Hypoid gears offer several advantages over other types of gears, such as spur gears or bevel gears, when it comes to enhancing efficiency and durability in gear systems. Let’s explore some of the key features that contribute to their superior performance:
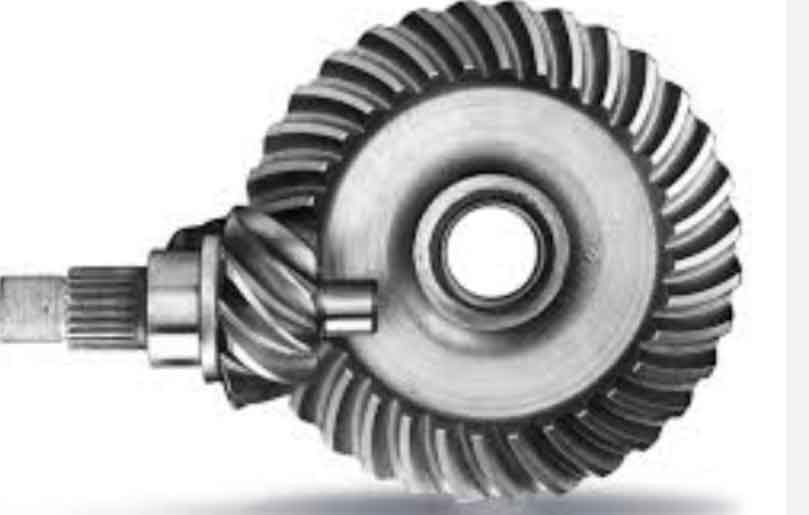
1.Higher Torque Capacity:
Hypoid gears are designed to handle higher torque levels compared to other gear types. The line contact between the gear teeth allows for a larger contact area, distributing the load more effectively. This feature enables hypoid gears to transmit higher levels of power without compromising their integrity.
2.Offset Design for Compactness:
The offset configuration of hypoid gears allows the transmission of motion between non-parallel and non-intersecting shafts. This design feature enables the creation of more compact gear systems, making them particularly advantageous in applications where space is limited. The compactness also helps reduce the overall weight of the system.
3.Improved Efficiency:
Hypoid gears exhibit higher mechanical efficiency compared to other gear types, such as worm gears. The sliding motion between the gear teeth minimizes friction losses, resulting in improved power transmission efficiency. Additionally, the gear geometry and tooth contact pattern contribute to reduced noise and vibration levels, further enhancing overall system efficiency.
4.Versatile Applications:
Hypoid gears find applications in various industries, especially in automotive systems. They are commonly used in differential gear assemblies, where they efficiently distribute torque to the wheels while allowing for different rotational speeds during turns. The durability and high torque capacity of hypoid gears make them suitable for heavy-duty applications such as trucks, construction equipment, and industrial machinery.
5.Lubrication and Cooling:
The sliding motion between the gear teeth in hypoid gears generates more heat compared to other gear types. Therefore, proper lubrication and cooling are crucial for maintaining the efficiency and durability of the gear system. Careful consideration of lubricant properties, adequate cooling mechanisms, and effective sealing are important factors in optimizing the performance of hypoid gears.
6.Manufacturing and Maintenance:
Hypoid gears require precision manufacturing techniques to ensure accurate tooth geometry and optimal contact patterns. Modern manufacturing methods, such as CNC machining and advanced gear cutting processes, allow for high-quality hypoid gear production. Additionally, routine maintenance practices, including lubrication checks and gear inspections, are essential for prolonging the lifespan and ensuring reliable operation of hypoid gears.
Hypoid gears offer enhanced efficiency and durability in gear systems. Their higher torque capacity, compact design, improved efficiency, and versatile applications make them suitable for various industries, particularly in automotive systems. By considering factors such as lubrication, cooling, precise manufacturing, and regular maintenance, the performance and longevity of hypoid gears can be further optimized.