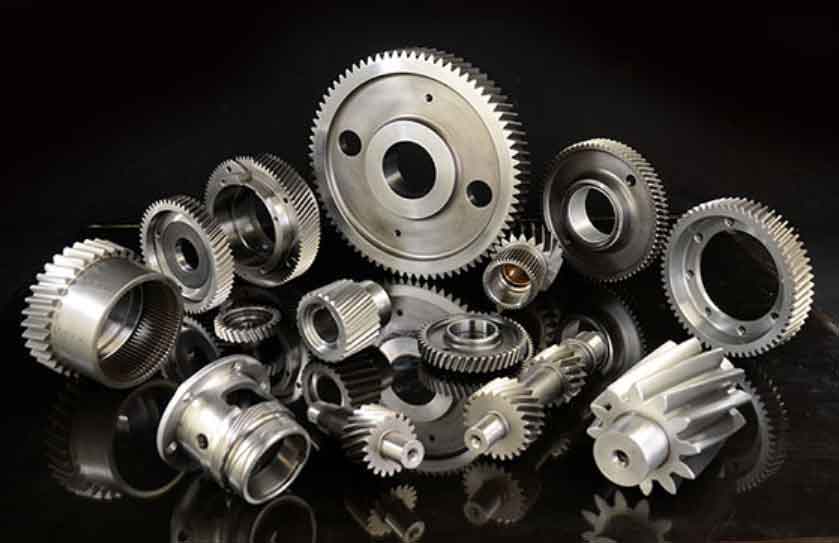
Helical gears are a type of mechanical gearing system used to transmit rotational motion and power between two shafts. They belong to the family of cylindrical gears and have tooth elements that are oriented at an angle to the gear axis, unlike spur gears, where the teeth are parallel to the axis.
Function:
The primary function of helical gears is to transmit rotational motion and torque smoothly and efficiently between two parallel shafts. The helical design provides several advantages over spur gears, including reduced noise, smoother operation, and increased load-carrying capacity. The angled teeth gradually engage, resulting in a gradual transfer of force, reducing impact and vibration.
Design and Characteristics:
- Helix Angle: The helix angle is the angle formed between the gear axis and an element of the helix (a line traced along the tooth surface). It is the key parameter that defines a helical gear. The angle can vary from a few degrees to almost 90 degrees, but typically it ranges from 15 to 45 degrees.
- Lead: The lead of a helical gear is the axial distance traveled by the gear tooth in one complete revolution. It is equal to the pitch times the number of teeth.
- Contact Ratio: Helical gears have a higher contact ratio compared to spur gears. The contact ratio is the ratio of the average number of teeth in contact to the number of teeth transmitting force. A higher contact ratio results in smoother and quieter operation.
- Load Distribution: The angled teeth allow for more tooth engagement at any given time, distributing the load across multiple teeth. This increases the load-carrying capacity and reduces wear on individual teeth.
- Axial Thrust: Helical gears generate axial thrust due to the helix angle. This thrust needs to be accommodated using thrust bearings or by balancing it with an equal and opposite thrust from a neighboring gear.
- Efficiency: Helical gears have slightly lower efficiency compared to spur gears due to the sliding contact of the teeth. However, this efficiency loss is relatively small and is outweighed by their other advantages in most applications.
- Lubrication: Proper lubrication is crucial for helical gears to operate efficiently and minimize wear. Due to the sliding action, they require adequate lubrication to reduce friction and heat generation.
Applications:
Helical gears find wide applications in various industries, including automotive, industrial machinery, marine, and power transmission systems. They are commonly used in gearboxes, where the change in speed and torque between the engine and wheels is required. Their smooth and quiet operation makes them suitable for high-speed applications.
In conclusion, helical gears are an essential component in many mechanical systems due to their efficiency, load-carrying capacity, and smooth operation. Their design considerations involve helix angle, lead, contact ratio, axial thrust, and proper lubrication to ensure reliable and efficient performance.