Gear shaping, as a fundamental process in gear manufacturing, has seen several innovations and advancements that have significantly improved the efficiency, accuracy, and flexibility of gear production. Some notable innovations in gear shaping include:
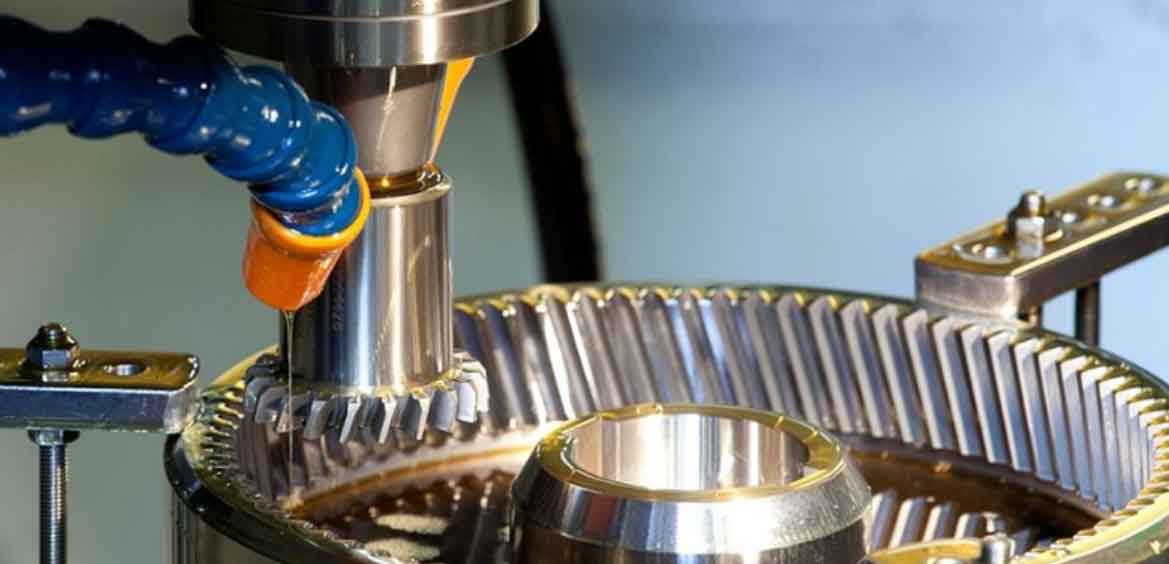
- High-Speed Gear Shaping Machines: Modern gear shaping machines have witnessed advancements in their design and construction, allowing for higher cutting speeds. High-speed gear shaping machines enable faster gear production, reducing cycle times and increasing productivity.
- Advanced Control Systems: Gear shaping machines now feature advanced control systems that provide precise control over the shaping process. These systems allow for the adjustment and optimization of cutting parameters, ensuring consistent and accurate gear tooth formation.
- CNC Gear Shaping Machines: Computer Numerical Control (CNC) technology has been integrated into gear shaping machines, offering greater flexibility and automation. CNC gear shaping machines allow for complex gear profiles and the use of various cutting strategies, making them suitable for the production of customized gears.
- Tooling Innovations: Shaper cutters, the primary tool used in gear shaping, have witnessed innovations to improve their performance. Carbide inserts and coatings are now commonly used, offering longer tool life, increased cutting speeds, and improved productivity. Additionally, advancements in tool design and manufacturing techniques have resulted in more precise and efficient shaping of gear teeth.
- Simulation and Virtual Modeling: Computer-aided simulation and virtual modeling techniques have revolutionized gear shaping. Manufacturers can now simulate the gear shaping process virtually, optimizing tool paths, reducing setup time, and minimizing errors before the actual production begins. This technology enables improved efficiency, accuracy, and reduces material waste.
- Automation and Robotics: The integration of automation and robotics into gear shaping processes has led to increased productivity and reduced human intervention. Robotic systems are utilized for loading and unloading gear blanks, tool changing, and in-process inspection, enabling continuous and uninterrupted production.
- In-Process Quality Monitoring: Gear shaping machines now incorporate advanced sensing and measurement systems for in-process quality monitoring. These systems monitor the cutting forces, vibrations, and gear tooth profiles in real-time, ensuring that any deviations or anomalies are detected promptly, leading to improved gear quality and reducing the risk of producing defective gears.
- Software Solutions: Gear shaping is supported by specialized software tools that assist in gear design, simulation, and optimization. These software solutions enable the efficient generation of gear tooth profiles, simulate the shaping process, and optimize cutting parameters for improved efficiency and performance.
These innovations in gear shaping have resulted in higher productivity, enhanced accuracy, and improved flexibility in gear manufacturing. Gear manufacturers can leverage these advancements to meet the increasing demands of various industries, including automotive, aerospace, and industrial machinery, where precise and reliable gears are essential for efficient operations.
Pages: 1 2