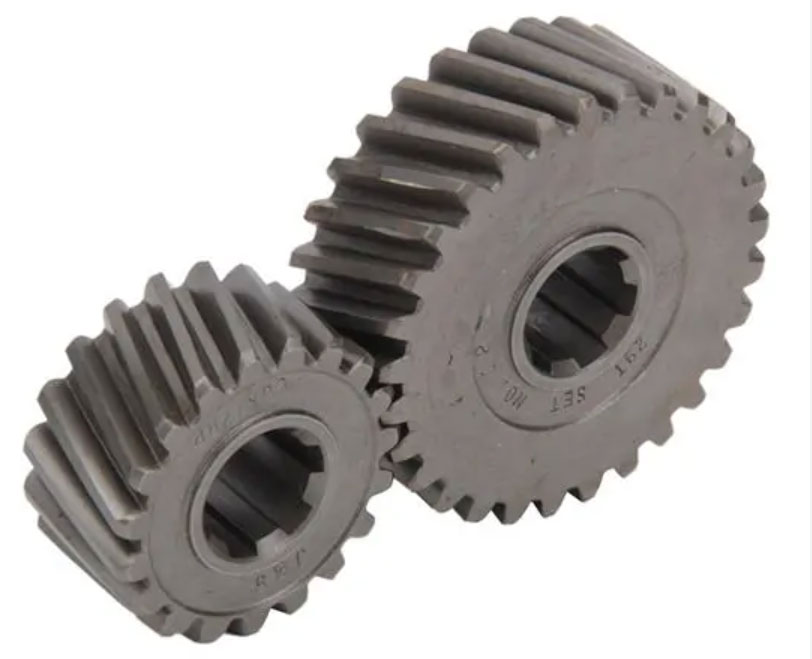
Helical gear manufacturing involves several techniques to ensure precise gear geometry, high-quality materials, and reliable performance. Additionally, robust quality assurance measures are essential to verify gear accuracy and performance. Here are some key manufacturing techniques and quality assurance practices used in helical gear production:
1. Gear Cutting Techniques:
- Hobbing: Hobbing is one of the most common methods for manufacturing helical gears. It involves using a hob, a cutting tool with helical grooves, to produce the gear teeth by removing material from the workpiece. This process is efficient and well-suited for high-volume production.
- Shaping: Gear shaping is another method for producing helical gears. It uses a reciprocating cutting tool (shaper cutter) to create the gear teeth. Shaping is suitable for small batch production and allows for more precise tooth profiles.
- Gear Grinding: Gear grinding is used to achieve high precision and surface finish in the final gear. After hobbing or shaping, grinding removes any remaining irregularities and ensures accurate tooth profiles and meshing.
2. Gear Material Selection:
- High-quality gear materials are crucial for gear performance and longevity. Common gear materials include alloy steels, stainless steels, and specialized materials for specific applications. Proper material selection is based on factors like load capacity, wear resistance, and heat treatment compatibility.
3. Heat Treatment:
- Heat treatment is an essential step to achieve the desired material properties in gears. Processes like carburizing, quenching, and tempering are used to improve hardness, strength, and wear resistance. Proper heat treatment ensures the gears can handle the required loads and stresses.
4. Tooth Profile Measurement:
- Precise measurement of the gear tooth profile is critical to ensure accurate gear meshing and smooth operation. Various methods, such as coordinate measuring machines (CMMs) and gear measuring instruments, are used for tooth profile measurement.
5. Gear Inspection:
- Inspection throughout the manufacturing process helps identify any defects or deviations from design specifications. Inspections can include visual inspections, dimensional checks, and non-destructive testing (NDT) methods like ultrasonic or magnetic particle inspection.
6. Gear Assembly and Runout Check:
- During gear assembly, proper alignment and center distance control are essential to ensure smooth gear meshing. Runout checks are performed to verify concentricity and minimize gear eccentricities during rotation.
7. Noise and Vibration Testing:
- Noise and vibration testing can help identify potential issues related to gear meshing, tooth contact, and dynamic behavior. These tests ensure the gears meet noise and vibration standards for specific applications.
8. Endurance and Load Testing:
- Endurance and load testing are conducted to assess the gears’ performance under real-world conditions. This involves applying various loads and stresses to simulate the gear’s operational life and performance.
9. Quality Management Systems:
- Implementing a comprehensive quality management system, such as ISO 9001, helps ensure consistent and controlled production processes. This includes documentation, traceability, and process control to maintain product quality.
By employing these manufacturing techniques and quality assurance practices, gear manufacturers can produce high-quality helical gears that meet strict performance and reliability standards, ensuring their suitability for a wide range of industrial applications.