Gear hobbing is a versatile manufacturing process that allows for the production of customized gears with specific characteristics tailored to meet unique application requirements. Here’s how gear hobbing unleashes the potential of customized gear manufacturing:
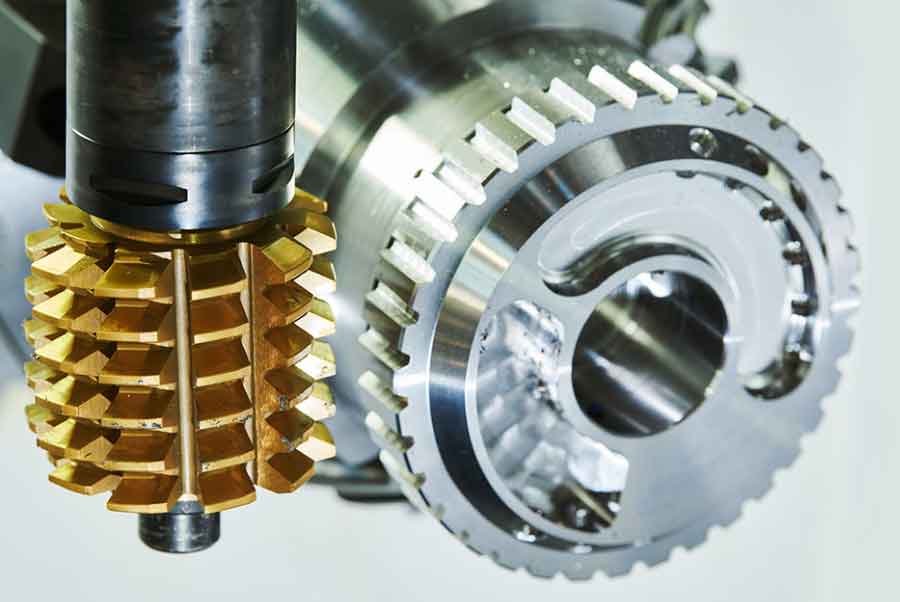
- Flexible Gear Design: Gear hobbing enables the production of gears with custom designs to match specific application needs. Whether it’s modifying the tooth profile, pressure angle, helix angle, or gear size, gear hobbing allows for flexibility in gear design. This flexibility ensures that gears can be optimized for efficient power transmission, precise motion control, or specific load-carrying capacities.
- Wide Range of Gear Types: Gear hobbing can produce various types of gears, including spur gears, helical gears, worm gears, and bevel gears. Each gear type offers unique advantages and is suited for specific applications. By utilizing gear hobbing, manufacturers can customize the gear type based on the desired functionality, space constraints, and load requirements of the application.
- Accurate Tooth Profile Generation: Gear hobbing excels in producing accurate gear tooth profiles. The hob’s cutting edges are precisely designed to generate the desired tooth shape and spacing. This accuracy ensures optimal gear meshing, minimizing noise, vibration, and wear. Customized tooth profiles can also be implemented to achieve specific gear characteristics, such as improved load distribution or reduced backlash.
- Material Selection for Performance: Customized gear manufacturing allows for the selection of materials that best suit the application’s demands. Different materials possess varying properties, such as strength, wear resistance, and fatigue resistance. By choosing the right material, manufacturers can optimize gear performance and durability. Gear hobbing can accommodate a wide range of materials, including various metals and alloys, enabling customization based on specific application requirements.
- Specialized Coatings and Treatments: Customized gears can benefit from specialized coatings and treatments to enhance their performance and longevity. Coatings like PVD (Physical Vapor Deposition) and DLC (Diamond-Like Carbon) can provide increased wear resistance and reduced friction. Heat treatments, such as case hardening or nitriding, can improve surface hardness and durability. Gear hobbing allows for the incorporation of these customized surface treatments into the manufacturing process.
- Prototype Development and Iteration: Gear hobbing facilitates the production of prototypes and iterative design improvements. Customized gear manufacturing enables manufacturers to quickly produce prototypes for testing and validation purposes. Based on the results, design iterations can be made to optimize gear performance before moving to full-scale production. This iterative approach allows for customized gear designs to be refined and fine-tuned for optimal performance.
- Efficient Production and Scalability: Gear hobbing offers efficient and scalable production capabilities. Once the customized gear design is finalized, gear hobbing machines can be programmed to produce gears in large quantities with consistent quality. The high cutting efficiency and continuous cutting action of gear hobbing make it suitable for both small-scale and large-scale production, ensuring the scalability of customized gear manufacturing.
- Quality Control and Inspection: Customized gear manufacturing requires stringent quality control measures to ensure that gears meet the specified design requirements. Gear hobbing allows for the implementation of quality control techniques, including in-process measurements, dimensional inspections, and surface finish assessments. These measures help maintain the desired gear accuracy, performance, and reliability.
By leveraging the capabilities of gear hobbing, manufacturers can unleash the potential of customized gear manufacturing. The ability to design gears according to specific application requirements, select suitable materials, incorporate specialized treatments, and optimize gear performance leads to tailored solutions that enhance efficiency, reliability, and overall system performance.