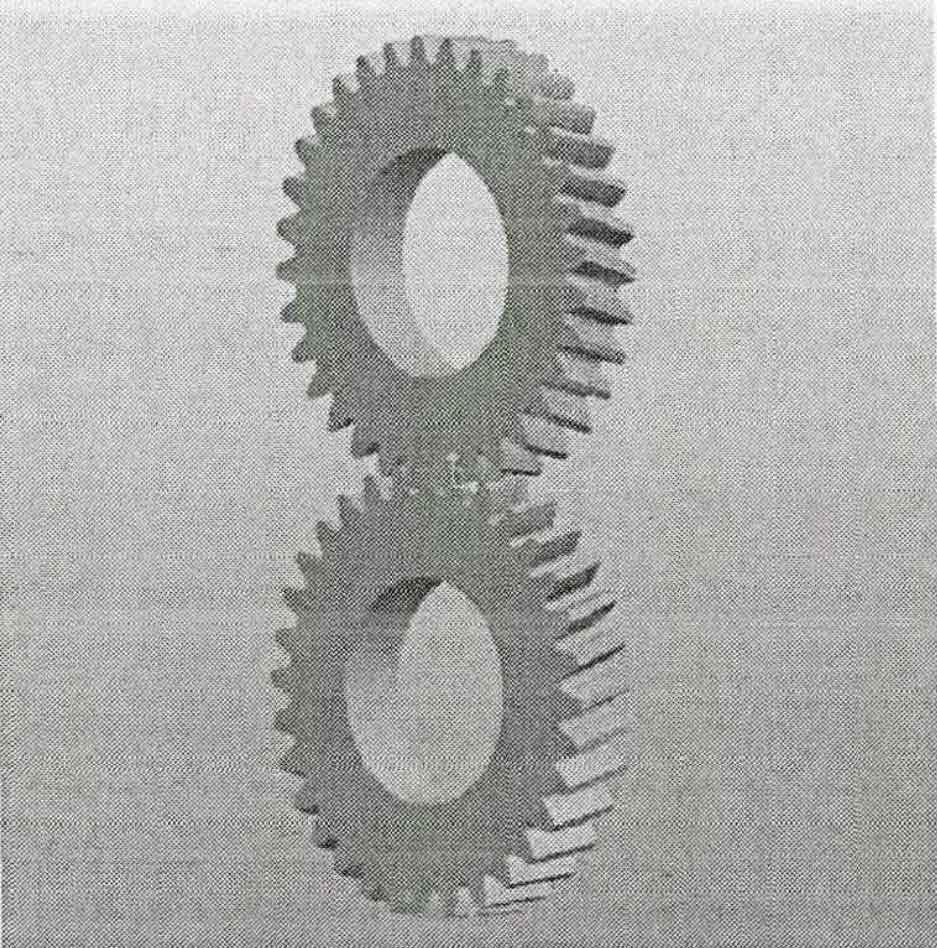
(1) This paper breaks through the condition limitation of calculating the time-varying contact line length of helical gear multi tooth meshing, establishes an algorithm for calculating the time-varying contact line length of external meshing of various helical gears such as wide helical teeth, high helical teeth and spur gears, studies and reveals the condition that the total length of time-varying contact line changes the least, and provides a theoretical basis for gear parameter design and optimizing time-varying meshing stiffness to reduce gear vibration.
(2) Considering the friction effect of gears under mixed elastohydrodynamic lubrication, a fast algorithm of helical gear tooth surface friction and tooth surface friction torque is established by using the slice spur gear method, which reveals the variation law of tooth surface friction and tooth surface friction torque, providing a scientific basis for engineering application.
(3) The influence law of tooth friction on the meshing deformation and time-varying meshing stiffness of helical gears is revealed. There is a large deformation mutation at the nodes. The time-varying meshing stiffness of helical gears is larger when the tooth friction is considered than when it is not considered.
(4) The dynamic equation of Helical Gear Considering tooth friction and its multi-scale solution method are established, and the influence of dynamic and static loads on harmonic resonance response is revealed.
(5) This paper reveals the variation law of helical gear transmission error when considering the overall error and tooth surface friction, and the influence law of gear accuracy grade reflected by base pitch error, tooth pitch error and tooth profile error on vibration and noise in the meshing impact caused by transmission error.