Gear hobbing is indeed a powerful method for high-quality gear production. It offers several benefits that contribute to the production of precise and reliable gears. Let’s delve deeper into the potential and advantages of gear hobbing:
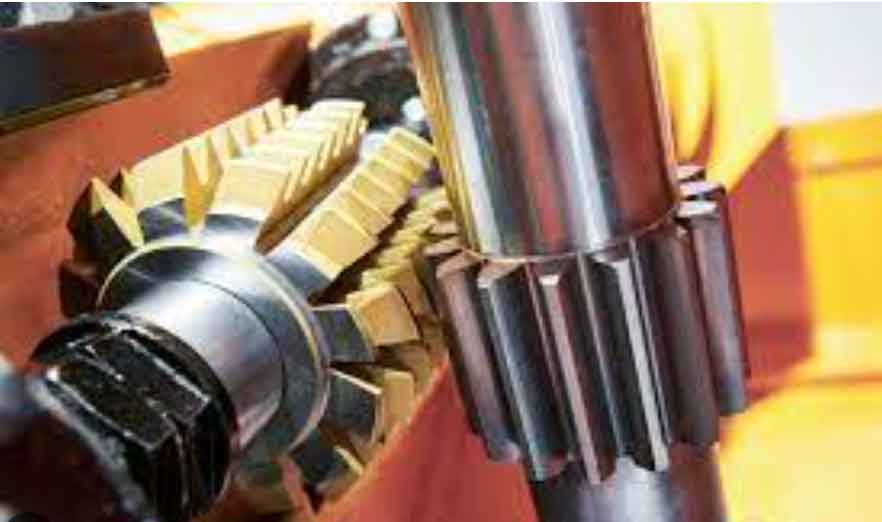
- Accuracy and Precision: Gear hobbing allows for exceptional accuracy and precision in gear tooth cutting. The process utilizes a specialized hob with precise cutting edges, resulting in gear teeth with excellent dimensional accuracy and proper tooth profiles. This level of precision ensures smooth gear meshing and optimal performance in gear-driven systems.
- Efficiency and Productivity: Gear hobbing is a highly efficient production method, especially for large production volumes. The process enables the simultaneous cutting of multiple gear teeth, leading to rapid gear production rates. With the use of modern gear hobbing machines and advanced automation, the process can be further optimized for enhanced productivity.
- Versatility: Gear hobbing is a versatile process capable of producing a wide range of gear types and sizes. It can generate various gear configurations, such as spur gears, helical gears, worm gears, and splines. This versatility makes gear hobbing suitable for diverse applications across industries, including automotive, aerospace, and industrial machinery.
- Cost-effectiveness: In high-volume gear production, gear hobbing proves to be cost-effective. Once the initial setup is complete, gear hobbing machines can continuously produce gears with minimal operator intervention. The efficient use of cutting tools and the ability to cut multiple gear teeth in one pass contribute to overall cost savings.
- Strength and Durability: Gears produced through hobbing exhibit high strength and durability. The accurate tooth profiles and proper tooth engagement achieved in gear hobbing ensure load distribution and minimize wear. The resulting gears can withstand heavy loads and prolonged use, making them reliable components in demanding applications.
- Scalability: Gear hobbing is easily scalable for different production requirements. Whether it’s small gears for precision instruments or large gears for industrial machinery, the gear hobbing process can be adjusted to accommodate a wide range of gear sizes and quantities.
- Quality Control: Gear hobbing allows for efficient quality control measures during the production process. Various inspection techniques, such as gear measurement machines and gear analyzers, can be employed to ensure the gears meet the desired specifications. This helps maintain consistent gear quality and reduces the likelihood of defects.
It’s worth noting that while gear hobbing offers numerous advantages, other gear manufacturing methods, such as gear shaping, gear milling, and gear grinding, also have their own merits and are suitable for specific gear production requirements. The choice of the most suitable method depends on factors such as gear specifications, production volume, cost considerations, and desired gear quality.
Gear hobbing is a powerful and widely used gear production method that enables the creation of high-quality gears with excellent precision, strength, and durability. Its efficiency, versatility, and cost-effectiveness make it a preferred choice for many gear manufacturing applications.