Heat treatment is a crucial process in the manufacturing of straight bevel gear, significantly impacting their durability, strength, and performance. By altering the microstructure of straight bevel gear material, heat treatment can enhance properties such as hardness, toughness, and wear resistance, leading to longer service life and improved reliability. This article explores various heat treatment processes used to enhance the durability of straight bevel gear, discussing their mechanisms, benefits, and practical applications.
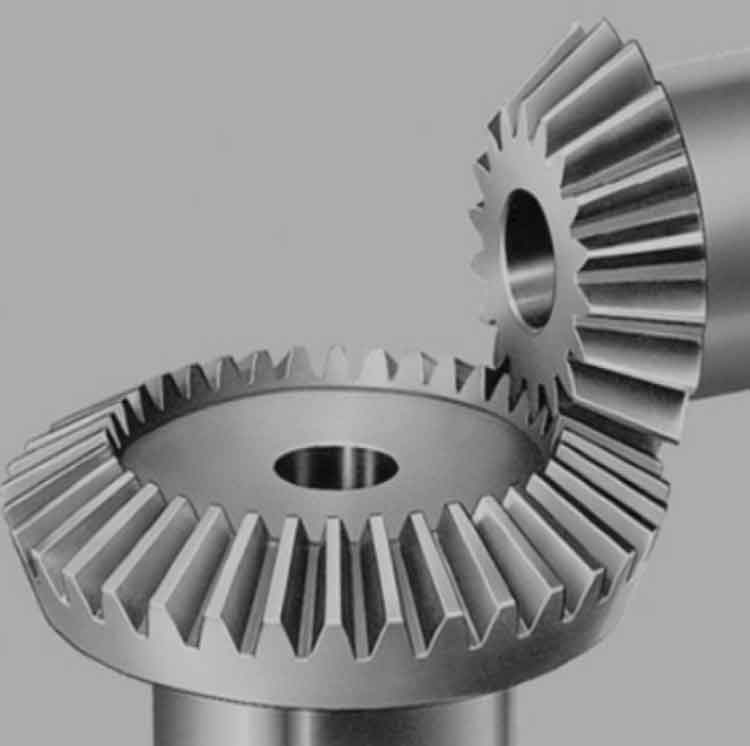
Introduction
Straight bevel gear is widely used in applications that require the transmission of power between intersecting shafts, such as in automotive differentials, industrial machinery, and aerospace systems. The durability of these gears is critical to their performance and longevity. Heat treatment processes play a vital role in improving the mechanical properties of straight bevel gear materials, making them more resistant to wear, fatigue, and other forms of failure.
Key Heat Treatment Processes
Several heat treatment processes are commonly used to enhance the durability of straight bevel gear. These include carburizing, nitriding, induction hardening, and austempering. Each process offers unique benefits and is selected based on the specific requirements of straight bevel gear application.
Table 1: Common Heat Treatment Processes for Straight Bevel Gear
Process | Description | Benefits | Applications |
---|---|---|---|
Carburizing | Adding carbon to the surface of low-carbon steel | Increased surface hardness | Automotive, heavy machinery |
Nitriding | Adding nitrogen to the surface for case hardening | Enhanced wear and fatigue resistance | Aerospace, precision gears |
Induction Hardening | Heating the gear surface using electromagnetic induction | Improved surface hardness and toughness | Industrial machinery, automotive |
Austempering | Quenching and tempering in a bath to achieve bainitic structure | Increased toughness and wear resistance | High-performance gears |
Carburizing
Carburizing is a process that involves adding carbon to the surface layer of low-carbon steel gears. This is achieved by exposing straight bevel gear to a carbon-rich environment at high temperatures. The carbon diffuses into the surface, creating a hard, wear-resistant outer layer while maintaining a tough and ductile core.
- Process Steps:
- Heating straight bevel gear in a carbonaceous atmosphere (e.g., natural gas or propane) at 900-950°C.
- Quenching straight bevel gear rapidly to lock in the carbon-rich surface structure.
- Tempering to reduce internal stresses and achieve the desired hardness.
- Benefits:
- Increased surface hardness and wear resistance.
- Enhanced fatigue strength due to the tough core.
List of Carburizing Benefits
- Increased surface hardness
- Enhanced wear resistance
- Improved fatigue strength
Nitriding
Nitriding involves introducing nitrogen into the surface of straight bevel gear material. This process is conducted at lower temperatures compared to carburizing, typically between 500-550°C, and results in the formation of a hard, wear-resistant nitrided layer.
- Process Steps:
- Heating straight bevel gear in an ammonia-rich atmosphere.
- Allowing nitrogen to diffuse into the surface to form nitrides.
- Cooling slowly to maintain the nitrided layer’s integrity.
- Benefits:
- Superior wear and fatigue resistance.
- Minimal distortion due to the lower processing temperatures.
List of Nitriding Benefits
- Superior wear resistance
- Enhanced fatigue resistance
- Minimal distortion
Induction Hardening
Induction hardening uses electromagnetic induction to heat the surface of straight bevel gear rapidly. The gear is then quenched immediately, resulting in a hard, tough surface layer while the core remains unaffected.
- Process Steps:
- Inducing an electromagnetic field to heat straight bevel gear surface.
- Quenching the heated surface quickly to harden it.
- Tempering to achieve the desired hardness and reduce internal stresses.
- Benefits:
- Improved surface hardness and toughness.
- Precise control over the hardened layer’s depth and properties.
List of Induction Hardening Benefits
- Improved surface hardness
- Enhanced toughness
- Precise control over hardening depth
Austempering
Austempering is a heat treatment process that involves quenching straight bevel gear in a molten salt bath or oil at a temperature above the martensite start temperature but below the pearlite formation temperature. This results in the formation of a bainitic microstructure, which provides excellent toughness and wear resistance.
- Process Steps:
- Heating straight bevel gear to the austenitizing temperature (800-900°C).
- Quenching in a salt bath or oil at 250-400°C.
- Holding until the bainitic structure is fully formed.
- Cooling to room temperature.
- Benefits:
- Increased toughness and wear resistance.
- Reduced risk of distortion compared to traditional quenching methods.
List of Austempering Benefits
- Increased toughness
- Enhanced wear resistance
- Reduced risk of distortion
Practical Applications and Case Studies
Heat treatment processes are selected based on the specific requirements of the application. For instance, carburizing is commonly used in automotive and heavy machinery applications where high surface hardness is critical. Nitriding is preferred in aerospace and precision gear applications due to its superior wear and fatigue resistance with minimal distortion. Induction hardening is widely used in industrial machinery and automotive components for its ability to precisely control the hardened layer. Austempering is chosen for high-performance gears that require a balance of toughness and wear resistance.
Table 2: Heat Treatment Applications and Benefits
Application | Preferred Process | Key Benefits |
---|---|---|
Automotive | Carburizing | High surface hardness, wear resistance |
Aerospace | Nitriding | Superior wear and fatigue resistance |
Industrial Machinery | Induction Hardening | Controlled hardness, toughness |
High-Performance Gears | Austempering | Toughness, wear resistance |
Conclusion
Heat treatment processes play a pivotal role in enhancing the durability and performance of straight bevel gear. By carefully selecting and applying processes such as carburizing, nitriding, induction hardening, and austempering, manufacturers can significantly improve the mechanical properties of gears, leading to longer service life and reliable operation. As advancements in heat treatment technologies continue, the capabilities and applications of these processes will expand, offering even greater benefits to straight bevel gear manufacturing industry.