Introduction to Helical Gears:
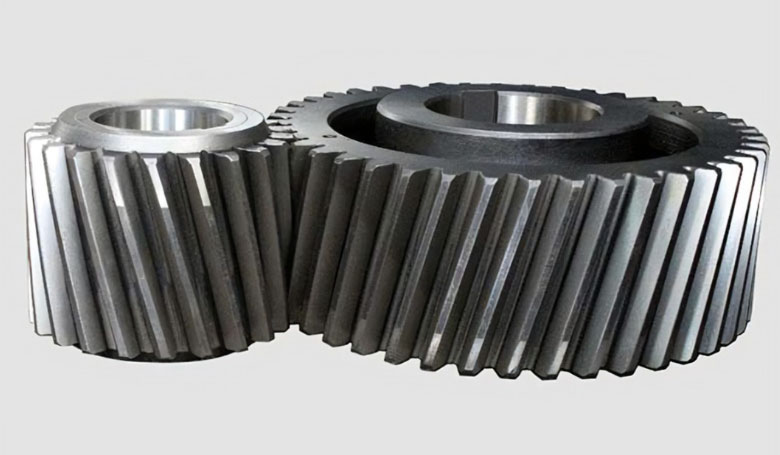
Helical gears are a type of mechanical gear with helical teeth that resemble the shape of a helix. These gears are widely used in various industrial applications, including automotive transmissions, industrial machinery, and robotics. Helical gears offer several advantages over other gear types, such as smoother and quieter operation, higher load-carrying capacity, and improved efficiency. In this comprehensive guide, we will explore the design, function, advantages, and applications of helical gears.
1. Helical Gear Design:
- Helix Angle: The helix angle is the angle between the gear’s axis and the tangent to the helix at any point on the tooth profile. It determines the direction of helix and affects the gear’s axial thrust and efficiency.
- Module: The module represents the size of the gear tooth. It is the ratio of the pitch diameter to the number of teeth. The module determines the gear’s dimensions and pitch circle diameter.
- Pressure Angle: The pressure angle is the angle between the line of action (the common tangent) and the line perpendicular to the tooth profile. It affects the gear’s strength and performance.
- Profile Shift: Profile shift involves modifying the tooth profile to optimize the gear’s performance, including noise reduction, load capacity, and contact ratio.
2. Helical Gear Function:
- Power Transmission: Helical gears transfer power and motion between parallel or intersecting shafts. The helical teeth mesh gradually, reducing the impact forces and noise compared to spur gears.
- Speed Reduction/Increase: Helical gears can be used to reduce or increase rotational speed by changing the gear ratio. They are commonly employed in gearboxes to achieve various speed requirements.
3. Advantages of Helical Gears:
- Smooth Operation: The gradual engagement of helical teeth results in smoother and quieter operation, reducing vibration and noise.
- High Load-Carrying Capacity: Helical gears can transmit higher loads due to multiple teeth being engaged simultaneously, distributing the load across more teeth.
- Efficiency: The continuous tooth engagement of helical gears reduces sliding friction, resulting in higher gear efficiency compared to spur gears.
- Less Wear: The rolling contact of helical gears minimizes tooth wear, leading to longer gear life.
4. Applications of Helical Gears:
- Automotive Transmissions: Helical gears are commonly used in automotive manual and automatic transmissions for efficient power transfer and smooth gear shifting.
- Industrial Machinery: Helical gears are employed in various industrial machines, including conveyors, machine tools, and printing presses, for reliable power transmission.
- Robotics: Helical gears are utilized in robotic systems to achieve precise motion control and reduce noise during movement.
- Power Generation: Helical gears are found in power generation equipment like turbines and generators for efficient energy transfer.
- Marine Applications: Helical gears are used in marine propulsion systems for reliable and smooth power transmission.
Helical gears have proven to be a versatile and essential gear type in a wide range of applications. Their unique design and function make them ideal for various industries, where efficiency, quiet operation, and high load-carrying capacity are paramount.