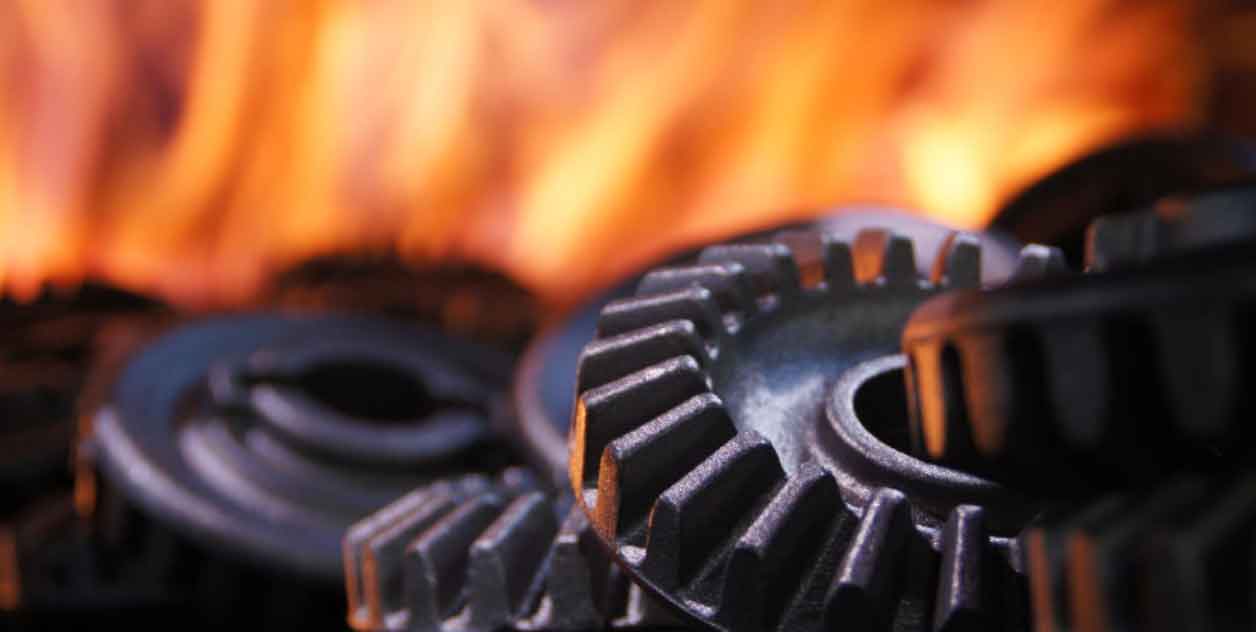
Accurate gear tooth profiles are crucial for smooth and efficient gear operation. Gear forgings play a vital role in ensuring precise gear tooth profiles, which are essential for proper gear meshing and optimized performance. This article highlights the significance of gear forgings in achieving accurate gear tooth profiles and explores the techniques employed to ensure precision in gear manufacturing.
I. Importance of Accurate Gear Tooth Profiles:
Accurate gear tooth profiles are vital for several reasons:
- Proper Gear Meshing: Precise gear tooth profiles enable proper engagement and meshing between mating gears. Proper gear meshing ensures efficient power transmission, reduces wear and friction, and minimizes noise and vibration.
- Load Distribution: Accurate tooth profiles facilitate uniform load distribution across the gear teeth. This ensures that the load is evenly distributed, reducing stress concentrations and the risk of premature tooth failure.
- Contact Ratio: The contact ratio, which measures the number of teeth in contact at any given time, affects gear performance. Accurate tooth profiles help optimize the contact ratio, ensuring sufficient tooth contact and minimizing the risk of tooth surface fatigue.
- Efficiency: Accurate gear tooth profiles contribute to higher gear system efficiency by minimizing power losses due to friction, heat generation, and backlash.
II. Precision in Gear Forging Process:
Gear forgings employ various techniques to achieve precise gear tooth profiles:
- Die Design and Precision Tooling: The die design and precision tooling used in gear forging play a critical role in shaping the gear tooth profiles accurately. Computer-aided design (CAD) and computer-aided manufacturing (CAM) technologies are utilized to create intricate die cavities that precisely replicate the desired tooth geometry.
- Controlled Deformation: Gear forgings involve the controlled deformation of metal billets under high pressure and temperature. This controlled deformation allows for precise shaping of the tooth profile, ensuring that the final gear matches the intended design specifications.
- Closed-Die Forging: Closed-die forging, also known as impression-die forging, is commonly employed in gear manufacturing. In this process, the metal billet is placed between two dies, and the pressure is applied to shape the material into the desired gear tooth profile. The dies are carefully designed to ensure accurate replication of the tooth geometry.
- Precision Machining: While gear forgings aim to achieve near-net shape configurations, some final machining operations may be necessary to achieve the desired gear tooth profiles. CNC machining or other precision machining techniques can be employed to refine the tooth profile, ensuring precise dimensions and surface finish.
III. Advantages of Gear Forgings in Achieving Accurate Tooth Profiles:
Gear forgings offer several advantages in achieving accurate gear tooth profiles:
- Material Flow Control: The forging process allows for precise control over the flow of the metal during deformation. This control ensures that the material is evenly distributed throughout the die cavity, resulting in accurate gear tooth profiles.
- Grain Structure Refinement: The controlled deformation and thermal cycles during gear forging refine the grain structure of the metal. This refined grain structure contributes to uniform material properties, minimizing the risk of surface irregularities and enhancing the accuracy of the gear tooth profiles.
- Reduced Machining Requirements: Gear forgings aim to achieve near-net shape configurations, minimizing the need for extensive machining. This reduces the chances of dimensional errors during machining and ensures that the final gear tooth profiles closely match the intended design.
- Design Flexibility: Gear forgings offer design flexibility, allowing for the creation of complex gear tooth profiles with precision. This flexibility enables gear designers to optimize gear performance for specific applications and achieve accurate tooth profiles that meet the desired performance criteria.
Accurate gear tooth profiles are vital for optimal gear system performance. Gear forgings, through their die design, controlled deformation, and precision machining techniques, ensure the precision and accuracy of gear tooth profiles. By utilizing gear forgings, manufacturers can achieve gear systems with proper gear meshing, uniform load distribution, and enhanced overall efficiency. The combination of advanced forging processes and meticulous attention to detail ensures the forging precision necessary for accurate gear tooth profiles.