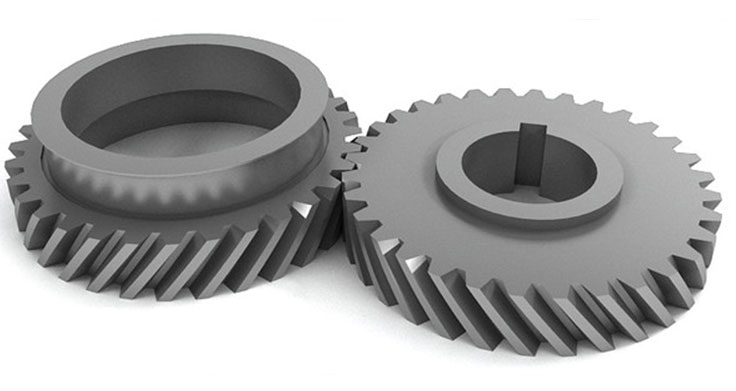
Helical gears play a significant role in marine propulsion systems, providing the necessary power transmission and torque conversion required for efficient vessel propulsion. While they offer various advantages, helical gears also face some unique challenges in the marine environment. Let’s explore both the challenges and advantages of using helical gears in marine propulsion systems:
Challenges:
- Corrosion and Seawater Exposure: The marine environment exposes gears to corrosive seawater, which can accelerate wear and reduce gear life. Proper material selection and corrosion-resistant coatings are essential to mitigate this challenge.
- Vibration and Shock Loads: Marine propulsion systems are subject to significant vibration and shock loads due to the vessel’s movement in water. Helical gears must be designed to handle these dynamic loads without failure.
- Noise Generation: Helical gears are generally quieter than spur gears, but noise reduction remains essential for maintaining crew comfort and reducing underwater noise pollution that can disturb marine life.
- Lubrication and Contamination: Proper lubrication is critical to prevent wear and overheating in the marine environment. However, the risk of lubricant contamination with seawater and debris must be carefully managed.
- Space Constraints: Space limitations in marine propulsion systems can impact gear design and arrangement, requiring compact and efficient gearboxes.
- Alignment and Installation: Proper alignment during gear installation is crucial to avoid premature wear and ensure efficient power transmission.
Advantages:
- Smooth and Efficient Power Transmission: Helical gears offer smooth and continuous tooth engagement, resulting in efficient power transmission and reduced noise compared to spur gears.
- High Torque Transmission: Helical gears have a higher torque capacity than other gear types, making them well-suited for marine propulsion systems that require high power output.
- Load Distribution: The helix angle in helical gears allows multiple teeth to be in contact simultaneously, distributing the load evenly across the gear teeth for improved load-carrying capacity.
- Customizable Gear Ratios: Helical gears can achieve a wide range of gear ratios, allowing marine propulsion systems to operate efficiently at different speeds and under varying load conditions.
- Reduced Tooth Impact: The gradual tooth engagement of helical gears minimizes impact forces during gear meshing, reducing wear and extending gear life.
- Enhanced Efficiency: Helical gears’ ability to transmit power with minimal energy losses contributes to improved overall propulsion system efficiency.
- Durability and Reliability: Properly designed and manufactured helical gears, along with appropriate material selection, offer durability and reliability in the demanding marine environment.
- Versatility: Helical gears can be used in various marine propulsion systems, including diesel engines, gas turbines, and electric propulsion systems.
- Reduced Noise and Vibration: While noise reduction is still essential, helical gears are generally quieter than spur gears, contributing to a more comfortable onboard environment.
To optimize the performance of helical gears in marine propulsion systems, manufacturers need to consider the challenges and implement proper material selection, gear design, lubrication, and maintenance practices. With careful engineering and adherence to best practices, helical gears can provide efficient and reliable power transmission in marine applications, contributing to the overall efficiency and performance of the vessel.