Quality Control:
Gear hobbing facilitates quality control throughout the manufacturing process. Gear hobbing machines are equipped with advanced monitoring and inspection systems that ensure the accuracy and integrity of the produced gears. Regular inspections, including dimensional measurements, surface analysis, and gear tooth profile verification, help identify any deviations or errors and enable corrective actions to be taken. This rigorous quality control ensures that only high-quality gears meet the required specifications.
Gear hobbing is the key to achieving reliable and high-performance gears. Its ability to produce gears with precise tooth profiles, excellent surface finish, and optimized performance characteristics contributes to efficient power transmission, reduced noise and vibration, and increased gear durability. With its versatility, efficiency, and cost-effectiveness, gear hobbing remains a vital process in gear manufacturing for various industries, ensuring the production of gears that meet the demands of demanding applications.