Gear shaping is a versatile process that unlocks the potential for customized gear manufacturing. Here’s how gear shaping enables the production of customized gears:
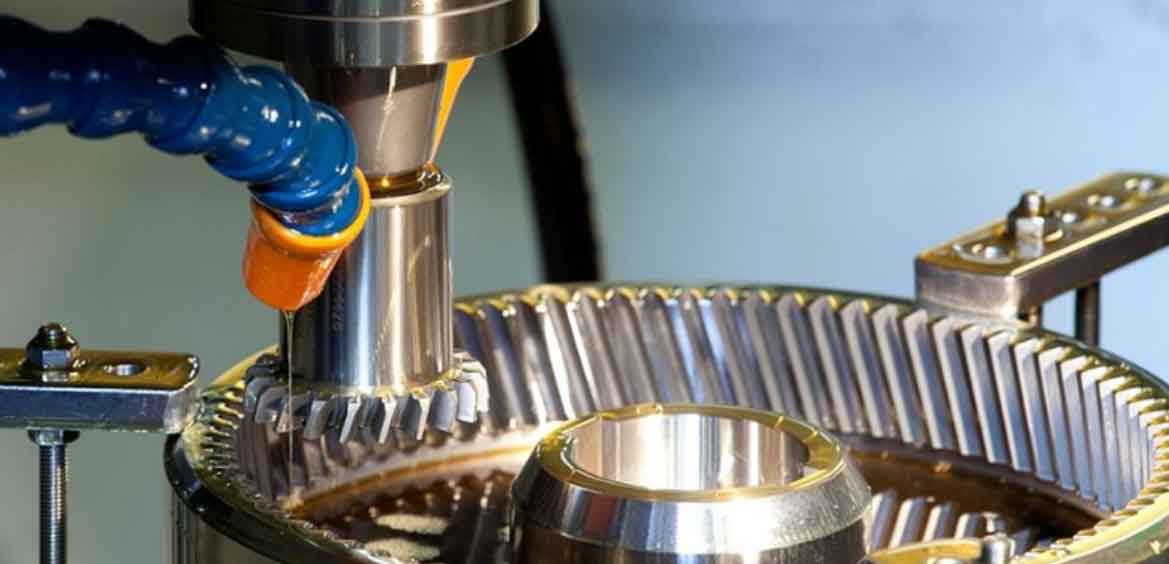
- Flexible Gear Geometries: Gear shaping can accommodate a wide range of gear geometries, including spur gears, helical gears, internal gears, and more. This versatility allows manufacturers to create gears with customized tooth profiles, pressure angles, addendums, and dedendums. Custom gear geometries can be tailored to specific applications, optimizing gear performance and ensuring compatibility with mating components.
- Gear Size Customization: Gear shaping machines are available in various sizes and configurations, allowing for the production of gears in different dimensions. Whether it’s small precision gears or large industrial gears, gear shaping can be adapted to manufacture customized gears of various sizes to meet specific application requirements.
- Complex Gear Profiles: Gear shaping is capable of generating complex gear profiles with high precision. This includes gears with modified profiles, asymmetric tooth shapes, or custom tooth modifications such as tip relief, root relief, or profile shifts. These customization options enable gears to be tailored to unique operational demands, such as reducing noise, optimizing load distribution, or improving meshing characteristics.
- Specialized Applications: Customized gear shaping is often employed in specialized applications where standard off-the-shelf gears may not suffice. Industries such as aerospace, defense, robotics, and medical equipment often require gears with specific performance characteristics and design requirements. Gear shaping allows for the creation of gears that are customized to meet the unique demands of these applications.
- Prototyping and Small Production Runs: Gear shaping is well-suited for prototyping and small production runs. It offers the flexibility to quickly produce customized gears for testing, evaluation, and validation purposes. With shorter setup times and the ability to produce small quantities economically, gear shaping enables manufacturers to iterate and refine gear designs before committing to full-scale production.
- Material Selection: Customized gear shaping allows for the selection of specific materials that best suit the application requirements. Various factors such as strength, wear resistance, and compatibility with environmental conditions can be considered when choosing the gear material. Customization extends to the material selection process, ensuring that the gears are optimized for performance and longevity.
- Application-Specific Modifications: Gear shaping can incorporate application-specific modifications to enhance gear performance. This includes features such as keyways, splines, holes, or customized mounting interfaces. These modifications facilitate seamless integration of gears into the overall system design, ensuring efficient power transmission and precise functionality.
- Efficiency Optimization: Customized gear shaping enables manufacturers to optimize gear efficiency by tailoring the gear tooth profile and surface finish. By analyzing the specific operating conditions and load requirements, gears can be designed with reduced friction, improved meshing characteristics, and enhanced efficiency. Customized gear shaping allows for the incorporation of efficiency-enhancing features such as optimized tooth contact patterns or low-friction coatings.
Gear shaping provides the flexibility and precision required to produce customized gears that meet specific design and performance criteria. By leveraging the capabilities of gear shaping, manufacturers can deliver gears that precisely match the needs of their customers, resulting in improved gear performance, increased system efficiency, and enhanced overall product quality.