Gear shaping is a machining process that involves the precise formation of gear teeth using a gear shaping machine and a cutting tool called a shaper cutter. Let’s take a closer look at the art of accurate gear tooth formation through gear shaping:
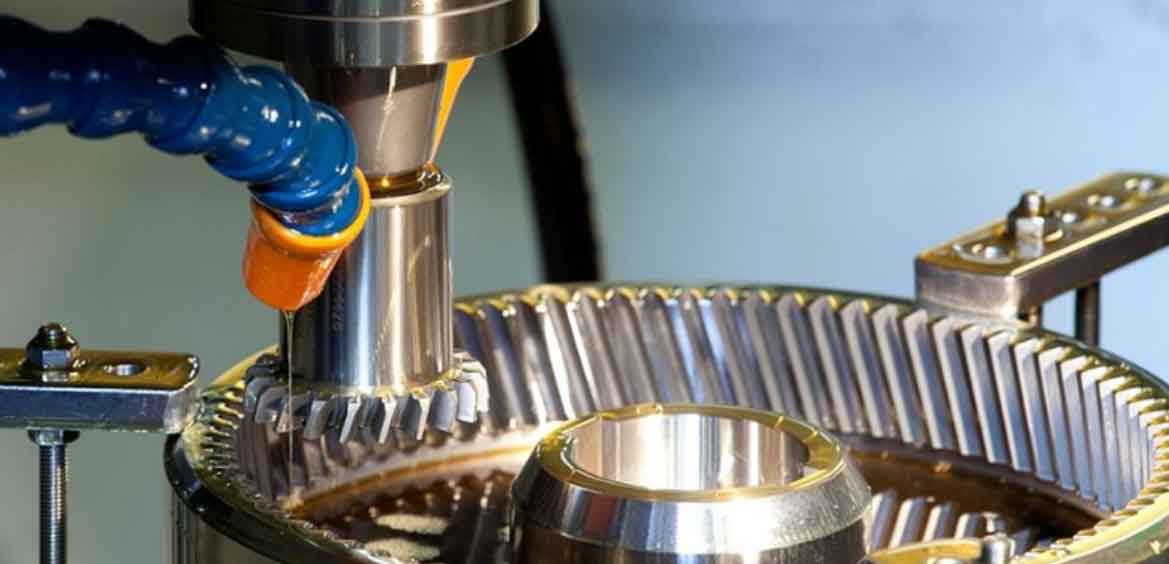
- Tooth Profile Generation: Gear shaping machines are capable of generating various tooth profiles, including spur gears, helical gears, and internal gears. The shaper cutter, with its specifically designed tooth geometry, gradually cuts into the workpiece to form the gear teeth. The reciprocating motion of the cutter and the rotation of the workpiece combine to produce the desired tooth profile.
- Cutting Principle: The gear shaping process follows a principle known as “generation cutting.” Unlike other gear manufacturing methods that rely on relative motion between the cutter and the workpiece, gear shaping generates the tooth profile by precisely controlling the cutter’s movement across the workpiece. This allows for greater control over tooth form accuracy and ensures consistent tooth spacing and alignment.
- Accuracy and Precision: Gear shaping is renowned for its ability to achieve high accuracy and precision in gear tooth formation. The reciprocating motion of the cutter allows for precise control over the cutting process, resulting in tooth profiles with tight tolerances. The accuracy of gear shaping is further enhanced by the use of advanced gear shaping machines with rigid structures and precise control systems.
- Tool Design and Selection: Shaper cutters play a crucial role in gear shaping, and their design and selection are critical for accurate tooth formation. The tooth profile of the shaper cutter must correspond to the desired gear tooth profile. Various factors, such as the gear module, pressure angle, helix angle (for helical gears), and material being cut, influence the design and selection of the shaper cutter. Proper cutter design ensures accurate tooth geometry and minimizes errors in the gear tooth profile.
- Machine Setup and Alignment: Achieving accurate gear tooth formation requires precise machine setup and alignment. The gear shaping machine components, including the cutter spindle, workpiece spindle, and ram, must be aligned correctly to ensure proper tooth spacing and alignment. Machine calibration and adjustment are essential for minimizing errors and achieving optimal gear accuracy.
- Cutting Parameters Optimization: The cutting parameters, such as cutting speed, feed rate, and depth of cut, need to be optimized for accurate gear tooth formation. These parameters depend on various factors, including the gear material, cutter design, and desired surface finish. Optimizing the cutting parameters helps maintain dimensional accuracy, minimize tool wear, and ensure consistent gear quality.
- Post-Processing and Quality Control: After gear shaping, post-processing steps such as deburring, cleaning, and heat treatment may be necessary to achieve the desired gear quality. Quality control measures, such as dimensional inspections and tooth profile analysis, are conducted to ensure that the gears meet the required specifications and tolerances.
Accurate gear tooth formation through gear shaping requires a combination of skilled operators, precise machine setup, proper tool design, and optimization of cutting parameters. The art lies in achieving the desired tooth profile with tight tolerances and ensuring consistent gear quality. By mastering the art of accurate gear tooth formation, manufacturers can produce gears that meet the highest standards of performance, durability, and reliability in various industrial applications.