In the process of helical gear meshing, the humidity of helical gear surface is composed of ambient temperature, helical gear body temperature and instantaneous temperature of meshing contact area. At high speed and load, the instantaneous temperature rise at the meshing point is very high. Gou Xiangfeng et al. Studied the influence of tooth surface temperature on helical gear motion during helical gear meshing in 2015, and deduced the relationship between helical gear temperature and time during helical gear motion. In 2011, Ma et al. Studied the sensitivity of different gear materials to temperature under low cycle fatigue conditions, fitted the correlation of transition life and summarized the formula describing the cyclic stress response law. Tankecheng et al. Carburized tlvw4220 helical gear steel under different humidity, analyzed the morphology of carbon content and metal metallographic structure of helical gear steel under different temperatures, obtained the carburization amount at various temperatures, and finally obtained the best carburization temperature.
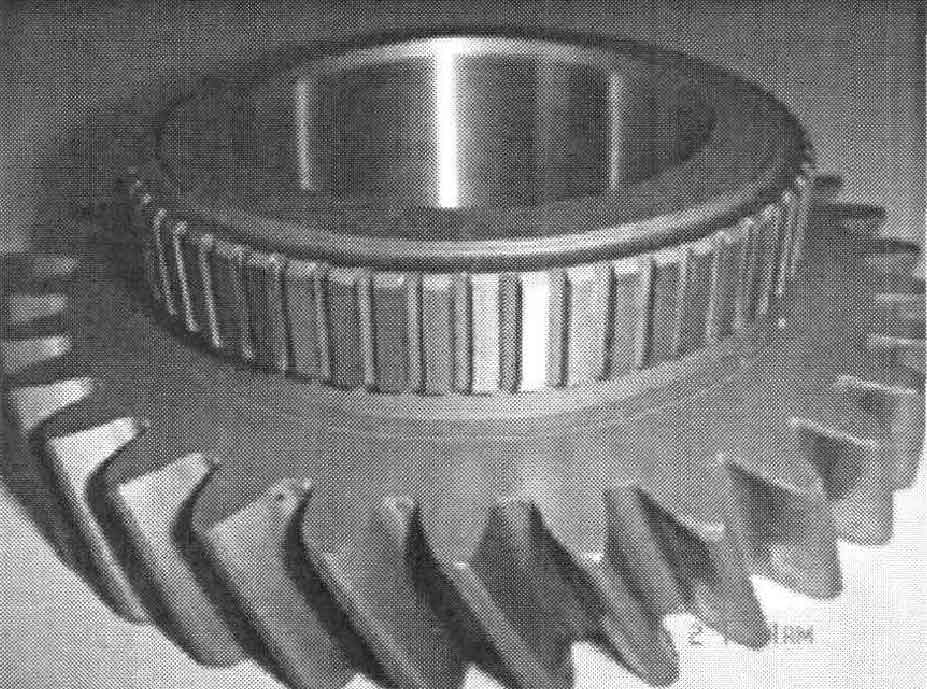
Similarly, the temperature optimization design of helical gears has also been paid attention by scholars. Qixiankun et al. Used the finite element analysis technology to simulate and analyze the helical gear box in 2015, and obtained the temperature distribution law and heating deformation of the helical gear box. The model proposed by him can be applied to complex and heavy-duty occasions, It has a certain guiding role in solving the problem of large heat output of traditional helical gear boxes. In 1995, Deng et al. Used the experimental method to study the influence of helical gear speed and slip conditions on the helical gear temperature field, and obtained some empirical formulas, which enriched the research field of helical gears. In 2006, changenet et al. Believed that the power of the automobile transmission was related to the temperature of the automobile body. In the experiment, the automobile manual transmission was taken as the main research object. Considering that the heat was mainly generated by friction, which occurred between the gear teeth, between the bearings and during lubrication and stirring, It is suggested that the energy loss is related to the temperature rise caused by various friction. Taburdagitan et al. Used the finite element method in 2006 to improve the level of parametric modeling. Compared with their predecessors, the mesh quality and effectiveness have been greatly improved. In their research direction, they also have a more prominent understanding of the humidity change during contact of cylindrical gears in important theory.
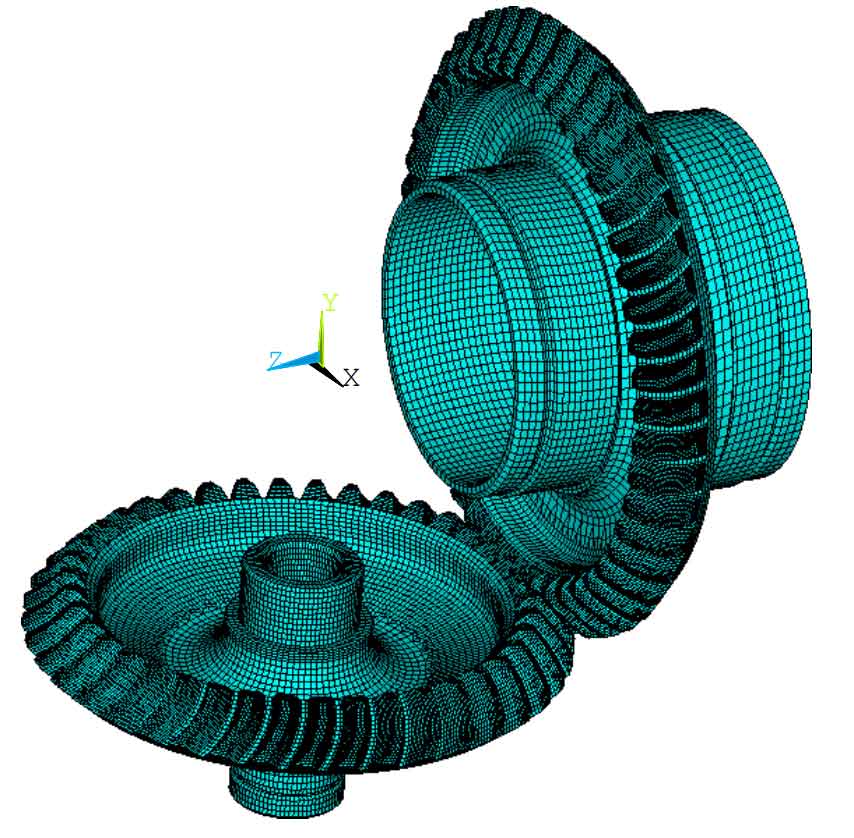
Domestic scholars have also done a lot of research on the temperature field of helical gear transmission. In 1995, qiuliangheng and others recognized the theoretical idea that humidity will inevitably lead to deformation. They modified the helical gear deformed by heating, simulated the temperature by finite element method, studied the temperature distribution of helical gear, and finally determined the relationship between them after many modifications and simulation calculations, It provides a good theoretical basis for tooth modification in the field of thermal deformation. In 1998, wuchanglin, Yu Lianqing and others took a certain automobile gearbox as the research object. Among them, the bearing and gear are the most important parts of the automobile. The researchers focused on the simulation analysis of this part, and the temperature field of this part of the parts was calculated. In 2000, zhangyonghong et al. Used the thermal network method to study the steady-state temperature field distribution of transmission system components for the main transmission system of helicopters, and made important contributions to the thermal stress analysis and transient temperature field analysis of system components. In 2004, ligui believed that the temperature and thermal deformation of helical gear were closely related, and the thermal deformation further affected the shape of helical gear, that is, changing the curve equation. It was concluded that the actual curve equation of helical gear was not completely consistent with the designer’s calculation equation, and the reason was the thermal deformation caused by the change of temperature. The research results of xiaowangqiang et al. In their paper in 2006 show that the temperature sensitivity of asymmetric gears is different from that of symmetric gears. Asymmetric gears are superior in this respect. Therefore, when gears with strong anti scuffing ability are required, asymmetric gears can be selected. In 2009, cuixinwei and others also conducted a systematic study on the anti scuffing problem of gears. He selected the heavy planetary gears and applied relatively large stress. Like his predecessors, the temperature distribution was mainly considered. He modified the helical gears and then analyzed the temperature field. He studied the scuffing problem from the aspect of tooth direction modification and put forward a profound understanding for the study of this problem.