It is the basic principle and method to reduce the distortion of workpiece to make the structure and quality of workpiece balanced as far as possible and the quenching medium cooled evenly as possible.
1. Design of compensation fixture
In essence, the design of gear fixture is to achieve the balance of various parts as much as possible when cooling through additional fixture according to the structural dimension of gear. When the cross-section size of the gear is very different, the compensation method has a good effect in order to make the workpiece heating and cooling uniform to reduce the distortion.
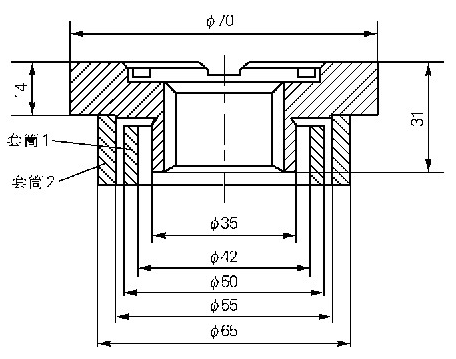
As shown in the figure, the cross-section size of the insert changes greatly, the direct quenching distortion of the insert carburizing is large, and the distortion causes the increase of the end face runout and the reduction of the spline hole. In order to reduce the distortion, sleeve l was added as the compensation pad. After carburizing and quenching, the end face runout of the insert was measured. It was found that the average runout was 0.118 mm, and the spline hole was also contracted, which could not meet the process requirements. Therefore, sleeve 2 was added outside sleeve 1. As a result, the average runout of the end face after quenching was reduced to 0.069 mm, and the distortion of spline hole (outer diameter) was also reduced by about 0.015 mm, The process requirements are met.
2. Reasonable hoisting and placement
The picture shows a kind of planetary gear with diameter of φ 601.32 mm, plate thickness of only 17.5 mm, asymmetric on both sides, which belongs to a disc-shaped part easily distorted by heat treatment. At first, after carburizing and quenching according to Fig. (a), the flatness of the end face is ≥ 1.0mm, and the maximum is 1.4mm. There is irregular distortion of lotus leaf shape, which leads to out of tolerance of the common normal line of the gear. Even if the amount of bilateral grinding reaches 0.7mm, it is often scrapped due to unqualified size after grinding. The reason for the large gear distortion can be seen from figure (a) that the cooling speed on both sides of the gear is not the same. Therefore, the mounting and hanging method is improved. According to the method shown in figure (b), a washer is added between the two gears to increase the interval, so that the cooling speed on both sides of the gear is nearly the same. After carburizing and quenching, the flatness of the end face is reduced to less than 0.4mm, and the distortion is greatly reduced.
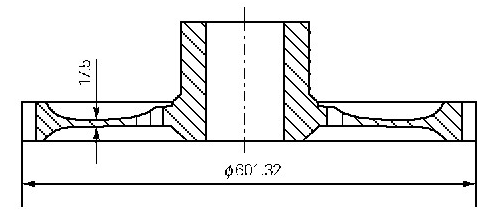
3. Improvement of lifting fixture structure
Taking the gear shaft as an example, in order to make the gear shaft stable in production, most of them are placed on the disk fixture for carburizing and quenching. In the experiment, the influence of the disk fixture structure on quenching and cooling is simulated, and the results are shown in the figure. The figure is the velocity cloud diagram of the medium flow field simulation when the shaft gear is placed on the small hole plate fixture and quenched in the oil groove, and the figure is the distribution cloud diagram of the medium flow field after the hole expansion in the middle of the fixture base. It can be seen from the figure that the through-hole of the fixture base affects the velocity distribution of the medium. By changing the size of the fixture base hole, the internal velocity of the gear shaft is accelerated, thus improving the uniformity of cooling inside and outside the gear shaft.
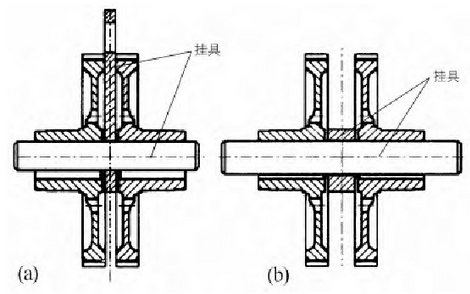
4. Improvement of cooling characteristics of quenching medium
A large number of observations and studies show that there is a great randomness in the rupture or boiling of the cooling medium vapor film, that is, it is difficult to determine the temperature range and time length of the first stage in the medium cooling curve, which will have a great impact on the cooling speed at the initial stage of quenching and the cooling uniformity of the workpiece.
In order to overcome the uncertainty of film boiling, the following measures can be taken:
1) Reasonable agitation to destroy steam film
The movement of quenching medium can destroy the stability of steam film. In some tests, 0.5 m m syringe was used to spray liquid at a speed of 0.1-5 M / s on the vapor-liquid interface 2 mm away from the sample. The results are shown in the figure. The curves 1, 2 and 3 shown in the figure are the cooling curves in the static liquid at 20 ℃, and their film boiling periods are different every time they are quenched; however, under the condition of injection speed V1 = 5 m / S (curve 4), the film boiling can be destroyed, so the cooling has reproducibility.
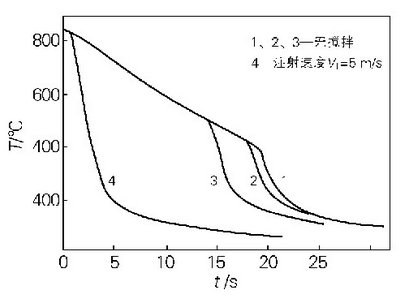
There are many ways to move the quenchant, but the effect is different. At present, it is generally considered that the better way to move the quenchant is to use propeller mixing. The biggest characteristic of propeller mixing is that it can produce a large flow and form a more uniform macro flow field in the quench tank, which meets the requirements of quench cooling.
2) Quenching with nitrate or high pressure gas
The cooling of nitrate or high-pressure gas can overcome the film boiling stage during quenching and cooling in water and oil, and directly enter the convection stage, so as to improve the cooling uniformity. The figure is a comparison of the cooling rate curve of 160 ℃ saltbath and 40 ℃ fast quenching oil. In the whole cooling process, the cooling rate of the nitrate bath is faster than that of the rapid quenching oil. According to the traditional point of view, the larger the cooling speed is, the larger the distortion of the quenched workpiece is, then the quenching distortion in the oil should be smaller, but the production shows that the distortion change in the salt bath is small. Table 9 shows the distortion of common normal line, internal spline 1, internal spline 2 and tooth top circle size after gear Carburization in nitrate bath and oil quenching. It can be seen from the table that except for the change of common normal line of nitrate quenching slightly greater than that of oil quenching, the change of internal spline and its range, the change of tooth top circle and its range of change are all better than that of oil quenching. The reason is that the characteristic temperature of the nitrate salt bath is higher than the liquid temperature of the workpiece, thus realizing the cooling in a single cooling stage (convection).

On the other hand, the ISOTHERMAL MARTENSITE can be tempered when it transforms under slow cooling condition, and the volume of tempered martensite is smaller than that of square martensite, so the distortion is reduced.
In recent years, high-pressure gas quenching is gradually rising. The figure is a comparison of out of round distortion, warping distortion and taper distortion caused by gas quenching and oil quenching of gears under given process conditions. For the standard gear, the warpage distortion and taper distortion are obviously reduced after air quenching, which are – 38% and – 34% respectively, and the dispersion is improved.
High pressure gas quenching reduces distortion, on the one hand, because of low cooling rate, low thermal stress and tissue stress, on the other hand, because there is no steam film boiling, so the cooling is relatively uniform.