Abstract
This paper proposes a novel high-precision detection method for the transmission error of double circular arc spiral bevel gears. The transmission error in double circular arc spiral bevel gears is complex and nonlinear due to tooth pitch deviation and other factors. This complexity affects the contact stress and elastic deformation of the tooth surface, leading to edge contact and distortion of the gear coordinate system. To address these issues, we establish a transmission error analysis model and analyze the effects of torque, installation, and manufacturing factors using the control variable method. Subsequently, we transform the detected tooth profiles into the theoretical tooth profile coordinate system and employ the normal equidistant line of the theoretical tooth profile to establish a transmission error search model. Experimental results demonstrate that the proposed method achieves highly reliable and precise transmission error detection results under various load conditions.
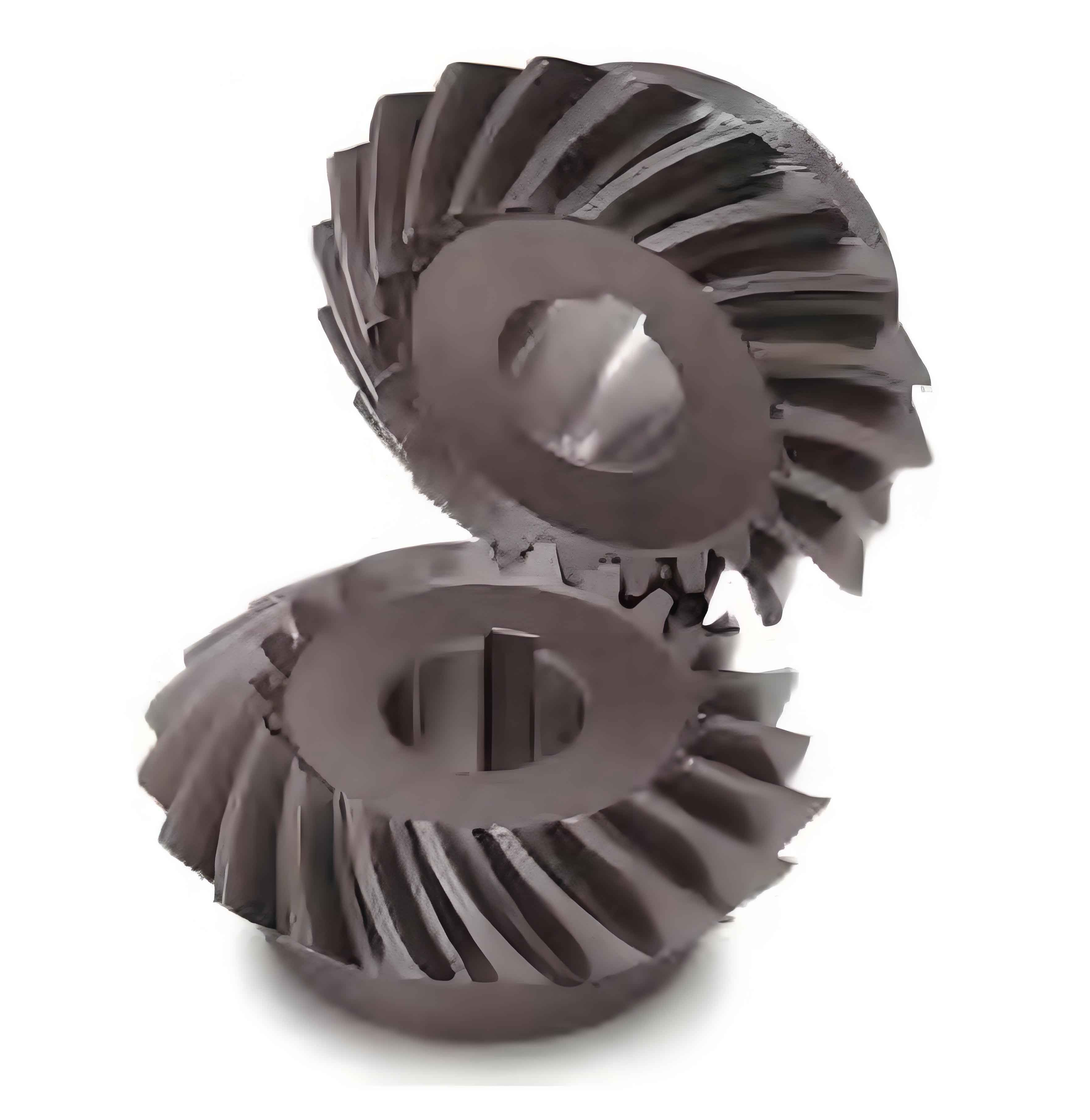
1. Introduction
Double circular arc spiral bevel gears are widely used in various industries, such as aerospace and automotive, due to their high accuracy and efficiency. However, errors in the transmission of these gears can significantly impact the precision and efficiency of mechanical systems. Consequently, accurate detection of transmission errors in double circular arc spiral bevel gears is crucial.
Previous research has explored various methods for error detection in spiral bevel gears. Some studies have utilized structured light scanning for depth feature acquisition, while others have employed coordinate transformations and optimization algorithms to correct position errors. However, these methods often suffer from limitations such as incomplete image acquisition, inaccurate gain coefficient adjustment, and parameter setting issues.
To overcome these limitations, this paper proposes a novel high-precision detection method for transmission errors in double circular arc spiral bevel gears. The proposed method integrates control variable analysis, coordinate transformation, and normal equidistant line techniques to achieve reliable and precise error detection.
2. Methodology
2.1 Establishment of Spiral Bevel Gear Coordinate System
The transmission error in spiral bevel gears refers to minor oscillations or changes in the gear tooth orientation during low-speed rotation. Due to the unique design and structure of double circular arc spiral bevel gears, edge contact can occur, leading to high contact stress and elastic deformation, which distort the gear coordinate system and amplify transmission errors.
To understand the generation and propagation of transmission errors, we establish a coordinate system for the spiral bevel gears. The key factors influencing transmission errors are analyzed, including tooth surface contact stress and elastic deformation.
The mathematical model of the gear coordinate system is given by:
begin{split} x &= g \cdot \exp(\sin(2\pi kZ\theta)) \cdot \cos(\theta) \\ y &= g \cdot \exp(\sin(2\pi kZ\theta)) \cdot \sin(\theta) end{split}
where:
- g is the tooth alignment error,
- k is the torque influence factor,
- Z is the number of teeth,
- θ is the angular position,
- and other symbols represent standard trigonometric and exponential functions.
2.2 High-Precision Transmission Error Detection
The transmission system of spiral bevel gears is complex and dynamic. By establishing a gear coordinate system, we can compare and analyze errors between the actual and theoretical gear geometries. This approach allows for accurate measurement and analysis of transmission errors.
The proposed detection method consists of the following steps:
- Theoretical Tooth Profile Extraction: Utilize the gear coordinate system to extract the theoretical tooth profile.
- Normal Equidistant Line Search: Obtain two equidistant tooth profiles that encompass the actual tooth points using the normal equidistant line technique.
- Transmission Error Model: Develop a transmission error search model based on the tooth profile equations.
The transmission error f can be expressed as:
f=fmeasured−ftheoretical
where fmeasured is the measured transmission error, and ftheoretical is the theoretical value calculated from the gear coordinate system.
3. Experimental Analysis
3.1 Experimental Setup
To validate the proposed method, experiments were conducted using MMSA spiral bevel gears. The experimental setup included a drive motor, gearbox, sensors, and a control system.
Table 1: Basic Parameters of the MMSA Spiral Bevel Gears
Parameter | Value |
---|---|
Tooth Width (mm) | 20 |
Outline Diameter (mm) | 17 |
Outline Length (mm) | 8.5 |
Pitch Cone Angle (Outer) (°) | 125 |
Pitch Cone Angle (Inner) (°) | 52 |
Cone Distance (Outer) (mm) | 80 |
Helix Angle (°) | 30 |
Transmission Angle (°) | 10 |
3.2 Tooth Profile Data Sampling and Precision Analysis
High-precision tooth profile data is crucial for accurate error detection. Sampling was conducted at three stages: initial contact, stable operation, and degradation.
The precision analysis shows that the initial contact stage has the highest sampling precision, while the stable operation stage has acceptable precision within tolerances. During the degradation stage, regular calibration ensures stable sampling precision.
3.3 Transmission Error Analysis under Rated Load
Under rated load conditions, the proposed method was compared with existing methods.
The proposed method closely matches the true error values, indicating its high precision.
3.4 Transmission Error Analysis under Varying Loads
To further validate the method, experiments were conducted under varying loads.
As load increases, the transmission error also increases. The proposed method consistently outperforms existing methods, demonstrating its robustness.
3.5 Cross-Arc Distance Error Analysis
Cross-arc distance errors were measured to assess detection precision.
The proposed method shows a high fit with the true values, indicating superior precision.
4. Discussion
The proposed method achieves high-precision transmission error detection in double circular arc spiral bevel gears. By integrating control variable analysis, coordinate transformation, and normal equidistant line techniques, the method effectively addresses the complexities associated with tooth pitch deviation and elastic deformation.
The experimental results confirm that the proposed method outperforms existing techniques, particularly under varying load conditions. The cross-arc distance error analysis further validates the precision and reliability of the method.
5. Conclusion
This paper presents a novel high-precision detection method for transmission errors in double circular arc spiral bevel gears. By establishing a gear coordinate system and utilizing the normal equidistant line technique, the method accurately detects transmission errors under various conditions. Experimental results demonstrate the superiority of the proposed method over existing techniques, indicating its potential for widespread application in precision mechanical systems.
Future research could focus on refining the model parameters and extending the method to other types of gears. Additionally, real-time error detection and compensation systems could be developed based on the proposed technique.