Gear metallurgy and heat treatment play crucial roles in ensuring reliable gear performance. Let’s explore how they contribute to the durability and efficiency of gears.
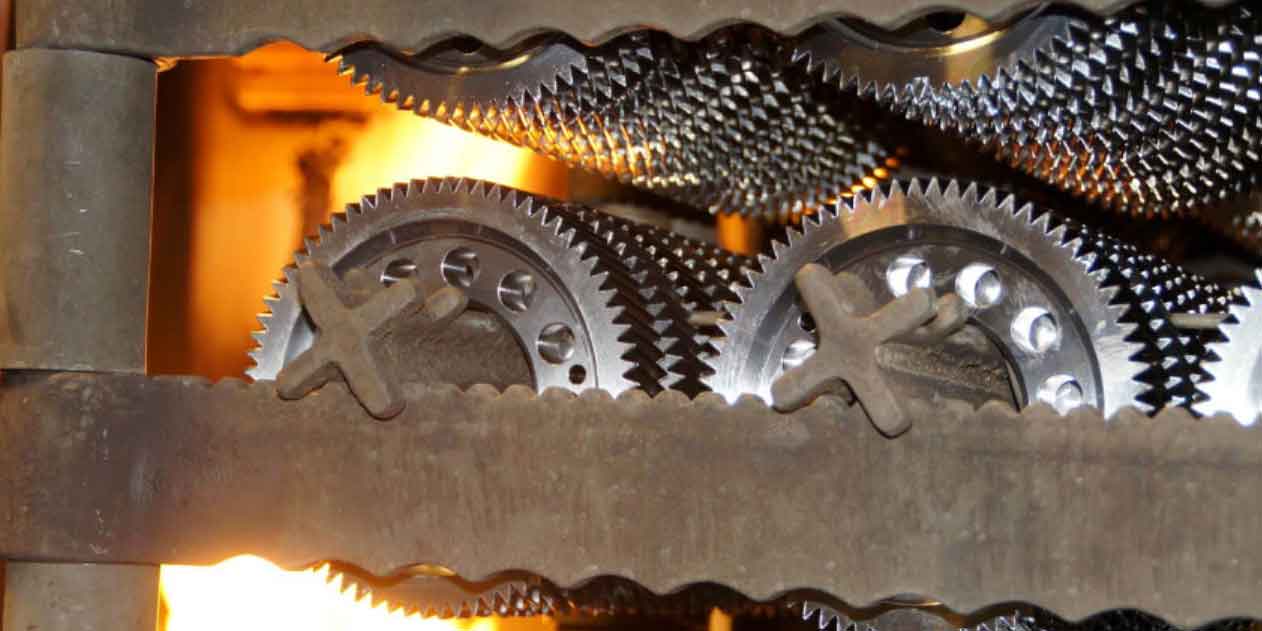
- Gear Metallurgy:
- The selection of appropriate materials is vital for gears to withstand the demanding operating conditions and loads they encounter. Here are some key considerations in gear metallurgy:a. Material Strength: Gears are typically made from steel alloys due to their high strength, fatigue resistance, and toughness. Common choices include alloy steels, carburizing steels, and nitriding steels, depending on the specific application requirements.b. Alloying Elements: Various alloying elements like chromium, molybdenum, and nickel are added to enhance the material properties. For instance, chromium improves wear resistance, while molybdenum increases strength and hardenability.c. Case Hardening Steels: Gears often employ case hardening, where a hard and wear-resistant outer layer is developed on a tough and resilient core material. This process improves both the surface hardness and the core strength of the gears.
- Heat Treatment:
- Heat treatment is a critical step in the manufacturing process of gears. It involves controlled heating and cooling of the gear material to achieve specific properties. The primary heat treatment processes for gears include the following:
- a. Carburizing: Carburizing involves introducing carbon into the surface layer of the gear material. This process creates a high-carbon, wear-resistant surface while maintaining a relatively low-carbon, tough core. Carburized gears exhibit excellent wear resistance and fatigue strength.
- b. Quenching and Tempering: Quenching rapidly cools the carburized gear to harden it, followed by tempering to reduce brittleness and enhance toughness. This combination of processes optimizes the balance between hardness and toughness, resulting in a strong and durable gear.
- c. Nitriding: Nitriding is another heat treatment technique where nitrogen is diffused into the gear’s surface. This process forms a hard nitride layer, providing excellent wear resistance and fatigue strength, particularly in high-speed and high-load applications.
- d. Induction Hardening: Induction hardening selectively heats specific areas of the gear using high-frequency induction coils. This process rapidly quenches the heated regions, resulting in a hardened surface. Induction hardening is commonly used for gears with complex shapes or large diameters.
- Heat treatment is a critical step in the manufacturing process of gears. It involves controlled heating and cooling of the gear material to achieve specific properties. The primary heat treatment processes for gears include the following:
Proper gear metallurgy and heat treatment ensure that gears can withstand the demanding conditions they are subjected to, such as high loads, shock, and repetitive stress. By selecting the right materials and applying appropriate heat treatment processes, manufacturers can significantly improve gear performance, reliability, and longevity.