In high-speed applications, helical gears are commonly used due to their ability to transmit power efficiently and smoothly. However, handling dynamic loads in such applications can be a challenge. Here are some considerations for handling dynamic loads in helical gears used in high-speed applications:
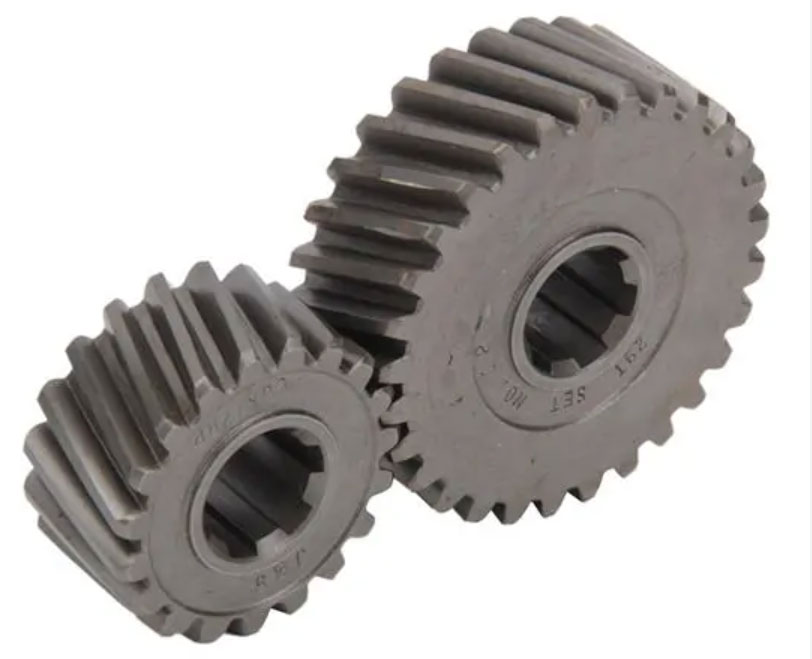
- Gear Design: Optimal gear design is crucial to handle dynamic loads. The gear teeth should be designed with appropriate pressure angles, helix angles, and tooth profiles to ensure smooth engagement and minimize dynamic loads during operation. High-quality gear materials with good fatigue resistance and hardness are typically selected.
- Load Distribution: Proper load distribution among gear teeth is essential to minimize localized stresses. This can be achieved by using multiple gear pairs or gear stages to share the load, resulting in reduced dynamic loads on each gear pair. The gear system should be designed to evenly distribute the load across the teeth.
- Lubrication and Cooling: Adequate lubrication is critical to reduce friction and wear between gear teeth. Lubricating oils with high film strength and viscosity are typically used in high-speed applications. Additionally, efficient cooling systems should be implemented to dissipate heat generated during operation, as high temperatures can affect the performance and durability of the gears.
- Alignment and Mounting: Precise alignment of gears is essential to minimize dynamic loads and ensure proper meshing. Misalignment can lead to increased vibration, noise, and accelerated wear. Careful attention should be given to the alignment and mounting of gears during installation and maintenance.
- Dynamic Load Analysis: Conducting dynamic load analysis using computer-aided design (CAD) and simulation tools can help identify potential areas of concern and optimize gear design. Finite element analysis (FEA) can be used to evaluate stress distribution, deformation, and fatigue life of the gears under dynamic loads, aiding in the design improvement process.
- Material Selection: Choosing the right material for the gears is crucial for handling dynamic loads. High-strength alloy steels, such as carburizing steels or nitriding steels, are commonly used for their excellent fatigue resistance and load-carrying capacity. Advanced materials like powder metallurgy steels or composite materials can also be considered for specific high-speed applications.
- Maintenance and Inspection: Regular maintenance and inspection of the gear system are important to detect any potential issues early on. This includes monitoring gear wear, checking for tooth damage or pitting, and ensuring proper lubrication. Timely maintenance can help prevent catastrophic failures and extend the lifespan of the gears.
Overall, handling dynamic loads in helical gears used in high-speed applications requires careful design, proper load distribution, effective lubrication, and maintenance practices. It is important to consult with experts in gear design and manufacturing to ensure the best performance and reliability of the gear system.