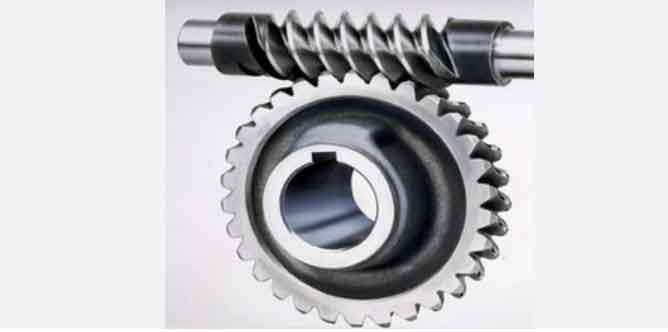
Helical gear manufacturing requires precision engineering to produce high-quality gears that meet the demanding requirements of various applications. The process involves several key steps to ensure the gears’ accuracy, durability, and performance. Here are the essential aspects of precision engineering in helical gear manufacturing:
1. Design and Engineering:
The manufacturing process begins with meticulous gear design and engineering. Engineers use specialized software and tools to determine the gear specifications, including the helix angle, tooth profile, number of teeth, and other critical dimensions. Precise design ensures that the gears will mesh smoothly and transmit power efficiently.
2. Material Selection:
Selecting the appropriate gear material is vital to achieve the desired gear performance. High-quality materials with the necessary strength, wear resistance, and fatigue properties are essential for long-lasting and high-performance gears. Common materials include alloy steels, carbon steels, and specialty materials for specific applications.
3. Gear Cutting Techniques:
Several gear cutting techniques can be used to manufacture helical gears, including hobbing, shaping, and milling. Hobbing is the most common method, involving the use of a hob tool to generate the gear teeth progressively. Precise control of the cutting process and tool geometry is crucial to achieving accurate gear tooth profiles.
4. Heat Treatment:
Heat treatment is a critical step in the manufacturing process to enhance the gear material’s properties. Processes like carburizing, quenching, and tempering are employed to achieve the desired hardness and improve wear resistance. Proper heat treatment ensures that the gears can withstand the loads and stresses encountered in operation.
5. Gear Grinding and Finishing:
After the initial gear cutting, gear grinding and finishing processes are often used to achieve tight tolerances and improve gear accuracy. Gear grinding ensures precise tooth profiles and surface finish, reducing noise and increasing gear efficiency.
6. Quality Control and Inspection:
Throughout the manufacturing process, strict quality control and inspection measures are implemented to verify the gear’s dimensions, tooth geometry, and surface finish. Advanced inspection tools, such as coordinate measuring machines (CMMs), ensure that the gears meet the required specifications.
7. Assembly and Testing:
If the helical gears are part of a gear system, their assembly with other components must be precise to ensure proper gear meshing. After assembly, gear systems are subjected to rigorous testing to verify their performance under various load conditions.
8. Continuous Improvement:
Precision engineering involves continuous improvement efforts to optimize gear manufacturing processes, reduce variability, and enhance gear quality. Feedback from testing and real-world performance is used to refine future gear designs and manufacturing techniques.
By integrating these precision engineering principles into the manufacturing process, companies can produce high-quality helical gears that deliver reliable and efficient performance in various industries, such as automotive, aerospace, industrial machinery, and more. Precision-engineered helical gears are essential for smooth operation, minimized noise, extended service life, and overall gear system reliability.