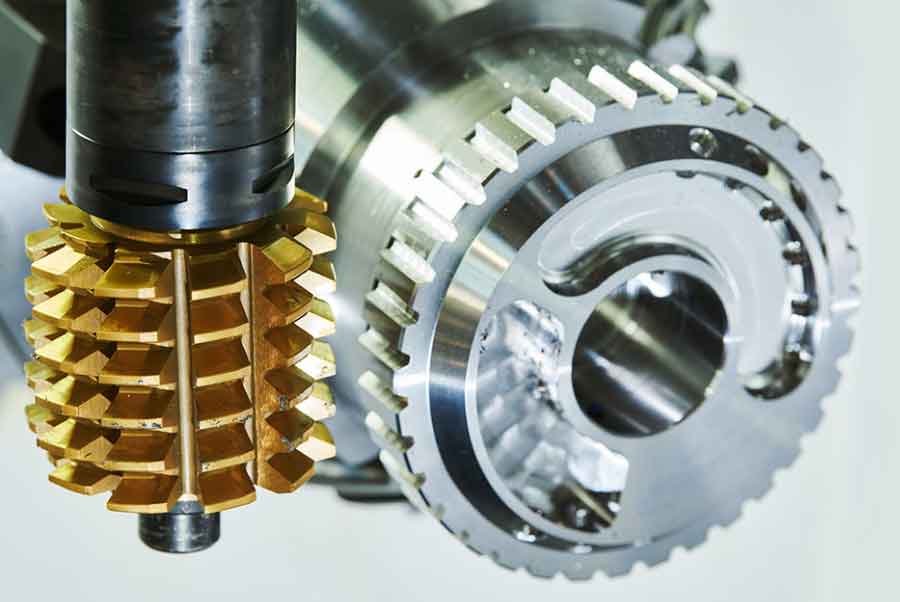
Gear hobbing is a powerful manufacturing process that unleashes the potential of high-quality gear production. It offers numerous advantages and plays a crucial role in various industries where gears are essential components. Let’s delve deeper into the potential and benefits of gear hobbing:
Precision and Accuracy:
Gear hobbing allows for the creation of gears with exceptional precision and accuracy. The process involves a controlled cutting action that ensures consistent tooth profiles, pitch, and spacing. This level of precision is vital for gears to mesh seamlessly and transmit motion efficiently.
Versatility:
Gear hobbing is a versatile process capable of producing a wide range of gear types, including spur gears, helical gears, worm gears, and more. It accommodates different gear configurations, tooth profiles, and sizes, making it suitable for various applications across industries.
Cost-Effectiveness:
Gear hobbing is a cost-effective method for gear production, especially for high-volume manufacturing. Once the hob and machine setup are in place, the process can efficiently produce gears at a relatively fast rate. It offers an economical solution without compromising on quality.
High Productivity:
Gear hobbing machines are designed for high productivity. They can generate multiple gear teeth in a single pass, thanks to the continuous rotation of the hob and indexing of the workpiece. This enables efficient production and shorter cycle times, contributing to increased productivity.
Strength and Durability:
Gears produced through hobbing exhibit excellent strength and durability. The cutting action of the hob removes material in a controlled manner, ensuring proper tooth engagement and load distribution. This results in gears that can withstand high torque, heavy loads, and prolonged use.
Scalability:
Gear hobbing is scalable to meet various production requirements. Whether it’s producing a small batch or large quantities of gears, the process can be easily adapted to cater to different production volumes. This scalability makes gear hobbing suitable for both custom and mass production needs.
Wide Material Compatibility:
Gear hobbing can be applied to a broad range of materials, including steel, cast iron, brass, bronze, and even some non-metallic materials. This flexibility allows manufacturers to select the most appropriate material for the specific application, considering factors like strength, wear resistance, and cost.
Enhanced Surface Finish:
Gear hobbing can produce gears with excellent surface finishes, reducing the need for additional post-processing operations. However, if a higher-quality finish is desired, gears can undergo secondary operations like deburring, honing, or grinding to achieve the desired surface texture.
Gear hobbing is a highly efficient and reliable process for manufacturing high-quality gears. Its ability to deliver precise, durable, and cost-effective gears has made it a preferred choice in industries such as automotive, aerospace, robotics, and industrial machinery. By unleashing the potential of gear hobbing, manufacturers can ensure the reliable performance of gears in various applications.