In recent years, many scholars have done a lot of research on gear modification, and there are many modification methods of gear tooth direction. Referring to a large number of relevant materials, there are three common methods with good modification effect: tooth end modification, drum modification and spiral angle modification.
① Tooth end modification
Tooth end modification is to gradually thin the tooth thickness to the end of one or both ends of the gear tooth in a small tooth width at the same time. This method is suitable for transmission speed V < 100M / s and small thermal deformation. The modification amount is calculated and determined according to the elastic deformation. For straight teeth and single oblique teeth, 0.013 mm ≤ Δ ≤ 0.035 mm。 The maximum contact deformation generally occurs at the place where the distance from both ends is 7% to 8% of the contact length, where the contact stress is the largest and the edge effect is the most prominent. In order to avoid the stress concentration caused by the edge effect, the modification length l should be greater than the above value, and generally L = 0.1b can be taken. Tooth end modification is the simplest of the three modification methods, and the meshing contact width along the tooth direction is larger than that of drum modification, and its bearing capacity is higher than that of drum modified gear. Because the tooth end modification only modifies the part near the end face, when the tooth width of the meshing gear is large, if the meshing gear has a slight inclination, it will cause serious load concentration. Therefore, the effect of tooth end modification is poor, which is only suitable for single piece and small batch production. The effect and size of tooth end modification are shown in Figure 1 below.
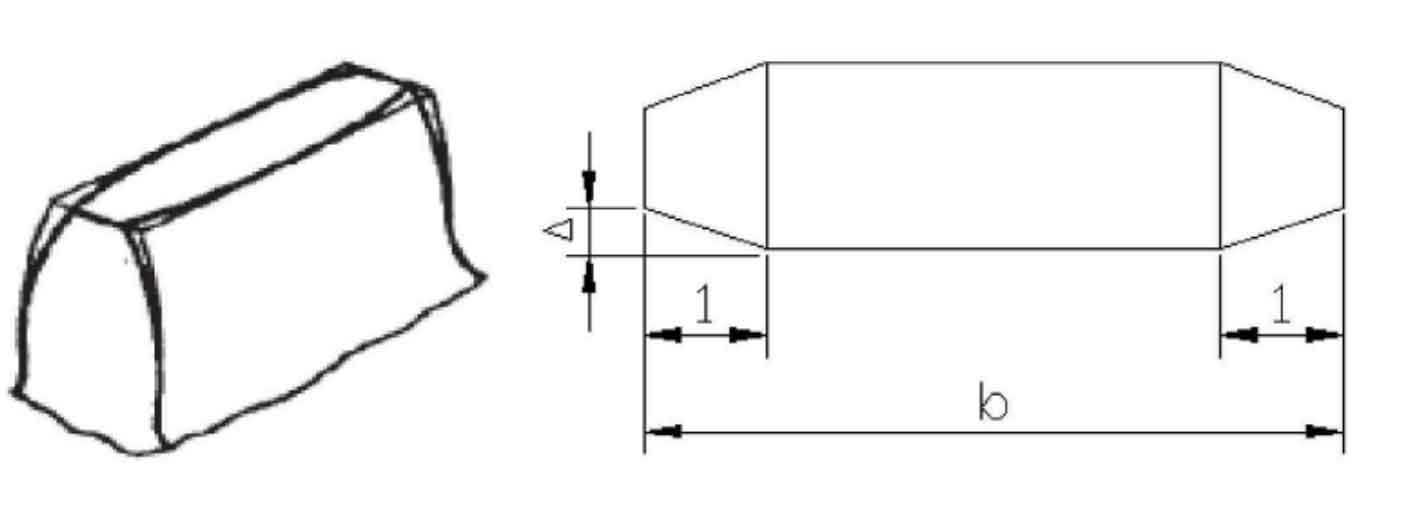
② Drum modification
Drum shape modification is a modification method to make the gear teeth bulge in the middle of the tooth width and arranged symmetrically on both sides. As shown in Figure 2, this method is applicable to the case of V < 100M / s and small thermal deformation. The modification amount is calculated and determined according to the elastic deformation, generally 0.013 mm ≤ Δ ≤ 0.035 mm。 The design method of this modification method is relatively simple, the processing is also relatively convenient, and it is easy to control the quality of modification and find problems, so it has a wide range of applications.
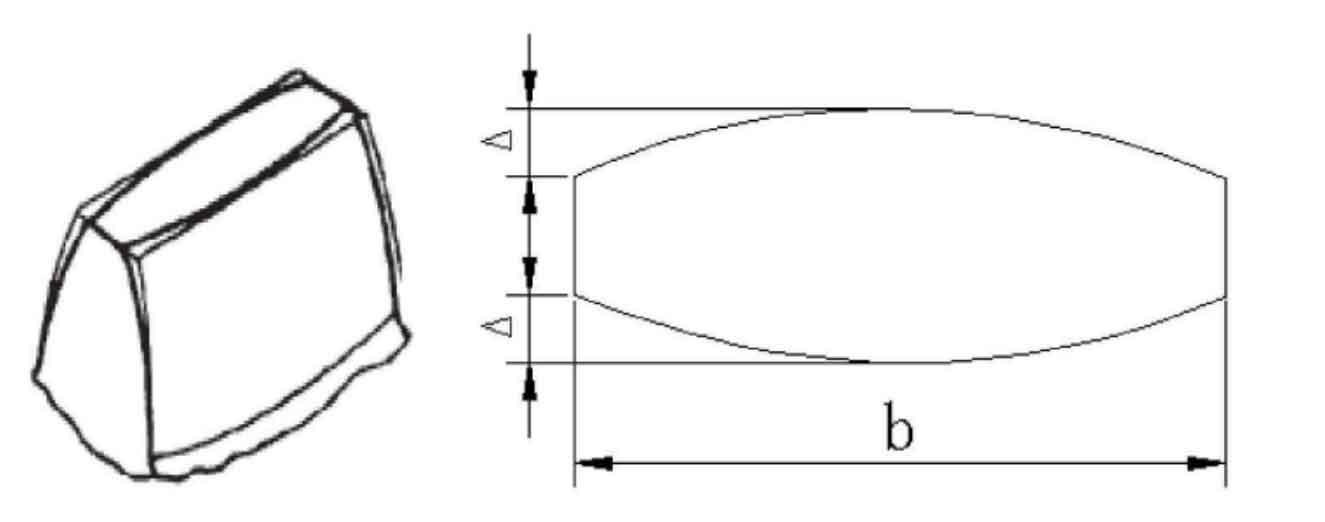
③ Spiral angle modification
As shown in Fig. 3, when the helical gear is processed with small angle, the difference between the two helical gears is caused by various helical angle correction factors, as shown in Fig. 3. The overall effect of helical angle modification is better than that of tooth end modification. However, because the angle of helical angle modification is very small, and there can be no obvious modification effect everywhere in the tooth direction, and the angle to be changed is small, it is not easy to control the processing volume and is not conducive to processing.
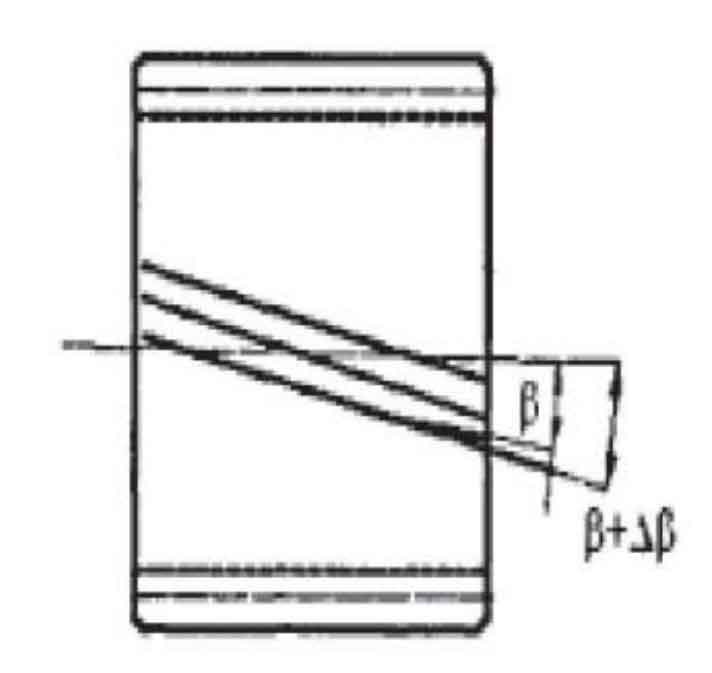
Due to the influence of many factors such as the bending deformation of the gear shaft, the tooth end modification method can not achieve a good modification effect; The angle to be changed by spiral angle modification is very small, which is not conducive to machining; Drum shape modification can compensate the manufacturing error of gear and various elastic deformation caused by gear under load, mainly the bending and torsional deformation of pinion shaft under stable load. After analysis and comparison, the drum shape modification method of helical gear is selected to modify the second shaft and fourth gear of the gear model supported at both ends.