The strengthening technology of gear heat treatment should pay attention to the control of surface integrity, that is, to control the structure, depth, hardness and residual stress of the hardened layer. Improper control of heat treatment of gears can easily lead to excessive grain boundary oxide layer structure, decarburization, micro cracks and other defects.
1. Nitrocarburizing
Compared with carburizing, the treatment temperature of nitrocarburizing (soft nitriding) is low, generally at 460 ~ 600 ℃, so the gear deformation is small. Nitriding can improve the surface hardness, wear resistance, fatigue strength and corrosion resistance of gears. Japanese automobile companies do not have high requirements for the fatigue life limit of some automotive gears. After heat treatment, they do not do the finishing of the gear surface. When heat treatment, they use nitrocarburizing process, usually to improve the wear resistance of the gear surface as the main purpose.
2. Surface hardening
Surface hardening mainly includes induction hardening and laser hardening. Compared with carburizing quenching, the surface quenching deformation is smaller. Induction hardening is mainly used for surface hardening of automobile gears [13]. According to the different module of gear, different induction quenching methods are adopted. For example, if the module of gear is 3-5mm, high frequency induction quenching is adopted; when the module is increased to 5-8mm, medium frequency induction quenching is generally selected. The hardening layer can be obtained by high frequency heating and quenching, and the fatigue strength of automobile steering pinion can be greatly improved by using high frequency quenching heat treatment. High frequency heat treatment has the outstanding advantages of low CO2 emission, high fatigue strength and wear resistance of gears, and small distortion [14]. Laser quenching has the advantages of fine and uniform grains in the quenching area and small gear deformation, which provides an effective way to strengthen the gear surface with large modulus and high precision, but its cost is high.
3. Carburizing
Carburizing is one of the chemical heat treatment methods widely used in automobile gear surface treatment. The carburizing treatment can make the gear have good comprehensive mechanical properties and effectively prevent the gear teeth from breaking.
At present, carburizing methods include gas carburizing, vacuum carburizing and plasma carburizing. Gas carburizing is a widely used surface strengthening process for low carbon alloy steel gears, which can make the surface of gears obtain higher hardness and improve their wear resistance, while the core is still the original lath like martensite structure to maintain good toughness.
High temperature carburizing can increase the carburizing temperature of gears from 900 ℃ to 1050 ℃, shorten the carburizing time by more than 50%, and improve the production efficiency effectively. However, high temperature carburizing is easy to cause austenite grain coarsening, reduce gear fatigue performance, and large deformation. In order to overcome the problem of grain growth during high temperature carburizing, domestic and foreign scholars have found that microalloying is an effective way to inhibit the austenite grain growth of gear steel. The research in Japan shows that the best carburizing depth and minimum deformation can be obtained by controlling the carburizing depth and surface hardness during heat treatment. By adjusting and adding Nb, Ti, B and other alloy elements, the austenite grain coarsening produced by high temperature carburizing is effectively controlled, and the above problems are well solved. Vacuum carburizing and plasma carburizing have the advantages of no grain boundary oxidation, high surface mechanical properties, less CO2 emission, short heat treatment time and energy consumption, but high cost.
4. Carbonitriding
The strength and wear resistance of gears can be improved by controlling the nitrogen concentration and the time node of nitrogen addition. The carbon nitrogen heat treatment method is conducive to the adjustment of the content of retained austenite to inhibit the development of initial fatigue cracks to the depth. The thickness of the abnormal carburizing layer of the traditional carburized and quenched steel (20CrMoH) is about 15 ~ 20 μ m, and the thickness of the abnormal carburizing layer treated by carbonitriding is only 1 / 2 of it.
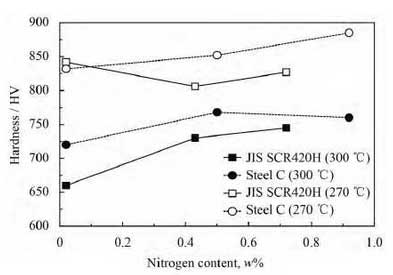
Carbonitriding can effectively improve the depth of carburizing layer, refine austenite grains, reduce gear deformation, improve gear strength and wear resistance. The actual instantaneous working temperature of carburized gears in automotive automatic transmission is about 250 ~ 270 ℃, which is 150 ~ 200 ℃ higher than the common tempering temperature range. Higher meshing temperature will lead to the decrease of tooth surface hardness and easy to produce fatigue pitting. Through adjusting the amount of nitriding, the tempering resistance is improved, and the tempering temperature is about 300 ℃. As shown in the figure, the effect of nitrogen content on the hardness of scr420h steel and Steel C at 170 ℃ and 300 ℃ was studied by carbonitriding process.