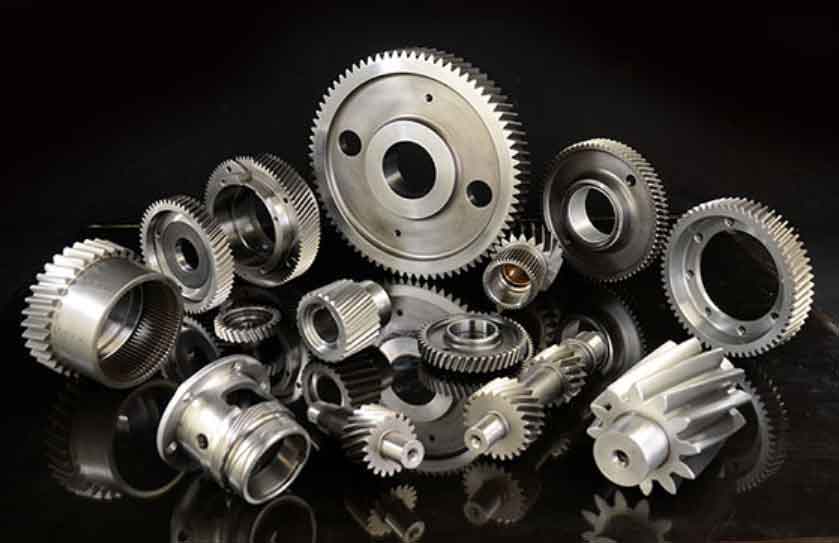
Helical gears are a type of mechanical power transmission system that uses helical teeth to transfer rotational motion and torque between parallel shafts. They are one of the most commonly used types of gears in various industrial applications due to their numerous advantages, including smoother operation, higher load-carrying capacity, and reduced noise compared to spur gears. Let’s explore the key aspects of helical gears in-depth:
1. Helical Gear Tooth Profile:
Unlike spur gears with straight teeth, helical gears have teeth with a helix angle. The helix angle creates a gradual engagement and disengagement of the gear teeth, resulting in smoother and quieter operation. The helix angle is typically expressed in degrees and can vary depending on the specific application.
2. Advantages of Helical Gears:
- Smooth and Quiet Operation: The gradual tooth engagement reduces impact and vibration, resulting in quieter gear operation.
- High Load-Carrying Capacity: The helical tooth design distributes the load across multiple teeth, allowing helical gears to handle higher loads compared to spur gears of similar size.
- Efficiency: Helical gears have higher efficiency due to reduced sliding contact between teeth during meshing.
- Parallel Shaft Configuration: Helical gears are used to transmit motion and power between parallel shafts, making them suitable for many applications.
- Overlapping Teeth: Helical gears have overlapping teeth, which improves the meshing contact area and reduces wear.
3. Helix Angle Direction:
Helical gears can have right-hand or left-hand helix angles. In right-hand helical gears, the helix angles of both gears are the same, and their teeth curve in the same direction. In left-hand helical gears, the helix angles are also the same, but their teeth curve in opposite directions.
4. Axial Thrust and Thrust Bearings:
Due to the helix angle, helical gears generate an axial thrust force along the shafts. This thrust force needs to be properly managed, and thrust bearings are often used to counteract the axial forces and maintain proper gear alignment.
5. Helical Gear Applications:
- Automotive Transmissions: Helical gears are commonly used in automotive transmissions to provide smooth gear shifts and efficient power transfer.
- Industrial Gearboxes: They are extensively used in various industrial machinery, such as pumps, compressors, and conveyor systems.
- Robotics: Helical gears are employed in robotic systems for precision motion control and efficient power transmission.
- Marine Applications: Helical gears are used in marine propulsion systems for smoother and quieter operation.
6. Helical Gear Manufacturing:
Helical gears can be manufactured using various methods, including hobbing, shaping, and milling. Hobbing is the most common method for mass production of helical gears due to its efficiency and precision.
7. Helical Gear Noise Reduction:
While helical gears are generally quieter than spur gears, they can still produce some noise due to the sliding contact between teeth. Noise reduction techniques, such as gear tooth profile modifications, gear coatings, and proper gear alignment, can further minimize noise.
Helical gears are a fundamental component of modern mechanical engineering, offering a reliable and efficient solution for transmitting power and motion in a wide range of applications. Their versatility, load-carrying capacity, and smooth operation make them indispensable in various industries.